Mar 10, 2021 | Blog
Do you want to monetize your brand? Do you want to engage your audience through real, non-digital means? Are you ready to become the InfluentrepreneurTM (Influencer + Entrepreneur) you were always meant to be?
Today, more and more influencers use private labelling – selling pre-made products under your own branding – to earn revenue and provide followers with a high-quality product that they can trust, because it’s yours!
As an influencer, you already have an online audience. And if you currently promote products on your page, then you also have a solid base of people who rely on your product recommendations. With this, becoming a CEO is as easy as:
- Pick a good product
- Apply your logo and brand
- Choose a shipping provider
- Sell your products online
There are many success stories from influencers turned CEOs, like our adorable canine friend Humphrey and his owner’s brand, Spotted by Humphrey. And companies like inKLOUT exist to help influencers design and market their own products.
But if you’re among the brave souls that want to tackle this journey yourself, this how-to guide will break down each of the three steps (especially the complicated logistics-side of things) to get you on your way to becoming CEO of your own e-commerce brand.
4 Steps to Become an Influencer + Entrepreneur
The private labelling business is very straightforward. You pick a product from a manufacturer, you brand the product, you sell the product, and you get the product to the customer’s doorstep.
You may have heard the term Dropshipping before, but this simply means that the manufacturer handles the final step for you and ships the product to your customers. We’ll get into this later on in Step 3…
So let’s get into the four steps to start your very own e-commerce private label business.
Step 1: Pick a Good Product
The most important thing to do when starting a private label business is to ask yourself the important questions, like:
- Why do people follow you?
- What is your passion or niche?
- What are your peers selling?
Answers to these questions will help you pick a product that is relevant to your personal image and content.
The search begins. Depending on your theme or category, whether it’s fashion, beauty, wellness, etc., you want to search for trending products in your personal domain, or products that you personally use and believe in.
Avoid over-saturated items. You want to stay ahead of trends, not lag behind them. Whatever product you choose, make sure that there isn’t too much competition. Typically, products that have a smaller amount of reviews (<1,000) on Amazon or on the private label manufacturer website are good candidates, as long as they are high quality.
Pick Your Manufacturer. Search on sites like Thomasnet, Alibaba, AliExpress or Google. Simply type “*your product* private label” and see the list of results. Be sure to ask about cost of goods, shipping cost, and turnaround time for any order.
Here is a list of Private Label manufacturers based on category. And as mentioned earlier, companies like inKLOUT can help you design or select a product for your brand.
Note: Most manufacturers do only use cashier’s check or a money wire for payment.
Step 2: Apply Your Logo and Brand
Your company now needs a name, a logo, a product label, and a slogan. This is your opportunity to tell your story, so have some fun with it.
Company Name
It’s important to select a name that resonates with your brand and with your audience. It’s equally important to make sure the name you choose isn’t already taken, because you will want to be able to trademark your name for a site domain and social media.
Shopify has a Business Name Generator that you can use to search for and create your perfect business name.
Company Logo
When you think of logos, what comes to mind? The Nike Swoosh? The McDonald’s Golden Arches? Right from the start, these companies knew that a thoughtful logo has a huge impact on your audience.
If you already have a great idea for your logo, sketch it out! Then, if you aren’t already a master at Photoshop, consider using a Graphic Designer to create a digital copy of your logo. We also recommend using a professional because you will need multiple image sizes for product labels, social media, website, and more.
Graphic Designers can also help you brainstorm ideas for a logo if you don’t already have one. Sites like 99designs, Fiverr, and Upwork have loads of freelance Graphic Designers that can help you create your logo.
Product Label
Typically, the private labelling manufacturer creates the product label for you, once they have your company logo and name. Given the manufacturer, you can customize the labelling as much or as little as you’d like, so be sure to ask about the manufacturer’s capabilities during your search.
Company Slogan
“Just Do It.”– Nike
“I’m Lovin’ It.” — McDonald’s
“We Throw in Extra Parts to Mess With You” — Ikea (not really)
Your slogan is your one sentence summary of your company and your brand. It should be something to grab your audience’s attention and showcase your company.
Step 3: Choose a Shipping Provider
In the most simple terms, you have three options when it comes to shipping.
In-House
The manufacturer sends you the product directly, and you store it in your home … or a warehouse, storage locker or shed. From there, you pack the product in a box/package and use USPS, FedEx or another delivery service to send it to the customer. This is called in-house fulfillment, because you do it entirely by yourself, most likely in your house.
This is the cheapest option, with just an upfront investment for a $200 label printer, but also the most time-consuming and the most difficult to guarantee quality service. Not to mention, you are responsible for handling product returns.
Keep in mind you are competing with brands that offer 2-day shipping and free returns. And when you start to sell a lot of products, you may find it hard to grow your business while spending all your time putting your products in boxes and taking trips to the post office.
Outsource
A company will store the product in their large network of warehouses and will ship the products on your behalf. For a set per-item fee, an eCommerce fulfillment company like ShipHero can help you deliver within two days, help you handle returns, and help you manage inventory.
Fulfillment-by-Amazon (FBA) is a popular example of outsourced fulfillment because you send your product to their warehouse, and for a per-item fee, Amazon will deliver your products.
Dropshipping
The factory/wholesaler will also pack and ship it directly to your customer, bypassing you entirely. This allows business owners to take a hands-off approach to the operation of their business, and customer satisfaction lies entirely in the hands of the manufacturer.
As a cheap and convenient option, dropshipping also results in lower profit margins, longer shipping times, and less control over your business. But CEOs that want to have a more hands-off approach will choose dropshipping for the minimum involvement required.
Step 4: Sell Your Product Online
With a fully-branded product and a shipping method in place, all that’s left to do is sell.
Whether you want to spread your products to everyone or keep it exclusive is up to you and your brand. You can sign up for Instagram Shopping to post a New Catalog of your products, or you can connect to your website. Instagram allows integrations with Shopify, BigCommerce, Magento and WooCommerce.
Besides your social media channels, you can sell on platforms like Shopify and Amazon to reach a large audience, but Shopify lets you design your own website and gives you more control to build your brand.
There you have it!
The four steps to becoming brand owner and CEO of your very own eCommerce private label company. ShipHero created this influencer how-to guide to help you on your entrepreneurial journey, because ShipHero’s mission is to help businesses deliver their eCommerce.
We’ve shipped over $5 billion orders to date. Each day, more and more businesses are signing up with ShipHero to receive 2-day shipping, return handling and the eco-friendly shipping option with priority ground shipping.
Aug 6, 2021 | Blog, Fulfillment, Warehouse Management Software
By: Aaron Rubin, Founder & CEO of ShipHero
Ecommerce websites are constantly shifting to keep up with buyer expectations. With competition from gigantic online stores such as Amazon, keeping up with ecommerce giants can be tricky. Luckily, there are a few key ecommerce trends that online retailers can look to in order to keep up with the wants of online shoppers.
With the rise of the ecommerce industry, more customers than ever are making purchases online. While brick-and-mortar retailers aren’t dead yet, many of them are seeing their customers flock to online stores. With a rise in ecommerce sales comes ecommerce trends.
Here are the 15 trends to keep in mind to help grow your ecommerce business.
AI helps improve ad campaigns and messaging
Top ecommerce stores are implementing AI and automation to help boost their ad campaigns and messaging across marketing initiatives and social media platforms. Through machine learning and artificial intelligence technology, companies have been able to make hyper-personalized advertising allowing for tailored messaging to customers. Specialized messages can include content specifically targeted at the user’s interests or product recommendations that fit their previous browsing history.
On top of being able to personalize messaging to specific users, AI can track the performance of these campaigns and let marketing leads know how each initiative is performing. By carefully examining you and your competitor’s marketing success, automation can pick out trends from the complex and time-consuming data, something hard for a human to discover manually.
The customer experience must be personalized
While AI is helping us customize our marketing experience for customers, we have to tailor the process from start to finish. For example, when searching through an online marketplace, users are more likely to purchase items they are interested in if they find them through sidebar suggestions based on their browsing habits throughout your site. Personalized product recommendations can help prevent cart abandoners and can help you sell more inventory too!
2-day shipping becomes the norm
Retail giants like Amazon have used their significant logistics network to ensure that 2-day shipping has become the new normal. Longer shipping times, though sometimes tolerated, are not going to be seen as the usual farther into the future. Finding shipping and logistics solutions to keep up with this 2-day expectation is difficult, but it is, unfortunately, a strong trend that will separate some sellers from their competitors. For ecommerce merchants that want to leverage 2-day shipping, consider working with a 3PL.
But customers will be hungry for 1-day and same-day shipping
Big ecommerce sites have made it possible for 1-day and same-day shipping, especially during the boom in online shopping during COVID-19. Customers can easily have food, snacks, household goods, or other products delivered to their homes overnight or even on the same day.
While many smaller companies have trouble keeping up with this high bar, many people have found the convenience of it even better than visiting a brick-and-mortar store to grab an item.
Chatbots improve shopping experiences
Chatbots, often powered by automation, can help guide customers through their shopping experience. By answering frequently asked questions or directing the customer to their desired page, chatbots can help users through any confusion or concerns without taxing your customer support staff. The answers are instant, customizable depending on your preference, and work on multiple devices.
Headless commerce drives innovation
Headless commerce, where the frontend and backend of your website are separated, can help you drive innovation on your site. The flexibility of being able to customize, brand, and play with your customer-facing front end while not harming the utilities within your backend lets companies make more considerable changes without stress or danger.
Separating your front and backend also helps improve customer experience by enhancing the website functionality and speed.
Subscriptions keep customers coming back
Subscriptions create a commitment, whether with SaaS in b2b, or monthly product boxes in b2c. Subscription models keep customers interested in your products and brand.
Even when your subscriptions aren’t your main product line, they can help buyers get connected and familiar with your messaging and quality, making them more likely to open their wallets when looking at your other product lines. Subscriptions are also a regular reminder that your business exists, keeping you at the forefront of a customer’s mind.
Customers want sustainability
With millennials taking up much of the ecommerce buying power, it is crucial to tap into things that often sway them. A Nielsen report has shown that 73% of millennials would pay more for sustainable products. Some examples of industries that benefit from this trend include upcycled products, consignment, and local p2p transactions. Tapping into these markets will require new initiatives and green product lines to appeal to these wants.
Mobile shopping is here to stay
Mobile devices have become more and more prominently used when shopping online, so much so that Insider Intelligence stated that mobile commerce would reach $488.0 billion (44% of ecommerce) by 2024. One-click shopping and easily accessible social commerce ads on apps have driven mobile shopping. In order to tap into the mCommerce market, it will be essential to make sure your website has mobile-friendly shopping or a mobile app.
Gen Z becomes more of a focus
The oldest of the Gen Z era are now in their early 20s, meaning they are quickly becoming more common customers within the ecommerce world. For a generation that has always known the conveniences of ecommerce and online ordering, a smooth customer experience will be vital. Gen Z is more partial to social commerce, meaning Facebook, Pinterest, TikTok, and Instagram are key places to garner their interest.
User-generated content remains key
Influencers have grown in popularity within marketing, especially when selling products through social media sites. Having a trusted celebrity or influencer tout your product can immediately get thousands of eyes on your business and markets much more directly to a group of consumers than SEO or content marketing.
TikTok and Instagram shopping become major sales channels
Both TikTok and Instagram are rising as major sales channels, especially with Gen Z starting to become a larger and larger part of the ecommerce market. Pew Research Center saw that 48% of United States adults between 18-29 years old use TikTok, a number that falls dramatically to 20% in the 30-49 age range. When marketing to younger consumers, both TikTok and Instagram will be a vital piece of the puzzle.
With Instagram and TikTok investing significantly in commerce capabilities, ordering directly from these apps is going to become much easier.
Brick-and-mortar retailers aren’t dead
Score saw that 55% of those who do online shopping prefer to buy from stores with a physical location rather than an online-only shop. Being able to do returns, try on clothes in the store, or see products in person is still valuable to consumers. You shouldn’t overlook the advantages of a brick-and-mortar location, especially in specific sectors such as apparel.
Buy Now Pay Later gains more traction
Buy Now Pay Later has become a wildly popular payment method for consumers. Services like Affirm, Sezzle, and Klarna make it easy for customers to make purchases on installment payments. Shopify has implemented the option natively with Shop Pay.
Apple Pay is launching a similar service. Having these installment-like payment options helps those without credit cards finance payments and creates accessibility for many shoppers. Having flexibility in payment systems also means that customers can make big-ticket item purchases that they may not have entertained otherwise.
The checkout experience must be easy and simple
Many platforms such as Shopify have made the checkout experience extremely smooth. Ensuring an easy and painless checkout can prevent cart abandonment and improve the crucial last parts of the customer experience. Poor checkout experiences are also more common on mobile devices, so make sure this process is simple across all of your platforms!
How ShipHero grows ecommerce businesses
Are you worried about keeping up with these ecommerce trends? ShipHero can help. Our software connects with your warehouse, outsourced shipping processes, and 3PLs to help you deliver your ecommerce. We help you elevate your experience through:
Fast shipping speeds
ShipHero offers standard, expedited, and overnight shipping so that you can keep up with top ecommerce retailers like Amazon and Walmart. We facilitate fast shipping without the hassle and frustration. ShipHero has no hidden fees, and we help you find the cheapest overnight options to save money.
Multi-channel fulfillment
Our software can help you handle your order fulfillment through a nationwide network of warehouses. By creating distributing processes throughout these warehouses, delivery delays are minimized, and orders arrive at your customers quicker. Multi-channel fulfillment allows us to offer overnight and 2-day shipping without the worry.
Easy returns management
Returns happen. When managed correctly, they can help you grow your sales and create repeat customers. Through built-in self-service options for your customers and easy label printing through connected shipping accounts, returns become simple for customers.
Conclusion
Keeping up with ecommerce trends is crucial to staying on top of the competition. From AI and chatbots to a heavier social commerce presence, adapting to the new normals can help you stay relevant and bring in new audiences. To give yourself an edge, implement technology and software such as ShipHero to help facilitate faster shipping and smoother fulfillment processes.
Schedule a meeting today with our experts to learn more about our WMS software built for ecommerce brands & 3PLs looking to run their best warehouse and how ShipHero works to ensure that organizations invest in the solutions that match their needs, to improve productivity, revenue, and success.
Click HERE to Schedule a Meeting Today
Aaron Rubin, Founder & CEO
ShipHero
About the author: Aaron Rubin is the Founder & CEO of ShipHero. He is responsible for planning and executing the overall vision and strategy of the organization. Rubin’s greatest strengths are leadership, change management, strategic planning and a passion for progression. He is known for having his finger on the pulse of ShipHero’s major initiatives, his entrepreneurial spirit, and keen business acumen. His leadership of ShipHero is grounded in providing excellent customer service that drives improved business operations. His passion for ShipHero comes from the culture and his ability to have an impact on the lives of employees, customers, partners, and investors.
Follow Aaron on Twitter & LinkedIn.
Apr 21, 2023 | Blog
The modern business landscape is in a constant state of evolution. Commerce is rapidly advancing, and the global environment is undergoing changes. Businesses must adapt to meet shifting market demands, stakeholder needs, and even customer service expectations.
Even if your own supply chain network is currently operating efficiently, the need to adapt remains as customer preferences, market dynamics, and global changes evolve. This comprehensive guide explores 10 actionable steps to enhance supply chain efficiency, ensuring your own business model remains agile and a competitive advantage.
Understanding Supply Chain Efficiency
Efficiency within the supply chain revolves around optimal utilization of technology, resources, and expertise. By improving this supply chain efficiency today, businesses can reduce logistics costs, manage risks, and enhance profits.
This component is integral to the operations of any company striving for growth and increased profitability. Efficient logistics processes, information management, and order processing are critical aspects. Optimizing these business processes can lead to improved stock management and better handling of returns.
Why Prioritize Efficiency in Supply Chains?
Efficiency in the supply chain focuses on achieving cost savings while ensuring customer satisfaction. An efficient supply chain strategy enables businesses to meet customer demands without inflating their operational costs and expenses.
It streamlines order processing, fulfillment, and delivery, ensuring timely access to goods and services. This effort enhances the customer experience and satisfaction and caters to market needs. Effective logistics and marketing strategies further make logistics companies enhance and improve supply chain efficiency, particularly in ensuring goods reach their destinations efficiently.
Balancing Efficiency with Effectiveness
Striking a balance between supply chain efficiency and effectiveness is crucial. While supply chain efficiency often focuses on cost-effective delivery, effectiveness ensures top-quality products that meet customer expectations.
Excessive focus on efficiency might compromise customer satisfaction, while over-prioritizing effectiveness can escalate shipping and logistics costs. Achieving balance involves understanding market needs and making changes accordingly.
Risk Management in Supply Chains
Efficient supply chain management is essential for businesses to navigate the complexities of today’s global markets. One of the key challenges that all supply chain depends and chains face is the management of various risks that can disrupt operations and impact profitability.
These risks can stem from factors such as natural disasters, geopolitical tensions, supplier disruptions, and even unexpected shifts in consumer demand. Risk management in supply chains involves identifying potential risks, assessing their potential impact, and developing contingency plans to ensure that the supply chain can continue to function smoothly even in the face of challenges.
Collaborative relationships with suppliers, diversification of sourcing, and the utilization of real-time monitoring technologies are crucial components of a robust risk management strategy.
Technology Trends in Supply Chain Management
In today’s rapidly evolving business landscape, technology has become a driving force behind the optimization of supply chain management. Emerging technologies such as blockchain, the Internet of Things (IoT), artificial intelligence (AI), and machine learning are transforming how supply chains operate.
Blockchain ensures secure and transparent data sharing across the supply chain, IoT devices provide real-time tracking and monitoring capabilities, while AI and machine learning algorithms enhance demand forecasting accuracy and optimize inventory management.
These technological trends empower businesses to make data-driven decisions, automate processes, and enhance overall efficiency and responsiveness in their supply chain operations.
Reverse Logistics and Product Returns
Efficiently managing the process of product returns, often referred to as reverse logistics, is a crucial aspect of maintaining a well-functioning supply chain. With the rise of e-commerce and changing consumer expectations, handling returned items has become increasingly complex.
Implementing streamlined processes for returns authorization, refurbishment, and responsible disposal of products is essential for minimizing waste and ensuring that returned items are properly managed.
Effective reverse logistics not only contributes to customer satisfaction but also supports sustainable and efficient supply chain and operations by minimizing environmental impact and optimizing resource utilization.
Customer-Centric Supply Chains
The modern business landscape places significant emphasis on delivering exceptional customer experiences. This has led to a shift towards customer-centric supply chain strategies. To meet the demands of today’s consumers, supply chains must prioritize customization and personalization.
Leveraging data-driven insights, businesses can anticipate customer preferences, reduce lead times, and ensure on-time deliveries. Agility and data analytics play a pivotal role in aligning supply chain operations with customer expectations, enabling businesses to create memorable experiences and foster lasting customer relationships.
E-Commerce and Last-Mile Delivery
The rapid growth of e-commerce has revolutionized supply chain dynamics and highlighted the critical importance of efficient last-mile delivery. Last-mile delivery refers to the final leg of the delivery journey, from distribution centers to customers’ doorsteps.
Optimizing last-mile delivery is crucial for customer satisfaction and loyalty. Strategies such as optimizing delivery routes, implementing innovative technologies like drones and autonomous vehicles, and establishing partnerships with local service providers all contribute to enhancing the efficiency of last-mile delivery.
Additionally, the creation of micro-fulfillment centers can further streamline the process and improve delivery speed.
Supply Chain Digitization and Data Analytics
The digitization of supply chain processes and the utilization of data analytics are reshaping how supply chains operate. Data-driven insights provide valuable information for demand forecasting, inventory management, and process optimization.
Predictive analytics enable businesses to anticipate trends and make informed decisions. Embracing digital transformation empowers supply chain managers to proactively identify areas for improvement, enhance visibility, and respond rapidly to changing market conditions.
This shift towards supply chain digitization is a crucial step in ensuring that businesses remain competitive and adaptable in today’s fast-paced business environment.
Collaborative Partnerships: Igniting Innovation and Efficiency
Forge robust partnerships to amplify and improve your own measure supply chain efficiency and resilience. Collaborate with suppliers, manufacturers, distributors, and retailers for co-innovation and streamlined operations. Share insights, tackle challenges together, and create an ecosystem that adapts and thrives.
Supplier Performance Metrics: Elevate Excellence
Assess suppliers using key performance indicators and metrics like on-time delivery and quality. Leverage data for improvement, risk assessment, and optimized collaboration. Regular reviews cultivate continuous enhancement.
Inventory Optimization: Efficient and Cost-effective
Master inventory management with dynamic safety stock calculation and advanced modeling. Prevent stockouts and excess inventory, enhancing availability while reducing costs.
Talent Development: Nurturing Expertise
Foster a skilled workforce through training, certifications, and continuous learning. Empower employees with problem-solving and leadership skills, driving innovation and growth.
Supply Chain Transparency: Consumer Trust Advantage
Embrace transparency with ethical practices and responsible sourcing. Convey values to modern consumers, building trust, enhancing reputation, and gaining a competitive edge.
10 Ways to Improve Supply Chain Efficiency
1. Enhance Supply Chain Visibility:
Achieving comprehensive visibility across your customer relationship management and entire supply chain and processes ensures timely decision-making and efficient planning. This transparency allows businesses to promptly address bottlenecks and other challenges, ensuring smooth operations.
- Address bottlenecks and challenges promptly.
- Facilitate efficient planning.
2. Foster Strong Supplier Relationships:
Building and maintaining robust relationships with suppliers and partners in responsive supply chain activities is pivotal. Regular communication and setting clear expectations can lead to long-term partnerships, ensuring timely deliveries and more efficiency strategies meeting customer demands.
- Ensure clear communication and expectations.
- Ensure timely deliveries and meet customer demands.
3. Mitigate Supply Risks with Data Management:
Monitoring supplier performance and ensuring their adherence to industry standards can prevent unforeseen regulatory challenges. Proper data management and a supply chain visibility strategy can also help in sourcing and manufacturing planning.
- Prevent unforeseen regulatory challenges.
- Facilitate sourcing and manufacturing planning.
4. Optimize Delivery Times Across Markets:
Efficiently catering to both established and emerging markets ensures a balanced growth trajectory for businesses. It’s essential to control the distribution, supply chain process and transportation aspects to achieve this.
- Efficiently cater to established and emerging markets.
- Control distribution and transportation aspects.
5. Embed Sustainable Practices:
Integrating sustainable practices, such as ethical sourcing and efficient and inventory management processes, can significantly reduce costs and boost supply chain performance and efficiency.
- Boost supply chain efficiency sustainably.
6. Leverage Automation:
Investing in automation, from warehousing to marketing to business processes itself, can streamline operations, increase efficiency, lower costs and enhance efficiency.
- Streamline operations from warehousing to marketing.
- Enhance overall efficiency.
7. Develop a Robust Returns Strategy:
Efficiently managing product returns requires a well-defined reverse logistics strategy, ensuring products are tracked from customers back to suppliers. This process is vital for maintaining customer satisfaction and managing stock and inventory levels well.
- Define a well-structured reverse logistics strategy.
- Maintain customer satisfaction and manage stock levels.
8. Empower Your Team:
Regular training sessions can equip and improve your supply chain staff with the skills needed to enhance and improve your supply chain, performance and efficiency. It’s a step towards ensuring that every part of the company is aligned with the best practices.
- Provide regular training to enhance staff skills.
- Align all parts of the company with best practices.
9. Implement Quality Software Solutions:
Investing in reliable software and systems can significantly improve efficiency in supply chain processes. It’s essential to have a system in place that provides real-time information and data to stakeholders.
- Invest in reliable software for real-time data access.
- Improve supply chain processes.
10. Commit to Continuous Improvement:
Regularly reviewing and refining supply chain management processes ensures sustained growth and increased efficiency. It’s about adapting to changes in the environment, understanding the next customer demand, improving supply chain efficiency and ensuring customer satisfaction. Continuous effort in this place can yield significant results over time.
- Regularly review and refine processes.
- Adapt to environmental changes and market demands.
Metrics to Gauge Supply Chain Efficiency
Measuring and improving supply chain efficiency involves using inventory data and assessing key metrics that provide insights into various aspects of your operations.
These metrics help you identify responsive supply chain, strengths, weaknesses, and areas for improvement and streamlined operations, ensuring that your supply chain remains responsive and competitive. Here are some essential metrics to consider:
Time
Swift order processing and delivery times are crucial for meeting customer expectations and ensuring timely access to goods and services. Shorter lead times can lead to improved customer satisfaction and increased sales.
Cost reduction
Balancing logistics costs with profit margins is essential for profitability. Monitoring your transportation costs, warehousing, and inventory carrying costs can help you optimize spending while maintaining service quality.
Quality
Maintaining high-quality standards in your products is vital for customer retention and sales growth. Monitoring product quality throughout the full supply chain process, from sourcing to delivery, can help you identify areas for improvement.
By regularly monitoring these metrics, you can gain a holistic view of your whole supply chain, track your inventory levels and network’s performance and make informed decisions to enhance efficiency and drive better results.
Key Takeaways
- Supply chain efficiency focuses on cost-effective, quality delivery.
- Balance efficiency and effectiveness for optimal results.
- Quality software solutions like ShipHero enhance efficiency.
FAQs on Supply Chain Efficiencies
1. What exemplifies business efficiency?
Efficiency involves producing more products swiftly and at reduced costs.
2. What are the advantages of supply chain efficiency?
Benefits include time and resource management and cost savings, leading to maximum efficiency and increased profits.
3. How can one assess supply chain efficiency?
Measure time, cost raw materials, and resources associated with product production and delivery.
By implementing these insights, businesses can navigate complex supply chain landscapes, ensuring growth and profitability.
Regularly reviewing logistics and other various supply chain management processes keeps businesses agile and delivers exceptional products and services to customers consistently. This effort results in a well-functioning machine that thrives regardless of challenges.

Feb 10, 2023 | Blog, Fulfillment, Warehouse Management Software
With the popularity of subscription services on the rise, it’s no surprise that eCommerce businesses are looking into this innovative and convenient model. But just how much can subscriptions improve customer retention? In this blog post, we’ll delve deeper into the benefits of subscription models and explore how these strategies can bolster user engagement, drive business success, and increase overall customer satisfaction. Bid farewell to your old approaches to customer retention — there’s a new modern solution in town!
What is a Subscription Business Model, and How Does it Work?
Subscription business models have taken over the economy. Instead of paying a hefty one-time fee upfront, subscription business models have conditioned customers to buy in and pay multiple payments spread throughout the year. This means subscription businesses can focus on customer retention rather than acquisition, leading to longer lifetime values (LTVs) per customer. Rather than ownership of physical goods or services, subscribing has flipped the script and ushered in a new wave of subscription-oriented lifestyle choices.
Types of Subscription Models
The Curation Model
The curation model is one of the most popular subscription services, with boxes tailored to every person’s personal needs and preferences. From beauty sets to cheese boards – whatever your vice is, there’s a subscription box for it. The curated approach is what sets this model apart from the other types of subscriptions available; it offers customers an ever-changing and exciting selection of products that are all unique to their tastes!
Example:
The Birchbox subscription service sends monthly subscription boxes containing two to six beauty products from more than 200 brands. Personalized boxes are sent based on a quiz, and the same product is never sent twice. Customers can purchase the full-size product directly from the website, improving retention and LTV.
The Replenishment Model
Replenishment subscription models often referred to as “subscribe and save,” are an increasingly popular option for busy people who wish never to run out of toilet paper or coffee pods again. This type of eCommerce establishes a recurring revenue model and ensures customers receive their purchases at predetermined intervals, allowing retailers to confidently and accurately predict inventory needs. If you sell everyday consumables, embracing this subscription strategy could give you a competitive edge.
Example:
Subscribers to Dollar Shave Club receive blades and shaving products regularly based on their needs. After completing the initial quiz, the customer can customize the suggested box to include the products they want. Customizing these specific features is the key difference from a curation model.
The Access Model
Access-focused subscriptions offer familiar customers exclusive discounts, early access, and more. Access models are all the rage in fashion and food verticals but can also be found among digital subscription brands. A subscription model allows you to benefit financially and insight into future forecasting, but it’s also a great way to show your valued customers some love. When customers feel special, their loyalty toward your brand is likely to increase.
Example:
Clearly, streaming media subscriptions, such as Netflix, are here to stay. Just having the ability to access unlimited shows and movies whenever you want is a fantastic perk and a great example of the access model in action! This model allows viewers to enjoy extra features like no commercials or early access to their favorite shows by signing up for more exclusive paid services.
Benefits of Subscription Models in Business
- Subscription models are convenient for customers.
- Customers can discover new products.
- Businesses can accurately predict revenue.
- Subscriptions can attract more customers.
- Subscriptions decrease customer acquisition costs.
- Businesses build stronger relationships with their customers.
Subscription Retention Strategies
Tracking what content subscribers engage with is a great way to determine what people are interested in and whether you’re hitting the mark with your content. By observing which stories they’re clicking on and products they’re talking about, you can determine which topics will be the most successful. On top of that, you can better tailor the content that runs in the future to suit their tastes. Getting this right is essential if you want to keep your subscribers engaged and coming back for more!
Welcome new subscribers and make sure they’re aware of their subscription’s benefits! An effective onboarding process will ensure that your subscribers are connected to your brand and understand the value of their subscription. When it’s time for them to decide whether to renew, you can be sure that they are already invested in the product and that their decision is easy. Subscribers will appreciate a great welcome, and you’ll be on your way to building a long-term relationship with them.
Encourage existing subscribers to renew by optimizing customer service and actively engaging with your current subscriber base. Doing this will build personal relationships with them and lay the foundation for a long-term relationship. At the end of their subscription, you’ll be able to have meaningful conversations that remind your subscribers of the great value they’ve already experienced from your service, which makes it much easier for them to hit “renew” when the time comes.
Reduce subscriber churn by knowing which of your subscribers are most likely to cancel. You can get ahead of potential cancellations by using data-driven insights to identify these high-risk customers and understand why their intentions may differ from other subscribers. From there, you can build targeted strategies to re-engage them and ensure they stay part of your subscriber base!
Measure and test any initial promotions or offerings. Try creating different discounts with different lengths of offers—this can help identify which works best at drawing in and retaining subscribers. Keep in mind that discounted subscriptions should also include your most engaging content if you want those readers to stick around. So don’t be afraid to experiment with various promotional offers; this is an excellent way to find out what attracts—and keeps—subscribers on board!
Offering exclusive subscriber-only benefits is a great way to increase loyalty and show your customers that you appreciate them. These benefits could range from tailored content, discounts on products or services, early access to new developments—or all of the above! However you choose to structure these offers, they will surely inform your subscribers that you prioritize their business and are committed to providing them with high-quality content and services.
Why Subscription Models are Becoming More Popular
Subscription models have become increasingly popular due to the range of benefits on offer. Price is a significant factor driving customers to subscriptions as companies offer discounts for bulk orders, keeping prices lower than store-bought equivalents. Plus, these companies tend to deliver directly to your door – making them an easy and convenient option too.
On top of that, most subscription services personalize their offerings with tailored deliveries, which add an extra touch and make the customer feel special. All this has ensured that subscriptions are rising in popularity, with reports showing 100% year-over-year growth for the last five years – so hop on board and join the subscription revolution!
Advantages of a Subscription Model to Improve Retention
Subscription models are a revolutionary way of tackling customer retention. With subscriptions, you can strategize the best approaches for creating relationships between you and your customers that extend beyond profit.
Companies can benefit from increased customer engagement and recurring revenue to support their business. When done strategically, big brands can also use their existing assets to launch new initiatives and acquire more subscribers.
Subscriptions also offer customers convenience, security, and reliability of products and services they need regularly. All in all, subscription-based revenue models can be advantageous for both the customers and the companies.
Subscribe to our blog to learn more, or click HERE to schedule a meeting today!
—
Maggie M. Barnett, Esq. COO of ShipHero – Author
About the author: Maggie M. Barnett, Esq., is the COO of ShipHero. She is responsible for planning and executing the overall operational, legal, managerial, and administrative procedures, reporting structures, and operational controls of the organization. Barnett’s greatest strengths are leadership, risk mitigation, change management, and a passion for business transformation. She is known for her expertise in delivering operational excellence and ability to provide guidance and mitigate risk. Her leadership of ShipHero is grounded in a servant mentality, always doing the right thing for our stakeholders. Her passion for ShipHero comes from the ability to drive operational excellence throughout the organization impacting the lives of our employees, customers, and partners.
Follow Maggie on Twitter & LinkedIn.
Apr 13, 2021 | Blog, The Packet
The Rise of E-Crime
This week, hackers released a database of personal data on over 533 million Facebook users, including emails, phone numbers and more (You can check to see if you were part of the leak here). Security experts say that this information has been available on dark-web for a while, and this recent “leak” is just a large accumulation of previously leaked data.
Am I in trouble?
Because this information is not new to hackers on the dark web, you may not experience an increase in theft attempts to you as a person; however, this large, aggregated leak is a treasure trove for hackers and cyber criminals hoping to steal from e-commerce companies.
Oh dang.
In 2020 alone, Sift estimates that more than $1 trillion was lost globally due to cybercrime. According to the same report, 62% of all payment fraud took place on a mobile device, and 45% of the U.S. e-commerce market was conducted on mobile devices in 2020. The perps mainly used ransom-ware attacks (taking control of a company’s systems and extorting them for money) or by using email-delivered malware to learn passwords and siphon funds.
Who are they targeting?
Transportation was the top targeted vertical, with reports of coordinated efforts to steal food/liquor deliveries in broad daylight. Also, loyalty businesses was the top targeted industry with a 275% increase in fraud attempts.
Where does this money go?
Video games mostly… actually. The top item purchased by cybercriminals is video game currency, followed by cryptocurrencies and site credits.
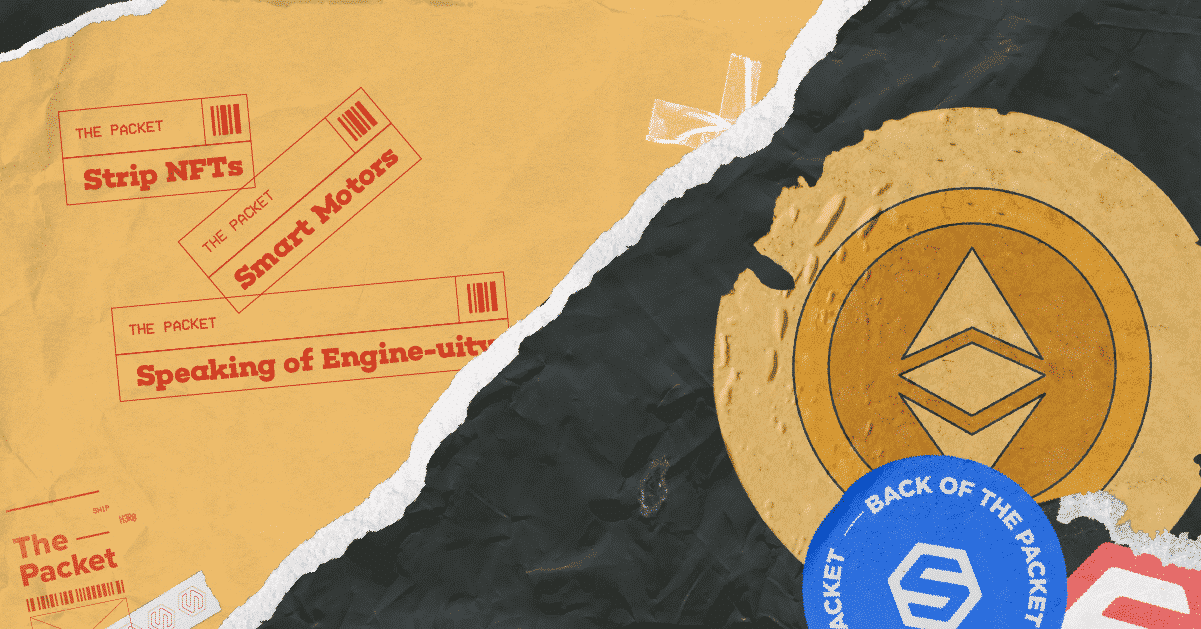
Strip NFTs
After 83 years, the major-league trading card company, Topps, announced plans to go public in a SPAC merger valued at $1.3B. The recent NFT-craze allows Topps to link collectibles to digital tokens, then receive payouts through Smart Contracts for the second-hand market sales — like the Mickey Mantle card that just sold for $5 million (which Topps made a whopping $.05 on over 70 years ago). Beyond sports, Topps has forged partnerships with Marvel and Star Wars to branch into the collectibles market.
Smart Motors
Turntide Technologies says it’s able to use recent advances in machine learning, software and electronics to create highly efficient motors that greatly cut carbon emissions. Buildings owned by BMW, JLL and Five guys, as well as cooling systems on dairy farms, already use this smart motor to reduce their carbon footprint, and companies that have retrofitted old motors with this smart motor have cut their HVAC motor energy consumption by 64% on average. If scaled out to replace all motors, Turntide says it could eliminate 25% of global carbon emission.
Speaking of Engine-uity
NASA’s Mars Helicopter, Ingenuity, has survived its first Martian night and is sending miraculous pictures of the Red Planet, which (spoiler) don’t look too red.
ShipHero News
How To Create Content for Your E-commerce Business – Part 1: Video
The very first step to marketing your e-commerce store is simple: content creation. In the world of SEO, social media, and online sales, check out our blog to find out what it takes to create authentic and engaging video content that builds trust with your customer base.
The Fulfillment Innovation Wheel: Data Now
It’s your data, and you need it now! Reporting & Analytics has never been more important to your e-commerce warehouse operations. Find out the KPIs and reports you need to make to stay competitive, in our newest blog for ShipHero’s Fulfillment Innovation Wheel series – Data Now.
Apr 21, 2023 | Blog
Stock-keeping units (SKUs) are essential for retailers. They let you track inventory quantity and stock movements without having to do physical checks every day.
But what do SKUs really do, and how do you make them? Read on for a comprehensive guide on SKUs!
What Is a Stock Keeping Unit (SKU)?
A stock-keeping unit (SKU) is an alphanumeric code assigned to each of your products. They usually come in the form of scannable barcodes printed on labels. An SKU usually contains the product’s details like its price, variant, size and more.
Each product variant has a unique SKU. So, for example, you have purple and yellow T-shirts in three sizes each: small, medium and large. Each variant of these T-shirts has its own SKU, meaning you have six SKUs.
Why do you need unique SKUs for each variant? This is to prevent mix-ups during the picking process. If an SKU only registers the color, your picker might retrieve T-shirts of the wrong size.
Why Are SKUs Important?
SKUs are important for stock tracking and sales data collecting. Tracking the movement of SKUs alongside customer orders means you know what products are selling and which variants are most popular. This way, you can anticipate high demand by stocking up on popular items.
SKUs are also often used for product recommendations in online stores. Let’s say a customer puts an action movie DVD in their cart. Your system can search for similar SKUs and recommend them to other action movies. This might trigger an extra purchase and increase your profits.
Stock Keeping Units (SKU) vs Universal Product Codes (UPC)
SKUs and UPCs are used for similar things. They both track inventory and stock levels. But there’s one key difference.
SKUs are retailer-specific. Even if two companies sell identical items, the SKUs will be different. Meanwhile, UPCs are universal, as the name implies. The same product will have the same UPCs across all retailers.
SKUs are more flexible than UPCs because they can either be printed in text or as a barcode. Meanwhile, UPCs can only be printed as a barcode. This means humans can easily read SKUs, while UPCs need a barcode scanner.
How Do You Create SKU Numbers?
You can create SKU numbers by splitting an alphanumeric string into different parts and defining each of them. Let’s take a look at the steps to create a SKU number:
- Make a top-level identifier: The first two or three digits of an SKU are a general classification of the product. These categories can be anything. Some examples include the product’s type, brand, manufacturer and department.
- Define a unique identifier: The middle part of the SKU is usually for unique identifiers like the item’s size, material and color.
- Finish with a sequential number: The last bit of the SKU is usually a sequential number that shows when it arrived in your warehouse. This means you won’t have a hard time calculating stock. Sequential numbers also help you prioritize selling items that have been in the warehouse longer.
- Input the SKUs into your inventory management system or point-of-sale: Manually managing hundreds or thousands of SKUs is extremely hard. That’s why the next step is to input your SKU in a database provided by your point-of-sale (POS) or inventory management system.
- Print SKU barcodes: Your POS system will convert the SKU numbers into barcodes. Print them and attach them with labels to your products.
What does an SKU number look like? Here’s an example SKU for an item sold at a clothing retail store:
Here’s the code broken down:
- JK: Jacket
- S01: Style 01
- YL: Yellow
- S: Small
- 001: First product at the warehouse
As you can see, the SKU system defines everything about the item to its most minute details. By reading the code, a picker can tell it’s a small yellow Style 01 jacket. They can also tell this is the first jacket of that type in the warehouse. From this information, they can send out the right item when a customer orders it.
Top 5 Uses of SKUs for Business
Now that we’ve learned what SKUs are and how to make them, it’s time to learn their uses. There are five major uses of SKUs in businesses.
1. Analysis
SKUs can track which items are selling and which ones aren’t. This helps you anticipate customer demand by purchasing more or less of certain products.
You can use SKU tracking data to predict which items might be top sellers so you can order more and maximize revenue. Conversely, you can reduce orders on items that aren’t selling well to prevent overstocking. Keeping inventory levels manageable also lets you save money on storage space.
SKUs don’t just give you insight into inventory. You can glean some behavioral insights, like learning which items are often bought together. This way, you can consider selling them as a package to further drive sales.
2. Inventory Management
SKU barcodes make inventory management easier through real-time tracking. As products arrive and leave your warehouse, your staff will scan their barcodes. This lets you monitor the stock levels of each item you have, even if you have multiple fulfillment centers.
More advanced warehouse management systems will even alert you when items are low in stock. By setting reorder points, you can prevent your most popular products from running out of stock. This prevents customers from shopping from other stores if something isn’t available.
3. Customer Assistance
SKUs organize your products so your warehouse team can easily find them. This means they can pick and pack goods faster, decreasing customer wait time. Faster deliveries mean happier consumers. This is especially important if you promise two-day delivery for your products.
4. Advertising and Marketing
Some eCommerce retailers use SKUs when advertising their products. They use this to ensure customers view the items they’re selling.
SKUs also work as an anti-poaching measure. When you promote a product based on its SKU, competitors can’t easily see which products you’re promoting because SKUs aren’t usually public. This makes customer poaching with lower prices and discounts tougher.
5. Product Recommendations
SKUs categorize items to make product recommendations easier. Your eCommerce platform can upsell or cross-sell other products to your customers based on what items they have in the cart.
Product recommendations usually show up on the checkout page just before people get their credit cards out. It can also “save” a sale by recommending similar products when the product a customer wants is out of stock.
Key Takeaways
SKUs don’t just help your pickers retrieve the right items. You can use SKU information for a variety of purposes, like behavioral analytics, demand prediction and product recommendations.
However, managing hundreds of SKU codes isn’t easy. You might need inventory management software to reliably handle all of them.
SKU FAQs
Is a barcode an SKU?
A barcode isn’t an SKU by itself. A SKU can be converted into a barcode, but barcodes can contain a variety of information.
What makes a good SKU?
A good SKU needs to contain the key details of a product without being overly long. Some essential details to include are size, color, category and order it arrived in the warehouse.
How are SKUs used in eCommerce?
SKUs are used in eCommerce in many different ways. Some of the more popular uses include inventory management, product recommendations and analysis.

Apr 15, 2021 | Best Practices, Blog
Proper inventory management is crucial to building a thriving Shopify store. Statistics from Shopify reveal that sellers accrue almost $2 trillion in costs due to inventory mismanagement. The losses are spread among overstocking, out-of-stock items and preventable returns.
Interestingly, these aren’t the only problems associated with inventory management. Shopify store owners still have to battle missing items, misplaced inventory, wrong product packaging and delivery, among others. If you can establish a solid foundation for tracking inventory on your Shopify store, you’re on your way to building a genuinely agile eCommerce business.
What is Inventory Management?
Inventory management refers to how businesses manage goods as they move along the supply chain. eCommerce inventory control ensures that companies know their products are in stock and are notified when inventory needs to be replenished.
Ultimately, a good inventory management system should minimize costs, satisfy customer demand and help you maintain optimal inventory levels. It should also centralize your data, making it accessible to the appropriate point persons.
Part of stock management is inventory control, which is the process of handling existing inventory, while the former primarily involves forecasting, ordering and receiving goods.
Why is Inventory Management Important?
Inventory management is the key to any eCommerce business’ success. It ensures customer satisfaction, keeps businesses profitable and minimizes operational costs. Other benefits of having an effective inventory management system include the following.
No Spoilage or Dead Inventory
When your inventory moves faster and your product lines stay healthy, you don’t put anything to waste. Regular inventory updates can help you avoid spoilage with perishable goods like food and beverages. Similarly, automatic stock updates can prevent dead stock, which are non-perishable products that are no longer in season.
Early Detection of Low Stocks
Most American retailers without powerful inventory software only have an inventory accuracy level of 65%. The more warehouse locations they have, the more this percentage falls.
Fortunately, perpetual inventory systems inform you of available inventory items in real time, preventing stockouts and missed sale opportunities. Instead of scrambling to increase your stock flow, early stock alerts can remind you to make refills in advance.
Improved Cash Flow
Cash flow shortfall is a persisting problem for businesses without perpetual inventory systems. The best way to increase cash flow is to turn inventory into revenue. When you factor inventory into your business operations, you get insight into how much you can sell and buy at any given time.
Remember, inventory flow can directly impact your future sales. Projecting when you’re about to run out enables business owners to accurately plan and increase sales.
Minimized Warehouse Costs
Efficient inventory counts tell you what items are selling fast and which don’t. You can free warehouse space up and store items that sell more by keeping up with sales volumes.
In addition, you can monitor every single product that doesn’t sell, potentially cutting them out of your inventory. When you stock only what is necessary, you can downsize your warehouse and save on costs.
Improve Shopify Fulfillment Network
By employing effective inventory management methods, you can hasten the fulfillment process. For instance, if you have multiple fulfillment partners, inventory management techniques like distribution ensure that you are close to buyers and can keep customers happy. Doing so also ensures that customer returns are seamless and you can easily re-enter usable inventory into circulation.
What is an Inventory Management System?
Inventory management systems enable users to track inventory quantity and streamline processes from purchasing to end sales. Key features of a stock management system include:
- Barcode scanning
- Detailed reports
- Labeling and documentation
- Purchase and supplier management
- Low stock alerts
- Stock turnover rates
- Bills of material (BoM) management
What is Inventory Management for Shopify Stores?
Inventory management for Shopify stores is the systematic approach to sourcing, storing and tracking your inventory. With a proper inventory management system in place, you’ll have the right stock at the right levels, in the right place, at the right time and at the right price.
Plus, it’ll reflect on your Shopify store listings. That way, you can avoid preventable losses due to out-of-stock items, overstocking and returns, and your brand has a better shot at survival, growth and profitability.
Why Inventory Management Matters for Shopify Stores
Inventory management is crucial to the success of Shopify stores. If you can get this aspect of business right, you’ll reduce overall inventory costs, optimize order fulfillment and position yourself to serve your shoppers better. Below are some of the benefits of proper inventory management:
Accurately Track Inventory and Prevent Stockouts
Shopify store owners understand that meeting customers’ needs is crucial to profitability. If you frequently run into stock management problems like overstocking, out of stock or overselling, you’re likely to have many dissatisfied customers. Ultimately, they would go elsewhere to make a purchase, and you may never see them again.
Better Cash Management and Inventory Accounting
If you have too much stock that you can sell within a reasonable period, you’re leaving your capital idle while wasting precious storage space. Knowing how much product to stock helps minimize the amount of dead stock on your shelves and levels out cash flow.
Improve Multi-Channel Selling and Demand Forecasting
Proper inventory management facilitates seamless selling across multiple marketplaces. For example, suppose you’re selling on Shopify, Amazon, eBay, Etsy and your business website. In that case, you’ll need to stay on top of your stock levels to convey accurate information to customers across these platforms. Inventory management also helps you accurately forecast demand, so you’ll always have what your customers need in stock.
Save Inventory Dollars
Virtually every task involved in inventory management helps you manage your resources efficiently. If you stock the right amount of the right products, you won’t waste inventory dollars on storage space. There’ll also be fewer cases of spoiled or expired inventory since your turnover rate will be optimal. Furthermore, the potential gains of having what your customers need in stock whenever they need it is unquantifiable.
Inventory Transfers
Due to varying demand levels, you may frequently have to transfer inventory from one marketplace to another when selling across multiple channels. If you do not follow the right inventory management practices during the transfers, tracking each channel’s inventory levels gets harder.
Shopify Inventory Management Challenges
Shopify has built-in inventory management software that’s adequate for tracking your inventory and managing sales on Shopify. However, the native Shopify app can’t cater to retailers’ unique needs who sell on multiple channels. Here are three common problems you’re likely to experience with Shopify’s native inventory management solutions:
Products That Don’t Integrate Into Shopify
Shopify has a long list of restricted and prohibited items. If you sell one of these products on other platforms, you’ll be facing a significant challenge with multi-channel inventory management.
Often, the only viable option is to have separate inventories for Shopify and other platforms. This complicates the inventory tracking process and can lead to inaccurate or inconsistent stock levels across the different channels.
Automated Inventory Replenishment
As your SKU library expands, your inventory management process will likely become more complicated, and there’ll be more opportunities for inventory management errors. To prevent these problems, you need inventory management software that automatically replenishes depleted stock from suppliers.
Such a program should recommend order quantities by factoring in your sales volume on Shopify and other channels. Unfortunately, the native Shopify app may be unable to carry out the task effectively.
Functionalities Across Channels
The native Shopify inventory management software does not fully support multi-channel selling. For example, the app cannot estimate all the product variants in your online stores. This information is vital to evaluating the performance of your products on channels other than Shopify.
Phantom Inventory
When your system reports items that don’t exist in your store, you risk creating phantom inventory. Without accurate and powerful reports, your business can become susceptible to errors and shrinkage.
While enterprise resource planning has its advantages, it does come with a steep learning curve, so always brush up on your inventory management tips.
How Do Shopify Merchants Handle Inventory Management?
How you utilize the different types of inventory management will ultimately depend on your business goals, existing systems, retail locations and other requirements. You can implement several strategies when using inventory management for the Shopify app.
FIFO Principle
The first-in, first-out (FIFO) principle prioritizes selling the old stock first, which is an ideal method for retailers that sell perishable goods. To achieve a FIFO system, warehouse management begins from the back, pushing older products to the front.
LIFO Method
Opposite the FIFO method is last-in, first-out or LIFO. This method involves selling your newest stock first, which benefits businesses that want to curb rising prices. While this method will lower taxable income, it will also yield lower profits and can negatively impact your retail business’ bottom line.
Regular Auditing
Facilitating a regular inventory and supplier audit can put the current state of your business into context and pinpoint areas of improvement. There are several ways to keep track of low or excess inventory:
- Physical inventory count: A physical inventory count refers to year-end inventory reporting. Count your stock to pinpoint discrepancies, update accounting and file income tax.
- Spot check: Count products in stock one by one throughout the year to ensure you have enough of that particular item. Spot checking is best for fast-moving items.
On top of physical audits, supplier audits can help identify areas of risk, improve your standards, enhance supplier communication and increase customer satisfaction.
Relationship Management
Relationship management is imperative to adapting quickly, especially if you have more than one retail store location or a thriving online business.
If you have a bad supplier, you could have insufficient inventory or too much of it. The better your relationships, the easier it’ll be to bring up issues with suppliers and resolve them. Keep your suppliers in the loop by letting them know when you’re expecting a sales increase, if you’re experiencing inventory dips or if a specific product is running behind schedule.
Accurate Forecasts
Accurate forecasts are challenging to achieve but not impossible. If you want to ensure you’re stocking the correct inventory, keep an eye on:
- Your average growth rate
- Market trends
- Upcoming deals and promotions
- Predicted ad spend
- Daily, weekly and monthly sales
- Sales comparisons
Noting these metrics can help you make more informed inventory decisions and prevent miscalculation in inventory mean.
What to Look For in a Shopify Inventory Management App
The Shopify App Store boasts numerous third-party inventory management tools that can make up for the native app’s shortcomings. Brands that sell on multiple channels typically layer these inventory apps over Shopify’s inventory management software to deliver the best results.
But how do you know the right app to choose among the scores of available options? Here are the nine inventory management features eCommerce store owners should look for in any app.
Multi-Warehouse and Multi-Channel Functionality
A good inventory management app must be capable of syncing your inventory across all sales channels and fulfillment centers. When you update your inventory, it should reflect in real-time or at most within fifteen minutes.
Order Routing and Automation
The app you want to choose should automatically route orders to the nearest fulfillment center to save on shipping costs. The order routing will be based on inventory availability across fulfillment centers, destination zip code and delivery date. Your inventory management app should direct the order to the warehouse, guaranteeing cost-effective and timely delivery.
Inventory Control Features
You want an app that allows you to adjust the number of units on your listings across channels. The inventory adjustments should reflect in real-time to prevent overselling or processing the payment for an order you cannot fulfill.
Comprehensive Analytics and In-Depth Reporting
You should be able to generate real-time data about stock level, inventory turnover, sales margins, profitability, etc., from your inventory management app. All these metrics can guide your purchase decisions and help you satisfy your customers better.
Shared Inventory Across Listings For the Same Product
The ideal app should be capable of tracking inventory across multiple listings for the same product. This is one of the shortcomings of the native Shopify app, as it cannot effectively manage multiple inventory listings that rely on one source.
Automated Inventory Replenishment
Your inventory management system should be able to generate purchase orders once you have the lowest inventory levels automatically. Furthermore, it should recommend order quantities based on previous sales data. These capabilities will significantly streamline your stock replenishment process.
Locked Inventory
If you offer special promotions or pre-order sales, you may want to prevent the items from showing on listings. However, you’d still want them to show on your total inventory since you’ll be processing pre-orders and promotional sales orders. The best Shopify inventory management apps have a wide range of features for locking such products.
Cross-Channel Capabilities
As mentioned earlier, brands that sell across multiple channels will benefit significantly from having a bird’s eye view of their inventory and sales data across each channel. For example, they should know how each SKU is shared across listings, the quantities of inventory in each warehouse at any given time, the amounts appearing on the listings across each channel, etc. Not all inventory management software can provide these vital pieces of information as desired.
How ShipHero Makes Inventory Management Easy on Shopify
If you’ve been looking for an all-encompassing Shopify inventory management app that allows you to fulfill orders expediently and manage inventory while still giving you the best shipping rates, ShipHero is the future of inventory management. Our inventory planner serves over 4,000 eCommerce brands and third-party logistics (3PL) companies, and you’ll no doubt enjoy our custom workflows. Below are a few advantages of ShipHero over its competitors:
All-in-One Inventory Tracking
With ShipHero, inventory management doesn’t stop at knowing what’s left in your warehouse or fulfillment center. Our all-in-one inventory tracking feature gives you limitless capabilities, including but not limited to tracking a product’s shelf life, tracking movement across warehouses, monitoring sales data across each sales channel, figuring out the best shipping routes and even providing customer experience insights.
These features allow you to monitor inventory movement in and out of your fulfillment centers while ensuring you give your customers the best shopping experience.
Easy to Set Up Shopify Inventory Integration
ShipHero is available on the Shopify App Store, and it seamlessly integrates with all the essential Shopify features. For example, the app easily connects with Shopify POS and allows you to swiftly and securely process customer orders as they come in. Beyond Shopify native apps, ShipHero also boasts numerous integrations that make it easy to connect shipping carriers, other eCommerce platforms such as WooCommerce and other essential business software like Inventory Planner.
And it still doesn’t end there. ShipHero further boasts over 20 partners that provide systems expertise and integrations to help you get more out of the app. FedEx, Hermes, LaserShip, DHL, USPS, WooCommerce, Walmart and Shippo are just some of ShipHero’s illustrious partners.
Inventory Reorder Alerts
As already emphasized, the ideal inventory management app should be capable of automatically reordering inventory based on your sales records. ShipHero also ticks this box, and it can significantly streamline your stock replenishment process while helping your in-house buyers make better decisions.
Also, since the app can have multi-channel integrations, it monitors your stock level across all the warehouses and factors in your sales data across each sales channel before placing the order. So, you can rest assured it’ll suggest just the correct quantity you need to satisfy all your customers and not just your customers on Shopify.
Conclusion
The native Shopify inventory management app can satisfy your needs if you only sell a few items on Shopify. However, the app’s limitations become more glaring when you explore other channels and expand your SKU library.
You’ll have to manually input SKUs into individual listings and update your stock levels, which can lead to poor inventory management. Doing this is akin to going back to managing stock using excel spreadsheets, and there’s no doubt your stock managers can make better use of their time.
Thankfully, ShipHero, an all-encompassing option for inventory management that integrates seamlessly with Shopify, is the commerce solution you need. The software possesses the much-desired multi-channel inventory management capabilities to streamline your inventory management tasks, get real-time location data, achieve strong sales and improve operational efficiency.
What’s more? You’ll be incurring significant cost savings while leaving your customers pleasantly satisfied. ShipHero helps you spend less time on inventory and has just the attributes you need to stay ahead of the competition.
Get started with ShipHero today by clicking the button below.
Shopify Inventory Management FAQs
Is there inventory management in Shopify?
Yes, there is built-in inventory and warehouse management on Shopify. You can track inventory history, stock transfers and product variants, adjusting stock levels as necessary.
Which is the best inventory management software integrated with Shopify?
The best inventory management for Shopify is ShipHero, which is ideal for growing and high-volume brands. ShipHero provides real-time tracking for stock transfers, levels, sellouts and replenishments. It also offers full warehouse management, enabling users to automate repetitive functions that contribute to a complex workflow.
In addition, ShipHero provides advanced reporting and personalized dashboards that make it easy to share data across teams. Other advanced features besides direct integration with Shopify include multi-location inventory, barcode scanning and supplier management. ShipHero also serves 10% of Shopify Plus stores globally.
How do I add a stock to Shopify?
You can add stock to your Shopify account by following these steps:
- Click on Products from the Shopify admin page.
- Click Add Product.
- Entitle your product and add a description.
- Save your product.
There are additional options for updating your stocks on Shopify, including duplicate, tags, edit, barcode scanning, delete and archive.
–
About ShipHero: We make it simple for you to deliver your eCommerce. Our software helps you run your warehouse, and our outsourced shipping solutions eliminate the hassle of getting your products to your customers. With over 5,000 brands and 3PLs relying on us daily, we’re here to help with all your logistics needs.
Let us know how we can help you today by scheduling a call HERE.
Apr 2, 2024 | Blog, Warehouse Management Software
Whether you’re a small online retailer or a multinational corporation, the right shipping software can help streamline your package delivery process, save you time and money, and improve customer satisfaction.
This article explores what shipping software is, why you need it, its key features, how to choose the right one, and more.
What is Shipping Software?
Shipping software is a technology solution that has revolutionized the way businesses handle their shipping processes. Beyond simply automating the shipping process, it optimizes for efficiency and cost-effectiveness.
Imagine being an online retailer with a high volume of shipments. Without shipping software, you would have to manually create shipping labels, select the best carrier for each shipment, and manage returns. This could be a time-consuming and error-prone task.
However, with shipping software, all of these tasks are streamlined and simplified. With just a few clicks, you can generate shipping labels, calculate shipping costs, print packing slips, and handle all the necessary documentation. This not only saves you valuable time but also reduces the chances of errors in the shipping process.
But shipping software offers even more benefits. It brings together different shipping carriers and consolidates their services into a single platform. This means you no longer have to juggle multiple carrier accounts or manually input shipment data for each carrier. Shipping software does it all for you, making it easier than ever to compare rates, delivery times, and service levels.
Imagine having to manually compare rates and delivery times for multiple carriers. It would be a time-consuming and tedious task. With shipping software, you can easily compare carriers side by side and make informed decisions about which carrier to choose for each shipment.
Furthermore, shipping software provides valuable insights and analytics. It tracks and records data about your shipments, letting you analyze trends, identify areas for improvement, and make data-driven decisions. This level of visibility into your shipping process can help you optimize your operations and reduce costs.
Additionally, shipping software often integrates with other business systems, such as inventory management or customer relationship management (CRM) software. This integration allows for seamless communication and data sharing between different systems, further streamlining your operations.
In conclusion, shipping software is a game-changer for businesses that rely on shipping. It automates and optimizes the shipping process, saving time, reducing errors, and providing valuable insights.
By consolidating different shipping carriers into a single platform, shipping software simplifies the comparison of rates and delivery times. With its integration capabilities, it can seamlessly connect with other business systems, enhancing overall efficiency.
Shipping software is truly a must-have tool for any business that wants to stay competitive in the fast-paced world of eCommerce.
For businesses looking to get a complete view of how shipping software fits into the larger context of shipping operations, our guide on shipping operations is a must-read. It covers everything you need to know about optimizing your shipping operations for peak efficiency and customer satisfaction.
Why Do You Need Shipping Software?
The reasons are compelling and could make or break your business.
Efficiency:
With the click of a button, you can generate shipping labels, eliminating the need for manual data input. This not only saves you time but also reduces the risk of human error.
Cost Savings:
The software analyzes different carriers’ rates, taking into account factors such as package weight, dimensions, and destination. It then lets you choose the most cost-effective solution for each shipment.
Improved Customer Experience:
Customers appreciate being able to track their packages in real-time, knowing exactly when to expect their delivery. By automating shipping notifications, you can keep your customers informed at every step of the shipping process, enhancing their overall satisfaction.
Time Savings:
You no longer need to log in to multiple carrier websites to create labels or track shipments. With shipping software, you can access all your shipping information in one place, streamlining your workflow and allowing you to focus on other aspects of your business.
Integration with Other Systems:
A smooth flow of information between different parts of your business eliminates the need for manual data entry and reduces the risk of error.
Advanced Reporting and Analytics:
You can track key metrics, such as shipping costs, delivery times, and carrier performance, to identify areas for improvement. By analyzing this data, you can make informed decisions to optimize your shipping processes and enhance overall efficiency.
Customer Support:
Whether it’s troubleshooting a technical problem or seeking advice on optimizing your shipping strategy, you can rely on their expertise and guidance. This support ensures that you can make the most of your shipping software and address any challenges that may arise.
Shipping software is a valuable tool for eCommerce businesses, offering efficiency, cost savings, improved customer experience, time savings, integration with other systems, advanced reporting and analytics, and dedicated customer support.
By investing in shipping software, you can streamline your shipping processes, reduce costs, and provide an exceptional shipping experience for your customers.
Key Features of Shipping Software
When selecting shipping software for your eCommerce business, it’s important to consider the following key features:
- Integration Capabilities: Look for shipping software that seamlessly integrates with your eCommerce platform, order management system, and other essential tools to streamline your operations.
- Carrier Options: Ensure the software supports a wide range of shipping carriers and lets you choose the most suitable options for your shipments.
- Automated Label Printing: The ability to generate shipping labels automatically is a crucial feature that saves time and eliminates errors associated with manual data entry.
- Real-time Tracking: Look for shipping software that provides real-time tracking updates to both you and your customers, enabling them to monitor their shipments every step of the way.
- Reporting and Analytics: Advanced shipping software gives you insights into your shipping performance and identifies areas for improvement.
Choosing the right carrier for each shipment doesn’t have to be overwhelming. To explore more about selecting the best multi-carrier shipping software that simplifies this decision-making process, check out our comprehensive guide on the best multi-carrier shipping software. This resource is very useful for businesses looking to optimize their shipping strategy across multiple carriers.
How to Choose the Right Shipping Software
Consider the following factors to make choosing the right shipping software for your eCommerce business a less daunting task:
- Compatibility: Ensure that the software integrates seamlessly with your existing systems and platforms, such as your eCommerce platform and order management system.
- User-Friendliness: Look for software that is intuitive and user-friendly, as it will be used by multiple team members with varying levels of technical expertise.
- Scalability: Consider your future growth and ensure the shipping software you choose can scale with your business, accommodate increased order volumes, and account for additional shipping requirements.
- Customer Support: Look for shipping software providers that offer excellent customer support, including responsive assistance and comprehensive training resources.
- Cost: Finally, consider your budget and the value that the shipping software provides. Compare pricing plans and assess how the software’s features align with your business needs.
If you’re looking at logistics beyond just shipping software, understanding the role of third-party logistics can be pivotal. Our detailed 3PL guide offers insights into how 3PL services can complement your use of shipping software, potentially further streamlining your eCommerce operations.
Key Takeaways
- Shipping software is a game-changer for eCommerce businesses, offering automation, cost savings, improved customer experience, and more.
- When selecting the right shipping software for your business, consider key features such as integration capabilities, carrier options, automated label printing, real-time tracking, and robust reporting.
- Evaluate compatibility, user-friendliness, scalability, customer support, and cost to make an informed decision.
- If you put in the legwork to find the right shipping software for your business, you’ll see immediate returns on your investment the minute your software goes live.

Frequently Asked Questions
Can shipping software be used for international shipments?
Yes, shipping software can handle both domestic and international shipments by providing the necessary documentation and facilitating international shipping processes.
Can shipping software integrate with my existing eCommerce platform?
Most shipping software solutions offer integrations with popular eCommerce platforms such as Shopify, WooCommerce, Magento, and more.
Is shipping software suitable for small businesses?
Absolutely! Shipping software benefits businesses of all sizes, providing efficiency, cost savings, and a better customer experience, regardless of their scale.
By implementing shipping software for your eCommerce business, you can streamline your package delivery process, save time and money, and create a positive customer experience.
Take advantage of the automation, cost savings, and flexibility that shipping software provides, and watch your eCommerce business thrive.
Apr 21, 2023 | Blog
Shipping operations play a pivotal role in the world of eCommerce businesses. Regardless of how exceptional your product is, its true value to both customers and investors is only realized when it’s delivered without hitches. Even outstanding product reviews can be overshadowed by shipping problems such as delays, incorrect shipments, or goods arriving damaged. These issues can range from minor problems to major disruptions that can significantly impact the business.
To truly scale your eCommerce business, it’s essential to refine your shipping processes. This not only ensures timely and cost-effective deliveries but also broadens your customer reach. Many shipping companies face problems in their operations, from cargo handling to tracking shipments. The scale of these issues can vary, but they often impact the business’s bottom line and investor confidence.
In This Article:
- Explore best practices for shipping products both domestically and internationally.
- Dive into strategies for optimizing labor costs, ensuring workplace safety, and leveraging data-driven software to boost your company’s order fulfillment efficiency.
Understanding Shipping Operations
Shipping operations encompass the various processes that eCommerce companies put in place to guarantee timely deliveries. Effective management of these operations is paramount. Disruptions in areas like warehousing, inventory, or the broader supply chain can lead to significant losses. Whether you’re a small business sending out daily packages or a global enterprise handling vast cargoes, shipping operations are the backbone of your success. From shippers and carriers to importers and exporters, everyone in the shipping lines plays a crucial role. A cohesive team, including the shipper and shipowner, ensures that the freight reaches its destination safely.
Four Core Stages of Shipping Operations
Shipping operations, although they might differ across industries, generally involve four primary stages:
Picking:
This stage involves a dedicated team, often referred to as pickers, retrieving items from warehouse storage for packaging. Efficient warehouse picking is crucial for meeting customer demands and ensuring worker safety. Modern software solutions can guide pickers in selecting the right products and maintaining accurate documentation. Learn more about warehouse processes here.
Packing:
In larger operations, picking and packing are distinct processes. Proper coordination ensures optimal use of resources, from equipment to personnel. It’s also essential to consider the consolidation of goods, and shipping label especially when dealing with containers.
Labeling:
Proper labeling of shipping carrier is paramount. Incorrect or missing labels can lead to issues with customs clearance, delivery, and trade rights. Understanding how shipping labels work is essential.
Shipping:
Once products are en route, especially via sea vessels or other ships, control diminishes. Challenges can arise, emphasizing the importance of insurance for all shipments. Discover more about expedited shipping options here. It’s also vital to consider maritime regulations, port criteria, and charter agreements. Effective tracking systems and efficient terminals play a significant role in ensuring the cargo reaches its destination.
Local vs. International Shipping:
While the core stages remain consistent, nuances arise when comparing domestic shipping rates to international shipping:
Local Shipping:
Shipping within a region offers more control. Choices offering free shipping range from UPS to local couriers, depending on the delivery area. Local terminals and ports play a significant role in ensuring smooth transportation.
International Shipping:
Shipping overseas, for instance to Canada or France, introduces complexities like customs and tariffs. Shipowners and shipping companies must be aware of the rights and responsibilities associated with international freight. Exporters must also navigate maritime regulations and charter agreements that dictate the terms of cargo transport.
eCommerce Shipping Software:
Such software aids in managing product shipping operations. Most warehouse management systems incorporate shipping features, streamlining the logistics and transportation processes. This includes tracking containers, managing storage facilities, and ensuring the right equipment is used to ship products.
Five Tips for Successful eCommerce Shipping
Holistic Cost Analysis:
Consider the entire operational cost, not just shipping expenses. Having multiple warehouses might reduce shipping times and costs but could increase maintenance and storage expenses.
Data Analysis:
Utilize warehouse and eCommerce software to assess shipping cost and efficiency. Base strategies on concrete information, not mere assumptions.
Automation:
Minimizing manual processes reduces errors, ensuring accurate order fulfillment and efficient handling free shipping of goods.
Prioritize Safety:
Worker safety should always come first. Avoid potential legal and financial repercussions by ensuring a safe working environment.
Regular Reevaluation:
Continuously assess and adapt your shipping strategy to changing market conditions and business criteria.
Sustainability in Shipping
In the dynamic world of eCommerce shipping operations, sustainability emerges as a guiding star. Beyond the seamless delivery of products, a growing focus on environmental responsibility is steering the conversation. Embracing sustainable shipping practices entails utilizing eco-friendly packaging materials, optimizing routes to curb emissions, and harnessing renewable energy sources within logistics. This harmonious approach not only ensures business success but also contributes to a greener planet. Dive into the realm of sustainable ecommerce shipping solutions and discover the fusion of commerce and conservation.
Last-Mile Delivery Innovations
Amid the tapestry of the ecommerce shipping process, the final stretch known as last-mile delivery unveils innovation’s vibrant tapestry. Picture a realm where drones soar with packages, autonomous vehicles navigate streets, and crowdshipping paints a collaborative canvas. This realm is now. The veil between order and doorstep is thinning, driven by cutting-edge technologies that redefine the eCommerce experience. These innovations are not mere concepts; they are tangible threads knitting the future of shipping.
Reverse Logistics Reimagined
In the dance of eCommerce, returns play an unforeseen role – enter reverse logistics. This backstage choreography involves handling returns with grace, orchestrating restocking, and nurturing customer satisfaction. Embracing returns as part of the performance, businesses can pivot this process into a symphony of efficiency. The spotlight shines on managing expectations and orchestrating returns seamlessly. Unravel the script of reverse logistics and find harmony amid the complexity.
Navigating Global Trade Agreements
Within the world of international eCommerce, a hidden labyrinth awaits – the realm of global trade agreements. The tapestry of cross-border commerce is woven with the threads of trade pacts, shifting regulations, and intertwined destinies. Here, businesses voyage through a sea of complexities, adapting their sails to ever-changing winds. Understanding this landscape is akin to deciphering a map to success across international waters.
Customer-Centric Shipping Experience
Beneath the logistics, a heartbeat echoes – the rhythm of customer experience. Transparent communication, timely deliveries, and the art of the unboxing experience converge to create a symphony of delight. Nurturing this customer-centric melody sets the stage for applause. Here, the curtain rises on strategies that transform shipping into a captivating experience, where customers become avid fans and brand advocates.
Risk Management and Insurance Insights
Amid the whirlwind of shipping, unforeseen storms can arise. The anchor that steadies the ship is risk management and insurance. A safety net woven with insights, strategies, and contingency plans shields businesses from financial tempests. This narrative of preparedness weaves together the significance of understanding insurance types, risk assessment, and sailing through the waves of uncertainty.
Innovative Packaging Solutions
In the realm of shipping, packaging is not just a cover but an art form. Imagine a world where packages are shields against damage, bearers of eco-friendliness, pioneers of privacy with discreet shipping, and creators of enchanting unboxing experiences. This world exists. Innovative packaging and shipping solutions redefine the ordinary, crafting a symphony of protection and aesthetics. Let the journey through inventive packaging unveil a new dimension of shipping’s visual and tactile poetry.
Tech-Driven Future of Shipping
On the horizon of shipping, a dazzling sunrise emerges – the age of technology. Blockchain brings transparency to tracking, AI predicts the tides of demand, and IoT breathes life into real-time monitoring. This symphony of innovation orchestrates a harmonious future where data dances, machines collaborate, and the efficiency of shipping is transformed. Unveil the future, where tech’s crescendo shapes the destiny of shipping operations.
Cultural Nuances in Shipping
Across the seas of international shipping, cultural currents flow. Navigating these waters entails more than charts and coordinates – it requires an understanding of cultural nuances, customer preferences, and the art of respectful interactions. Each shore is a tapestry of traditions, and each customer a unique chapter. By embracing cultural considerations, businesses unfurl the sails of cross-border success.
Synergy with Shipping Partners
In the symphony of shipping, partnerships are the harmonies that elevate the melody. Shipping carriers, couriers, and freight forwarders weave a fabric of collaboration that carries the eCommerce chorus to distant shores. Nurturing these alliances is more than a transaction; it’s the secret to seamless logistics. Discover the art of synergy, where partnerships propel the rhythm of successful ecommerce shipping strategy.
Post-Delivery Analytics Unveiled
After the applause of delivery fades, the analysis takes center stage. Post-delivery analytics, a symphony of data, offers insights into performance and points towards the future. Feedback from customers, patterns in delivery times, and a scorecard of satisfaction compose this insightful melody. By embracing this data-driven tune, businesses refine their shipping operas and shape the encore of success.
Key Takeaways
- Success in eCommerce is intrinsically linked to efficient shipping operations.
- Utilizing eCommerce shipping software can streamline and optimize these operations, enhancing the overall performance of the business and attracting investors.
Shipping Operations FAQs
What is Dropshipping?
Dropshipping involves selling products stored at a third-party location, often an online store without the seller maintaining a physical inventory.
What are the 3 Methods of Shipping?
Land, sea, and air are the primary shipping methods. The choice of shipping method depends on the product, its value, and the destination.
Should Shipping be Included in the Cost of Goods Sold?
For U.S. tax purposes, shipping costs should not be included in the cost of goods sold.

Feb 23, 2021 | Best Practices, Blog, Fulfillment, Warehouse Management Software
Welcome to our Shipping Methods Explained blog series. In this series, we will deep dive into fulfillment methods – that is, how businesses fulfill their online orders and get products to their customers.
Sounds simple right? Well, in theory it is. You could hop on your itty-witty bicycle and hand-deliver your product, mission accomplished. But consider the complexity when your company fulfills hundreds to thousands of orders daily, not to mention the skyrocketing shipping costs that could price you out of the market.
Managing inventory, navigating each carriers’ specific requirements, calculating the lowest cost from thousands of shipping options… it’s a daunting task. That’s why more and more businesses are outsourcing their fulfillment methods.
Are you ready to outsource your fulfillment? Let’s analyze your options to help you decide the best method for your business. In this article, we’ll discuss Multimodal and Intermodal Shipping. What is multimodal and intermodal shipping? What are the pros/cons of each? How do they compare/contrast and which one right for my business, if any? Let’s dive in.
(Check out our previous articles on Dropshipping, FaaS, and FBA/FBM. And be sure to check back for future articles where we’ll cover even more fulfillment methods)
What is Multimodal vs. Intermodal?
Multimodal transport is also known as ‘combined transport’ because the products are moved using different modes of transportation along the fulfillment journey, but under the terms of a single contract and facilitated by a multimodal transport operator (MTO). Whether by road, sea, air or rail, or a combination of them all, the MTO is liable for the entire journey from beginning to end, although they often use sub-contracted carriers that specialize in each mode of transportation.
Intermodal transport involves the use of an intermodal container which carries products throughout the entire fulfilment journey; regardless of the type of transportation, the same intermodal container will be offloaded from one method and loaded onto the next without ever moving the product inside.
The main difference between multimodal and intermodal transport is: 1) how the product is transferred between transportation modes, and 2) how the contracts are made with each carrier.
Product Transfer
With multimodal transport, the products or commodities are loaded and unloaded into transportation-specific containers when transferring, say, between sea and rail, rail and ground, etc. Excessive product transfer may result in product damage or loss; you may have heard the phrase “fallen out of a truck” when asking your relative about an expensive purse they clearly can’t afford. In fact, product damage during transportation costs up to $0.48 per pallet annually, which certainly adds up over time with larger supply chains.
This is the benefit of intermodal transport, because the products are loaded into a single intermodal container to be used for several modes of transportation. The products themselves will remain secure as the container itself is loaded and offloaded from a truck, train, ship or air freight.
Using one intermodal container allows for safer packing of products, which results in less damage and loss, as well as quicker and more efficient movement between freight methods. For this reason, intermodal transport tends to be less costly than multimodal transport.
Contracting Carriers
During a multimodal transport, the shipper creates a single contract with the Multimodal Transport Operator (MTO), which is wholly responsible for the cargo from the origin to the end destination. This allows the shipper to simplify the communication process by just working with a sole transport provider or agent. Also, the simplified communication allows for more accurate shipping updates, tracking notifications, and opportunities for optimization. On the other hand, the shipper must rely on the MTO to select the best/cheapest routes for their cargo, and flexibility is limited.
Conversely, during an intermodal transport, the shipper must create multiple contracts with individual carriers. While there is only one intermodal container, it will be passed between many liable parties, increasing the complexity for the shipper in terms of communication and optimization across carriers; however, the shipper has more flexibility to independently choose each leg of the fulfillment journey.
In summary:
Multimodal Transport
- Multiple carriers, one contract with MTO
- Product transfers containers between transports
- Enhanced communication and optimization, but heavy reliance on MTO routes
- More chance of product damage and loss
Intermodal Transport
- One intermodal container, multiple contracts with carriers
- Products remain secure in single shipping container
- More flexibility to choose your own routes along fulfillment journey, but more complexity for the shipper
- Less chance of product damage and loss
In conclusion, shippers must determine if multimodal or intermodal is the right choice given their circumstances, i.e., is your product fragile or at risk of damage/loss, do you have the resources to schedule and manage carrier contracts, etc. Thankfully, smart fulfillment providers and 3PLs like ShipHero can help you determine the best way to ship.
Be sure to stay tuned to our Shipping Methods Explained series as we deep dive into the specifics of fulfillment.
Learn more about ShipHero’s industry-leading warehouse management software.