Feb 16, 2023 | Blog
Your 3PL logistics partner is an extension of your business. As a business owner, it’s your responsibility to tell them exactly what you do and don’t want. But how do you know what you want? You aren’t as familiar with the logistics industry as them, so it would make sense that you might not know exactly what to ask for. In this article, we’ll review how to manage and improve your 3PL partner’s performance so you can both experience a successful partnership. Let’s dive in!
What is 3PL Performance?
3PL performance refers to the level of service and efficiency offered by a third-party logistics company in managing your business’s supply chain management. It includes several measurements which are key performance indicators of the success of logistical infrastructure. A few examples of what to measure would be delivery accuracy, order fulfillment speed, inventory management, and customer satisfaction. Let’s dive into what that looks like:
- Delivery Accuracy – A 3PL’s ability to deliver orders on time and in the correct quantities, without errors or damages.
- Order Fulfillment Speed – The speed at which 3PL processes and delivers orders, including the time taken to pick, pack, and ship orders.
- Inventory Management – The ability of a 3PL to accurately track and manage inventory levels, ensuring that the right products are available when and where they are needed. This includes minimizing stock shortages, reducing carrying costs, and improving the accuracy of inventory reports.
- Customer Satisfaction – The ability of a 3PL to get packages to customers on time, intact, and with no errors.
How to Measure 3PL Performance
Measuring 3PL performance involves evaluating the effectiveness of a third-party logistics service provider in managing a company’s supply chain operations. Using the same four examples above of measuring delivery accuracy, order fulfillment speed, inventory management, and customer example let’s dive into how you can measure the 3PLs performance in these areas.
- Delivery Accuracy – This can be measured by the percentage of deliveries that are on time and without errors or damages. To improve delivery accuracy, a company can set clear expectations and goals with its 3PL logistics provider, and track performance using real-time data and reports.
- Order Fulfillment Speed – This can be measured by the average time taken to pick, pack, and ship orders. To improve order fulfillment speed, a company can use automation tools and processes, as well as set clear performance targets and regularly monitoring progress.
- Inventory Management – This can be measured by the accuracy of inventory reports, stock levels, storage of pallets, and the amount of inventory carrying costs. To improve inventory management, a company can implement real-time inventory tracking and reporting, regularly review stock levels and work with its 3PL to optimize inventory management processes.
- Customer Satisfaction – This can be measured by surveying customers and tracking key performance indicators, such as order accuracy, delivery speed, and product quality. To improve customer satisfaction, a company can work with its 3PL to provide regular updates, resolve any issues quickly, and regularly review performance data to identify areas for improvement.
Overall, the key to effectively measuring 3PL’s logistics performance is to establish clear performance targets, regularly monitor performance data, and work with the 3PL to continuously improve processes and systems.
How to Manage 3PL Performance
Managing a 3PL’s performance starts with you! Here are a few tactics to help you ensure your 3PL is meeting your performance needs.
Set Clear Expectations From the Start
Clearly defining what you expect from your 3PL in terms of performance, services, and delivery time frames is essential for a successful relationship. If you require a 99% accuracy rate for deliveries, make sure that this is agreed upon and included in your contract. As an example, if your company wants to work with a 3PL for order fulfillment you will first define the scope of work as receiving, storing, and shipping orders within their fulfillment center. Then you’ll set KPIs such as order accuracy, cost savings, and on-time delivery. If they have warehouse management software, you’ll also want to communicate how you plan to use it. Then review any special requirements such as unique packaging needs. Once all this is discussed, you should form a specified contract (which many 3PLs create for you). The agreement should be documented and signed between your business and the 3PL. This way, the company and the 3PL both have a clear understanding of the expectations and can work together effectively.
Designate One Point of Contact With Your 3PL
Having one designated point of contact with your 3PL can improve communication and help to prevent confusion or misunderstandings. This person should be responsible for managing the relationship with the 3PL and ensuring that all performance expectations are met. The designated point of contact should be an individual within your organization who is responsible for managing the relationship with the 3PL. This person should have a clear understanding of your company’s objectives, policies, and procedures and effectively communicate these to the 3PL. This individual should be available to answer questions and address any concerns that may arise during the course of the partnership.
Keep the Lines of Communication Open
Good communication is key to a successful 3PL partnership. Encourage regular check-ins, have open and honest discussions about performance, and make sure that you have a clear process in place for dealing with any issues that arise. To keep the lines of communication open, schedule regular check-ins with the 3PL. These check-ins could be bi-weekly, monthly or quarterly and can be in-person, via email, or through a video conferencing platform. During these check-ins, review performance metrics, discuss any challenges that have arisen, and share updates on any changes to the relationship or business. Additionally, setting up a shared project management platform or email chain can be a helpful tool for communication. This allows all parties involved to keep track of updates, questions, and issues in one centralized location. Encourage open and honest communication, and create an environment where any questions or concerns can be brought to the table. This builds trust and a stronger partnership between your company and the 3PL.
Set Up Formal Performance-Review Periods
Regular performance reviews help to keep the 3PL accountable and provide an opportunity to discuss any issues or areas for improvement. Schedule regular meetings, and make sure that performance data and metrics are reviewed and discussed. When setting up a formal review with your 3PL, it is important to cover key areas to assess their performance and identify areas for improvement. During the review, you should discuss specific metrics and warehouse KPIs (Key Performance Indicators) that are relevant to your business. This can include order accuracy, delivery times, customer service levels, inventory management, and cost-effectiveness like the above, or it could include other metrics relevant to your business. The review should also include an evaluation of the overall relationship between your company and the 3PL, including their ability to effectively meet your expectations and support your business goals. Additionally, it is important to address any operational or customer-related issues within the 3PLs fulfillment center that have arisen and discuss any areas where the 3PL can improve in the future.
Establish an Escalation Process
Having a clear escalation process in place helps to quickly resolve any issues or problems that arise. This process should outline how issues will be reported, who will be responsible for resolving them, and the steps that will be taken to resolve them. For instance, if there’s a problem with an order, the first step could be to contact the designated point of contact at the 3PL. If a resolution isn’t reached after a certain amount of time, the next step could be to escalate the issue to a higher-level manager at the 3PL. If the issue still isn’t resolved, the next step could be to involve a senior executive from your company or a third-party mediator to help resolve the situation. It’s important to have a clear escalation process in place so that issues can be resolved efficiently and effectively without causing undue stress or harm to the relationship with the 3PL.
By using these tactics, you can help to ensure that your 3PL logistics performance remains on track and that your 3PL continues to deliver the level of service that you require.
Tips for Managing 3PL Performance
Regular Check-Ins
It’s important to keep a pulse on the 3PL’s performance. Schedule weekly or monthly check-ins to review progress and address any issues. For regular check-ins, you could create a shared dashboard to track metrics and KPIs. This allows both you and the 3PL to see areas for improvement and track progress.
Working Together
Treat the 3PL as a partner, not just a vendor. Collaborate on processes and procedures to ensure a seamless flow of operations. Their fulfillment center should be an extension of your business. To work together, hold joint training sessions where both parties can learn from each other and create a mutual understanding of the operations.
Clear Communication With 3PL
Open and transparent communication is key to success. Clearly outline your expectations and communicate any changes or concerns promptly to avoid misunderstandings. To ensure clear communication, use a project management tool to keep all stakeholders in the loop and record all discussions and decisions made. This way, there is a clear record of expectations and agreements.
Key Takeaways
In conclusion, outsourcing logistics activities to a 3PL can provide numerous benefits to small business owners, including increased efficiency, cost savings, and improved customer service. However, you and your 3PL logistics service provider need to both agree on what metrics and KPIs they are expected to hit, and the progress of hitting these metrics should be regularly reviewed. No provider is perfect, but clear communication allows you to both agree to expectations, air out any issues and set your partnership up for success. If you haven’t scheduled a review with your 3PL, do so today!
3PL Performance FAQs
How is 3PL Performance Measured?
A 3PL provider typically measures their own performance through a variety of metrics such as order fulfillment accuracy, order processing time, inventory accuracy, shipping accuracy, delivery time performance, customer satisfaction, and cost control. They use these metrics to evaluate their performance and identify areas for improvement, so they can ensure they are delivering the best possible service to their clients. For example, if order fulfillment accuracy is low, they may take steps to improve their processes, such as implementing new software or hiring additional staff, to increase accuracy and improve overall performance. Additionally, by monitoring delivery time performance, they can ensure that orders are reaching their customers in a timely manner, which maintains customer satisfaction and reduces the risk of customer churn. Overall, a logistics service provider should have a performance measurement strategy that provides insight into their operations, enabling their client, (you, the business owner) to make informed decisions that lead to better results and improved customer satisfaction.
Why is KPI Important for a 3PL?
KPI (Key Performance Indicator) is important for a third-party logistics firm because it provides measurable and quantifiable targets that help the provider evaluate their performance, track progress, and make informed business decisions. Warehouse KPIs serve as benchmarks for success and provide valuable insights into areas for improvement. They also help 3PLs to monitor their operations, identify areas for improvement, measure customer satisfaction, and optimize resources. By setting and tracking KPIs, 3PLs can monitor their performance and ensure they are meeting their goals and delivering the highest level of service to their customers.
How Do You Measure Logistics Performance?
Let me give you an example. Sarah sells handmade jewelry online and relies on a 3PL provider to handle the shipping and delivery of her products to customers. To ensure that her 3PL provider met her expectations, Sarah reviewed their fulfillment center setup, then shared key performance indicators (KPIs) to measure their performance. By consistently monitoring these KPIs, Sarah could assess the performance of her 3PL provider and make data-driven decisions to improve the overall customer experience. Over time, she saw a significant improvement in her KPIs, which translated into happy customers and increased sales.
Feb 16, 2023 | Blog
What is a third-party logistics provider (3PL) and how could it improve your business? In a world of continual shipping restraints and high customer expectations, a 3PL could be your solution. Below we will detail exactly what you can expect from using a 3PL and the benefits you’ll gain when using one for your business. Let’s dive in!
What is a 3PL?
A 3PL is a company that offers outsourced logistics and supply chain management services to businesses. These services can include transportation, warehousing, inventory management, and other related functions. When contracting with 3PLs you are provided a cost-effective solution for companies that do not want to invest in their own logistics infrastructure, allowing them to focus on their core competencies. Have you ever felt unsure of what to do next when you encounter a logistical problem? That’s another area 3PLs can help. They often have specialized expertise and technology so you can optimize your supply chain operations and improve efficiency.
Third-Party Logistics Definition, Process, & Resources
The infrastructure within a 3PL is rather impressive. They have poured their revenue into streamlining logistical operations with technology many others couldn’t afford to utilize if they tried to create their own logistics infrastructure.
With this infrastructure, they utilize a wide range of processes and resources to manage logistics and supply chain operations for their clients. These processes can include:
- Transportation management involves coordinating the movement of goods by road, rail, air, or sea.
- Warehousing and distribution, which involves storing and distributing goods in an efficient and cost-effective manner.
- Inventory management involves tracking and managing stock levels to ensure that products are available when customers need them.
To support these processes, 3PLs often invest in sophisticated technology. These technologies allow them to automate and streamline logistics operations, so they can provide real-time visibility into inventory levels, delivery schedules, and other key metrics to their clients. Often, they will also utilize a wide range of resources, such as a fleet of vehicles, warehouses, and equipment, to support their logistical processes. These technologies and resources work in tandem with a skilled workforce that includes logistics experts, transportation planners, warehouse managers, and inventory analysts who work to optimize their client’s supply chain operations.
Lastly, a main part of most 3PL processes includes working closely with their clients to understand their specific logistical needs and to develop customized solutions that align with their business goals. They also continuously monitor and analyze logistics trends and market conditions to identify opportunities for cost savings and process improvements. Basically, they are like a logistics superhero your business can call upon to make their logistical operations as efficient as possible!
Third-Party Logistics (3PL) Basics
When you’re setting up your business with a 3PL provider, they’ll need some basic information from you in order to get things moving. They’ll need to know all about the products you’re shipping, like their dimensions, weights, and any special handling requirements. They’ll also want to know your current and projected shipping volume, so they can plan accordingly. Additionally, they’ll need to know your preferred shipping methods and carrier preferences, and any specific delivery requirements, restrictions, or compliance requirements you might have.
Are 3rd-Party Logistics the Same as Order Fulfillment?
Third-party logistics is a service in which a company outsources its logistics and distribution functions to a third-party provider. This provider takes on the responsibility for all or some of the company’s logistics operations, such as transportation, warehousing, and distribution.
Order fulfillment, on the other hand, refers to the process of receiving, processing, and delivering customer orders. This process includes tasks such as receiving the order, picking and packing the items, and shipping the order to the customer. Order fulfillment can be handled by a company’s own logistics and distribution team or by a third-party provider.
In summary, 3PL is a broader term that encompasses all logistics and distribution functions, while order fulfillment is a specific aspect of logistics that refers to the process of fulfilling customer orders. A company may use a 3PL provider for both logistics and order fulfillment, or it may handle logistics in-house and use a separate 3PL provider for order fulfillment.
3PL Services vs. Drop Shipping
Third-party logistics companies offer a wide range of benefits over traditional drop shipping methods. One of the biggest benefits of 3PL services is the level of control and visibility they provide. With a 3PL provider, businesses have real-time access to inventory levels, shipping costs and information, and other logistics data, allowing them to make informed decisions about their entire supply chain. This level of control and visibility is often not possible with drop shipping, where businesses may have limited visibility into the logistics process. 3PL providers also bring specialized knowledge and expertise in logistics and supply chain management. They have the resources, technology and experience to optimize the entire logistics process, which can result in cost savings, improved efficiency, and increased competitiveness in the market.
Benefits of Third-Party Logistics
Are you tired of spending countless hours and resources managing logistics and supply chain operations for your business? Are you looking for a way to streamline your logistics processes and improve efficiency? Then look no further than third-party logistics.
By outsourcing logistics and supply chain management to a 3PL, you can free up valuable time and resources to focus on your business’s core competencies. A 3PL can handle the transportation, warehousing, and inventory management on your behalf, allowing you to focus on growing your business.
They can also help you save money by finding more cost-effective solutions for logistics and supply chain management. They have the expertise and technology to optimize logistics operations and improve efficiency, which can result in significant cost savings for your business.
Moreover, a 3PL can help you improve delivery times and increase customer satisfaction by optimizing logistics operations to meet customer demands. They can also help you improve inventory management by implementing inventory management systems that provide real-time visibility into inventory levels and stock management.
By outsourcing logistics and supply chain management, you can also take advantage of their networks of resources, such as transportation and warehousing facilities, and their skilled workforce, which includes logistics experts, transportation planners, and inventory analysts. Partnering with a 3PL will help your business grow. Instead of spending precious time and revenue packing orders, you can get those same orders to your clients faster and cheaper!
Will Your Business Benefit From Third-Party Logistics?
Here are several signs that indicate a business could benefit from using a third-party logistics provider:
- Lack of logistics expertise: If your business does not have the necessary expertise in logistics and supply chain management, it may be beneficial to outsource these functions to a 3PL.
- Capacity constraints: If your business is experiencing growth and is struggling to keep up with the demand for logistics services, a 3PL can provide additional capacity and support.
- High logistics costs: If your business is spending a significant amount of money on logistics and supply chain management, a 3PL may help you reduce costs by finding more efficient solutions.
- Difficulty in meeting customer demands: If your business is struggling to meet customer demands for delivery, a 3PL can help you optimize your logistics operations to improve delivery times and increase customer satisfaction.
- Difficulty in tracking and managing inventory: If your business is struggling to keep track of inventory levels and manage stock, a 3PL can help you implement inventory management systems to improve visibility and control.
- Difficulty in managing returns: If your business is struggling to manage returns and reverse logistics, a 3PL can help you handle these processes more efficiently.
If any of these sound familiar, your business will absolutely benefit from a third-party logistics solution!
The Third-Party Logistics Process
Are you curious about the inner workings of a 3PL fulfillment center? It can be difficult to understand the process if you’re new to outsourcing shipping. But the truth is, the 3PL fulfillment process is not as mysterious as it may seem. Let’s dive into the ins and outs of what happens in a 3PL eCommerce warehouse from the moment a customer clicks “submit order” on your online store to the final delivery.
eCommerce Platform Integration
An eCommerce platform is the software that powers your online store. Many 3PL companies have an eCommerce platform integration that will connect seamlessly with your store. This means when a customer is ready to check out and provides their billing and shipping information, this information is then processed by your 3PL partner. It goes to the fulfillment center where it is received and the order begins its journey.
Inventory Management
As the 3PL provider begins to check the inventory for the order they will often consult inventory management software which is usually connected to both your eCommerce platform and your overall inventory. That way the 3PL provider can know right away if the product is available, and can update stocking levels for you both to view.
Picking, Packing, and Shipping
Once the inventory is confirmed, the 3PL provider’s team will pick the items from the warehouse shelves. They use barcode scanning or other identification methods to ensure that they are picking the correct items and quantities. After the items are picked, they are packed and prepared for shipment. This may include packaging the items in protective material, creating shipping labels and invoices, and any other necessary preparation for shipping. After the order is packed, the 3PL provider will ship the order to the customer using the shipping method specified on the order. The 3PL provider may also provide tracking information to the customer so they can track their order during transit.
Same-Day Shipping
To achieve same-day shipping, a 3PL company requires a combination of strategic warehouse locations, fast and efficient order processing, real-time inventory management, expedited shipping options, and effective communication with the customer. Having strategically located warehouses that are close to major population centers allows the 3PL provider to quickly and efficiently ship items to customers within a certain radius. To achieve same-day shipping, the 3PL provider typically offers expedited shipping options such as overnight delivery or express shipping.
Reverse Logistics
When a customer initiates a return, the 3PL provider will typically receive the returned product and inspect it to make sure it’s in good condition. If there’s an issue with the product, the 3PL provider will contact the customer to resolve it. Once the return is approved, the 3PL provider will then process the return by updating the inventory, and if necessary, restocking the product.
Key Takeaways
Convinced yet? We know now that 3PLs stand out from other logistical solutions because they offer tailored solutions, specialized expertise, scalability, sophisticated technology, access to resources and handle reverse logistics processes. Plus they work closely with their clients to understand their specific logistics needs and develop customized solutions that align with their business goals. Which means you have more time to become the next big thing!
What Is a 3PL System FAQs
What is the Role of 3PL in a Company?
The main role of a 3PL is to handle the logistics functions that a company does not want to handle or cannot handle in-house. This can include transportation, warehousing, and distribution, as well as other logistics-related services such as inventory management, order fulfillment, and reverse logistics. By outsourcing logistics and distribution to a 3PL provider, a company can focus on its core competencies and business operations. This can help the company to save costs, improve efficiency, and increase its competitiveness in the market.
How Many Types of 3PLs Are There?
There are four types of 3PLs. First-party logistics (1PL) refers to in-house transportation services where a company handles its own logistics and distribution functions without the involvement of any additional parties, such as a florist using their own delivery van to drop off purchases to local buyers. Second-party logistics (2PL) involves the use of outside logistics providers, such as courier services like USPS, FedEx, or UPS, which are not integrated with the company when contracted. Third-party logistics companies create an integrated system that allows for real-time data sharing between the company and the 3PL, resulting in a streamlined, efficient, and reliable long-term solution in complete synchronicity with the business. Fourth-party logistics (4PL) is much like a 3PL, but logistically the company’s relationship with the consumer is often brokered by a middleman.
Jan 6, 2023 | 3PL Warehouse Management, Best Practices, Blog
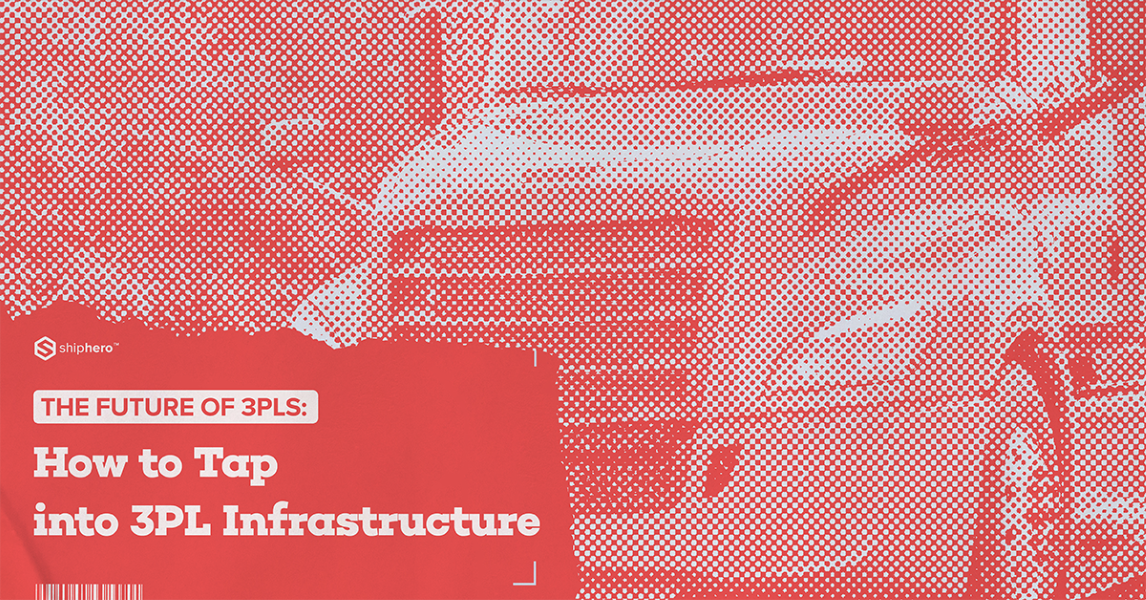
Are you feeling overwhelmed as your eCommerce business grows? Can’t quite keep up with the demand but don’t have the capital to invest in a massive supply chain infrastructure of your own? You don’t need to. With a 3PL (third party logistics), you can access sophisticated systems, warehouses, and transportation networks that provide unmatched customer service and cost savings. In this blog post, we’ll explore how tapping into 3PL infrastructure may be just what’s needed for growing eCommerce businesses to weather even the stormiest market.
When Do Businesses Need a 3PL provider?
If you’ve never seen the impact of third-party logistics providers, you may be under the impression that it’s an expense you can do without. But trust us when we say that it pays off a lot more than doing all your fulfillment in-house! 3PL companies can help merchants – from small businesses to eCommerce empires – with their scalability needs. When faced with unforeseen order growth or a spike in customer demand, working with a third party warehouse and its services can save you time and money in the long run. After all, nothing’s worse for your brand than breaking promises to customers, especially in an era when 60% of global consumers expect same-day or two-day delivery.
How 3PLs Bring Technology to Infrastructure
3PLs have come a long way since the days of organizing physical products in dusty warehouses – they’ve brought technology to infrastructure! Online merchants are all too aware that keeping up with the big retailers means implementing advanced 3PL tech, such as their warehouse management system (WMS). A WMS allows 3PLs to connect data from various sources, enabling end-to-end visibility into every single order. Wherever you send it, you can track it! So what exactly does this mean? In short, online merchants can more easily compete with larger retailers by turning to technology-enabled 3PLs for services.
- Automating the 3PL Automating the 3PL process isn’t just for robots, it’s for people too! By automating processes, businesses can save precious time and effort. Ordering and tracking become an effortless breeze. With real-time updates in your online store, warehouse staff is updated on orders as soon as they’re placed. Furthermore, various parameters allow you to quickly search and find exactly what you need. And that’s not all – fulfillment software also ensures optimal inventory management, so reordering is quick and efficient. Automation leads to reduced delivery times so customers can receive their packages faster.
- Data Moves Freight Whether it’s to shave off delivery time or reduce inventory costs, data can help get freight moving in the right direction. Fulfillment software can use past data to ensure you’re sending your products to the best possible locations. No more guesswork! With built-in metrics focusing on peak times, revenue, by channel, and quantity orders by USPS zone, you’ll have unbeatable insight to optimize your supply chain. Plus, data logs only get more accurate as time goes on and you gather increasing amounts of order history – it’s a win-win!
- Reduce Errors 3PL technology is here to make our lives easier, especially when reducing errors in order fulfillment. By automating the shipping process with connected technologies, 3PL infrastructures eliminate duplicated work and human error that can cost customers time, money, and an overall bad experience. What’s more, 3PL technology offers insight into the 3PLs performance with complex data like accuracy levels and delivery timelines that demonstrate how orders are being handled every step of the way.
- Meet Customer Expectations Customers today expect lightning-fast delivery within the same day or two days, which can only be achieved if the right technology is in place. That’s where a tech-enabled 3PL comes in; they can help you optimize your storage and shipping to meet customer expectations. With their system, your inventory will be distributed to warehouses closest to your customers. Each time an order is placed, algorithms select the courier providing an efficient, cost-effective solution.
How to Tap into 3PL Infrastructure
Partnering with 3PL services can help give you a leg-up in today’s competitive world, but it’s essential to be sure the 3PL infrastructure can keep up with your business growth. Before signing on, evaluate the 3PL’s existing logistics operations—are they set up to store, pack, and efficiently pick orders while accommodating a rise in inventory? Additionally, ask about the cost and if any steep start-up fees come into play. While upfront costs may seem high, future savings may be unlocked when you consider what is included in the quote – from less overhead to lower labor costs down the line. Ask your 3PL vendor what reporting capabilities they offer; this allows you to track areas such as order accuracy and timeliness of deliveries, along with any potential risks or liabilities associated with broken or lost items. You’ll also want to confirm that 3PL integrates well with your existing inventory, order management, and warehouse management software for a smooth transition into 3PL services. Are you looking for warehouse software that works for 3PLs? ShipHero’s warehouse management system comes with integrations plus real-time reporting, the perfect combo for staying ahead of the future of your business!
Third Party Logistics Advantages and Disadvantages
The 3PL infrastructure, which is tailor-made for the e-commerce industry, makes it easy for small to medium-sized businesses to launch their products worldwide and scale up their operations on demand. However, 3PL isn’t entirely sunshine and rainbows – there can be hiccups ranging from extra fees to lags in shipping standards. As always, it’s important to weigh the advantages and disadvantages of 3PL in your decision-making process before investing time and energy into outsourcing logistics.
Advantages
1. Better Shipping Rates
When many brands join forces and leverage the volume of their orders, they can negotiate better rates from carriers. That’s why 3PL providers are so great: You may be small in number alone, but together you’ll get heard loud and clear for discounted prices that lead to greater profits per order.
2. Decreased Shipping Time
So how do you compete with Amazon Prime to get packages to customers? Building tons of warehouses across the country might be expensive, but you can hit that two-day mark without breaking the bank by using a 3PL.
3. Real-time Transparency
Real-time transparency gives brands the advantage of being in direct control: accurately stocked shelves and order status updates that come lightning fast. With paperless warehouse operations and Tier 1 WMS data at your fingertips, you can keep a refreshed eye on every detail – from macro to micro!
4. Strategic Partnership Networks
Instead of relying on a go-it-alone approach, tap into 3PLs strategic partnership networks to get your hands on solutions specifically made for you. From integrated tools and offers to highly customized experiences—you can make it happen with these trusted partners!
Disadvantages
1. Upfront Investment
It’s clear that when it comes to 3PL providers, there’s no free ride – you’ll have to pay the piper for setup costs such as software integration, SKU uploads, and account access.
2. Hours or Workflow
Instead of packing your orders, wouldn’t it be nice to have a third party do the job for you? But beware – working with 3PLs means relying on their hours and workflow. It’s best to plan ahead when engaging such services, as any disruption could lead to hiccups in delivering your goods.
3. Finding a 3PL You Can Trust
Choosing the right 3PL partner isn’t just about getting a good deal – although that doesn’t hurt. You’ll have to put in some homework and carefully vet reviews, size, reach, and service offerings before you can confidently shake hands with your ideal 3PL provider!
ShipHero is a Shopify Third Party Logistics Partner!
ShipHero, with 3PL infrastructure and software that seamlessly integrate with Shopify and Returnly (to name a few), is undoubtedly a 3PL partner you’ll want to know about. With ShipHero’s one-stop shop for 3PL services, you can rest easy knowing that your inventory will always be on track. And saving money? That’s a no-brainer! Thanks to real-time ship rate shopping and built-in reporting features that cover COGS, picker/packer efficiency, replenishment, and more… we might be the best 3PL for Shopify you have ever tried!
3PLs: The Backbone of Supply Chain Management
3PLs are often the unsung heroes of a shipper’s operations, providing an invaluable infrastructure to help them track inventory, orders, and logistics with greater precision and certainty. Their solutions offer robust analytics, machine learning capabilities, and automated toolings for pricing, booking, and documentation, allowing shippers to make better decisions backed by fact-based data quickly. Despite the apparent advantages 3PLs present to businesses of all sizes, many fail to take advantage of 3PL tech solutions. As 3PLs have become essential in managing supply chains, it is time for shippers to reevaluate 3PL advantages and disadvantages and prioritize using their 3PL business relationships more effectively to stay one step ahead of their competition. 3PLs are the future of eCommerce. By tapping into their infrastructure, you can level up your customer service while saving money on warehousing and transportation.
Nov 12, 2021 | Blog, Fulfillment, Warehouse Management Software
Technology and automation have dramatically streamlined modern business processes. The logistics industry in particular has grown tremendously thanks to modern advancements. Despite the power of technology though, eCommerce brands still need to have effective inventory management systems in place to optimize their order fulfillment processes.
To optimize your inventory management, it’s important to use a combination of the best practices and industry-leading software solutions. By streamlining your inventory management, you can cut back on unnecessary expenditure, fulfill orders quicker and increase your bottom line.
How to Create an Inventory Management Process That Just Works
Here are the best practices for creating an inventory management process that works for every successful business.
Data is Your Hero
Accurately reporting your relevant inventory data is a vital part of an effective inventory management system. All the data including your beginning inventory, how many finished inventory items were shipped out, your cost of goods sold (cogs), product returns, deadstock, and inventory quantity need to be accounted for.
To report data accurately, your team needs to be actively engaged in supply chain management. Make a point to count inventory and compare the value with the figure on the GRN (Goods Received Note). If you deal with perishable items, you need to be especially careful about expiration dates. You should pay attention to any stock damage or returns and keep a comprehensive written record.
Implement a Warehouse Management System
A warehouse management system is a collection of software and processes that enable a business to control and monitor all operations within the warehouse.
A warehouse management system gives businesses real direction and control over their warehouse processes. With a system in place, you can optimize each process and use analytics to monitor performance.
Warehouse management software lets you monitor assets from the time they’re delivered from the manufacturers to the time they reach your customers.
A strategic warehouse management system streamlines restocking and logistics operations and uses demand forecasting tools to balance your inventory levels. WMS software tools take care of important calculations like your economic order quantity.
They also integrate well with any system, whether it’s the periodic inventory system or the perpetual inventory system.
Or Work With a 3PL
As your eCommerce store grows, keeping up with order fulfillment becomes increasingly difficult. Brands reach a point where to keep up with demand, they have to decide whether to:
- Hire more, specialized logistics personnel to handle the increasing demand.
- Hire less experienced staff and train them up.
- Work with a third-party logistics provider (3PL).
Initially, many businesses shy away from option (3) because of the significant upfront costs. However, in the long run, the third option cuts back your expenses and optimizes your fulfillment process.
With option 1, the costs of hiring specialized personnel add up. Moreover, as your brand continues to grow, you might have to hire even more employees to keep up with the demand.
On the other hand, option 2 puts you at risk of heightened expenses due to inexperienced team members and more mistakes. An inexperienced team translates to delays and incorrect orders.
Third-party logistics (3PL) providers, on the other hand, give you access to a team of experienced professionals without you having to pay salaries and benefits. They’re partners; not employees. About 86% of Fortune 500 companies and 96% of Fortune 100 companies use 3PL services.
Audit your Existing Inventory Management Processes to Discover and Analyze Issues
An audit of your management processes identifies problems that you can improve to streamline inventory processes.
For example, is your picking team finding it difficult to locate items? Then it’s time to organize your inventory better. A ratio analysis where you compare your current financial year to the last helps identify potential performance issues too.
If last year’s numbers were better, you might be losing revenue on unnecessary expenses, like storage costs due to overstocking.
After discovering problems in your management processes, you can take proactive steps to solve them and streamline your fulfillment process.
Implement an ERP
An enterprise resource planning (ERP) system is software designed to help organizations manage their daily business tasks. An ERP can manage a multitude of business activities ranging from accounting and HR to risk management and supply chain operations.
You can move your financial data over to the software after installing it. The inventory software is then free to organize warehousing operations and manage inventory logistics.
With an ERP, you can monitor your operations through your mobile devices, and the software facilitates integrations with popular eCommerce applications including eBay, Amazon and Shopify.
Use Multiple Fulfillment Centers
While a single fulfillment center seems more cost-effective because of the reduced storage costs, there are some additional expenses you need to consider.
Having multiple, strategically located fulfillment centers cut down your delivery times and costs. This is because your business can fulfill orders from the center nearest to the recipient. It also means you can offer expedited shipping, which consumers have come to expect as standard practice.
Since small businesses can’t always afford the overheard that follows using multiple centers, many turn to a 3PL provider instead. Leading 3PLs have their own network of distributed fulfillment centers that you can utilize by partnering with them.
Change your Inventory System
It is crucial to choose an inventory valuation method that best aligns with your business model. With the first in, first out method there are certain advantages, such as a reduced risk of obsolete inventory and a reduced inflationary impact.
The valuation method you select can significantly influence your inventory management process. You need to choose one that best suits your business.
The first in, first out (FIFO) method offers certain advantages, like reduced risk of obsolete inventory and less inflationary impact. But some businesses choose to swap from FIFO to methods like JIT.
The ‘just in time’ (JIT) method requires less storage space, because you buy stock on an immediate-need basis. Using this method also means you have working capital to invest elsewhere, rather than having it tied up as stock.
JIT also reduces your chances of overstocking significantly. But, at the same time, JIT doesn’t leave much room for error or delays. If your supplier runs late, and customer orders are coming in, orders may end up delayed or unfilled altogether.
Conclusion
Effectively managing your inventory improves the efficiency of your entire fulfillment process, leading to faster deliveries, accurate orders, reduced costs, and happier customers.
You can optimize your inventory management by implementing the best practices, including leveraging distributed fulfillment centers, implementing an EPR, and taking a data-driven approach.
However, managing your inventory processes isn’t easy, especially if your eCommerce brand is growing rapidly. If you’re struggling with inventory management, ShipHero’s warehouse management software and team of experts can help streamline your operations.
Nov 5, 2021 | Blog, Warehouse Management Software, Warehouse Operations
On average, one out of three businesses miss their delivery deadlines because they just sold a product that’s out of stock. This highlights just how common inventory management issues are. Poor inventory management leads to losses and unhappy customers. Being understocked translates to unfulfilled orders, and excess inventory drives storage and management costs up.
To optimize your order fulfillment process, maintaining your inventory and knowing the best times to re-order are vital. So let’s take a look at common problems to steer clear of, and some solutions to your inventory management issues.
Common Issues with Inventory Management
Some persistent inventory management issues afflict most businesses at some point, which include:
Products Consistently Running Out of Stock
Running out of products consistently is a result of inefficient inventory management. Failing to set accurate reorder points and stock up on in-demand products leads to shortages, which translates to unfulfilled orders.
If you run out of in-demand goods, not only are you losing revenue from potential sales, but your customers may start purchasing from competitors.
Incorrect Demand Forecasting Leads to Inventory Shortages or Too Much Inventory
The idea behind demand forecasting is to analyze industry trends and predict what your inventory levels should be. If a product’s popularity is expected to pick up soon (like chocolates during Valentine’s Day) or decrease soon (like air conditioners towards the end of summer), demand forecasting helps prepare your inventory accordingly.
However, inaccurate demand forecasting causes more problems than it solves. Incorrect predictions throw your stock levels off balance; you may end up overstocking or understocking, inviting respective consequences.
Companies Forget to Re-order Products
Forgetting to re-order products leads to shortages and consequently, unfilled orders. If you don’t have a proper inventory management system in place, forgetting to re-order from suppliers might happen frequently.
How the Inventory Turnover Ratio Affects Inventory Management
Your inventory turnover ratio typically indicates how strong or weak your sales are at a given time.
What is the Inventory Turnover Ratio?
The inventory turnover ratio is an efficiency ratio, and it’s also known as stock turnover or inventory turns. The metric measures how efficiently your brand manages its inventory. The calculation determines the rate of sales and restocks of a particular product during the fiscal year. Your company’s inventory turnover can indicate inventory performance; a high turnover ratio generally means strong sales, while lower inventory turnovers might be due to overstocking.
How to Calculate Inventory Turnover Ratio
You can calculate the inventory turnover ratio by using the inventory turnover formula:
cost of goods sold (COGS) / [(beginning inventory + ending inventory)/2]
Here, the beginning and ending inventory is divided by 2 to calculate the average inventory. Moreover, the average inventory is taken over a particular time period. Alternatively, you can calculate the ratio by dividing sales instead of COGS by the average inventory value. However, since sales include a markup, this method is generally not as accurate.
How to Analyze Inventory Turnover Ratio
The inventory turnover ratio assesses how your rate of sales aligns with your warehouse restock rate. Thus, the ratio actually indicates how efficient your inventory management system is.
To analyze your turnover ratio, important factors to consider include:
- The industry standard as a benchmark to monitor your performance. Low-margin industries generally have higher inventory turnover ratios.
- Cost flow assumptions can cause fluctuations in the turnover ratio, but you don’t necessarily need to have a course of action for them.
- The valuation method you’re using affects your inventory turnover calculation, and thus the result. For example, using LIFO over FIFO generally produces a higher stock turnover, courtesy of the higher cost of goods sold (cogs) with a lower inventory value.
What is an Ideal Inventory Turnover Rate?
What qualifies as a ‘good’ inventory turnover rate largely depends on the industry. You can estimate how healthy your turnover rate is by comparing it to the industry standard. Then, you can better understand your inventory’s success by comparing your turnover rate and seeing if it’s higher or lower.
Low Inventory Turnover
A low inventory turnover generally means your brand is underperforming because it indicates either surplus stock or a lack of sales. However, if you’re expecting shortages or a price hike on the goods soon, then a low turnover rate is beneficial. It means you’re holding out for a better time to sell.
Otherwise, low turnover rates are usually caused by at least one of the following factors:
- Overstocking
- Liquidity problems
- Weak sales
- Failed marketing efforts
- Inefficient inventory management
High Inventory Turnover
In most industries, a high inventory turnover ratio is generally a positive indicator. It means your products are selling well, and you’re successfully restocking every 1-2 months.
The ideal inventory turnover ratio is generally between 5-10 and varies across industries. Generally, high inventory turnover indicates improved liquidity, efficient inventory management and strong sales.
However, inadequate inventory or stock shortages also lead to higher inventory turnovers, so you need to assess the contributing factors.
5 Ways to Improve Inventory Management
If you’re looking to improve your inventory management, here are five of the best practices.
Leverage Product Bundles
Product bundling is a technique of grouping multiple products or services and selling them as a single unit. It’s a simple strategy to reduce marketing and distribution costs while guaranteeing a higher average order value (AOV).
You can lump multiple products together, including high and low ticket items, and sell them at a reduced cost. Since you don’t have to market each item individually, the profit margin is still appreciable.
You can also leverage product bundles to sell off slow-moving inventory. Deadstock takes up storage space and drives storage costs up, so pairing a few unwanted items with some in-demand ones can rid you of the excess inventory.
Adjust Product Pricing
Adjusting your pricing strategy helps keep inventory levels balanced by combating both understocking and overstocking problems. If you’ve got too much inventory to manage, dropping the prices on certain products helps you sell them out faster and reduce storage costs.
Alternatively, if you’re understocked, you can increase the prices of the items to temporarily reduce demand. When your inventory is restocked, you can drop the prices again.
Make Use of Automatic Re-orders
Manual reorder processes invite inaccuracies and your personnel may forget to place the orders altogether.
You can leverage inventory management software to set accurate, automatic re-order points, based on real-time inventory levels and demand forecasting. With automatic reorders, you mitigate the risks of running out of inventory or overstocking.
Streamline the Supply Chain
Inventory management is just one stage of your supply chain; by optimizing the processes before and after it, you can collectively streamline distribution and fulfillment efforts. This involves optimizing stocking times, organizing inventory, reducing picking and packing times and improving the delivery process.
Work with a 3PL
Third-party logistics providers help streamline your entire order fulfillment process, including warehouse and inventory management, picking, packing and delivery.
SMBs in particular benefit from working with 3PLs because they don’t have to hire their own, specialized logistics team. 3PL providers optimize your fulfillment process, improving your customer’s experience and reducing unnecessary costs.
Working with a 3PL also guarantees transparency, because unlike with a 4PL, you retain ultimate control. Leading 3PLs also have their own software to give their partners updates and a transparent view of their operations.
Conclusion
Inventory management issues affect your bottom line, leave your customers unhappy and may overwhelm your workforce too. By implementing the best practices, you can mitigate inventory management issues and streamline your workflow.
As your eCommerce brand grows, managing your own inventory becomes increasingly challenging. You have more orders to fill, a larger and geographically diverse customer base, and your employees struggle to keep up with the logistics.
Sep 27, 2021 | Blog, Warehouse Operations
One day, robots will run most functions within a warehouse. Outfitted with the latest in artificial intelligence, they’ll be able to manage warehouses very efficiently. However, we’re not there yet. In the interim, you have to find technologies that can give you more flexibility and agility, while making the lives of employees and customers better.
Automation is the Big Umbrella
Underlying all technology in a warehouse is automation. Automated processes, tools and machines make your daily warehouse life easier. Warehouse management software (WMS) has grown in its functionality over the past 10 years, often incorporating some of the latest technologies to make running your business more efficient. No doubt you already use some of these features in your warehouse operations. Let’s examine a few different aspects of this type of automation and identify ways to know if your organization is ready for it.
Software Automation
At the center of any warehouse automation is WMS. It is the engine that makes your warehouse technology run. Without the right software in place, automated processes wouldn’t be possible.
This is true because WMS incorporates a wide range of your warehouse processes, including receiving and put-away, inventory management, order fulfillment, picking and packing and shipping. In every step, there is an algorithm or a program or an advanced piece of machinery that makes things more efficient and each of these is controlled by WMS.
Physical Automation
Since the invention of the conveyor belt, workers and companies have been automating physical procedures in the modern warehouse. Conveyors, lifts and other machines that work to make warehouse employees’ lives easier are the first step in warehouse technology, often referred to as basic automation. These are the types of tools and features you would expect to see in any modern facility.
Other common automated tools include barcode scanners and smart devices. Each was designed to streamline warehouse and eCommerce fulfillment processes to reduce errors.
However, more advanced technology has brought more advanced automation with things like automatic pickers and labeling machines. The most recent introduction and perhaps the most progressive of these technologies is autonomous robots. These can include everything from shelf loaders to forklifts with sensors so that they can operate without human supervision.
There is the concern that so much automation and the advancement of robotics and artificial intelligence could lead to reduction in the workforce. A recent article in MIT Technology Review, discussed this topic, and concluded that while that may eventually happen, there is still a large gap between the number of warehouses that have robots and the ones that don’t.
The adoption process is steady, but slow. Additionally, companies view the role of human workers changing in this new workplace, moving from manual labor to more oversight and maintenance of the machines. So, you’re probably not going to lose your job to a robot, you’re just going to end up doing something different.
Committing to Automation
Automating warehouses comes with an upfront cost that is off-putting to many business owners. Especially since the true benefit of the automation won’t be felt for a few months or a year until after implementation. However, there are some tell-tale signs that your company is ready to take the plunge. Review the list below and see if any of these instances apply to you and your organization.
- You’re still using a legacy warehouse management system that relies on manual inventory counts that are housed in spreadsheets.
- Your order fulfillment capacity is declining.
- Your warehouse processes and procedures are labor-intensive.
- Your inventory counts are always inaccurate.
- You’re receiving negative feedback from customers regarding shipping delays.
- Your total number of employees fluctuates due to high/low demand or seasons.
If any of these sound like your organization, it might seriously be time to investigate WMS options. In the long run, increasing customer satisfaction, ensuring employee morale and maintaining accurate inventory counts will lead to more success across the board; and higher revenue.
Embrace Automation
There has always been a slight resistance to technology. However, it has become apparent in the past decade that in order to be competitive, successful and profitable you must adopt technology and automation to its fullest extent. If you’re ready to do so, ShipHero is ready to help.
Jul 3, 2023 | Blog
The Top 10 Best 3PL Companies for Consumer Electronics
Client-focused innovation has been a driving force in moving the consumer electronics industry forward so fast that it has outstripped many businesses’ capabilities to handle logistics operations effectively. This situation pushes many organizations towards seeking help from external third party logistics (3PL) providers that can meet these critical supply chain needs while preserving quality standards. But how can we know which 3PL provider is reliable? This article aims to provide readers with our top picks in the business and essential criteria before making an informed decision.
What is 3PL?
Before getting into details about our list of recommended providers let’s have a brief reminder about what third party logistics (3PL) providers are used for; when outsourcing logistics or supply chain activities – companies enlist specialized companies for core tasks like warehousing, inventory management or transportation duties among others.
What is Consumer Electronics?
Consumer electronics are everyday products fashioned from high level technology such as smartphones or home gadgets that typically endure high speed changes rendering product inventories challenging to manage while precise distribution involves maintaining product quality standards at every turn.
An Overview of the Electronics Industry
The electronics industry is vast and includes different sub-industries ranging from audio/visual equipment to telecommunications infrastructure. It thrives off innovation, and even demands innovation from the companies within its industry. This evolution requires both fast adaptation coupled with business creativity, which pushes them into pressure zones where only highly skilled and fast-paced businesses thrive. They cannot slow down, which is why they need top-notch 3PL services.
The Role of 3PL in the Electronics Industry
Why Choose 3PL for Your Electronics Business?
By partnering with dedicated third party logistics providers. Businesses are given opportunities to level up their supply chain and focus on finalizing core operations. In turn, this gives rise to improving productivity levels and ultimately increasing business success by meeting customers’ evolving market demands. The electronics industry faces unique challenges that require specialized expertise to manage effectively. As such partnering with a third party logistics (3PL) provider can bring valuable benefits to businesses in this sector.
3PL Services Provided for Electronics Companies
3PL providers offer a comprehensive range of services tailored to meet the specific needs of electronics companies. These services include:
- Warehousing and Distribution
- Order Fulfillment
- Inventory Management
- Reverse Logistics
- Customized Packaging
- Kitting
- Transportation and Freight Management
- Inventory and Shipment Tracking Tools
- Customer Service
- Returns Logistics
Top 10 3PL Companies for Consumer Electronics
Shiphero
ShipHero offers comprehensive fulfillment services, including inventory management, order processing, and shipping. Their technology-driven approach and scalable solutions make them an ideal choice for consumer electronics businesses of all sizes. Need to chat with a fulfillment expert? Shiphero is here to help!
Red Stag Fulfillment
Red Stag Fulfillment specializes in handling large, heavy, or fragile consumer electronics products. They have advanced warehousing capabilities and stringent quality control measures to ensure safe and accurate order fulfillment.
Fulfillment.com
Fulfillment.com offers global fulfillment services, making them an ideal choice for consumer electronics businesses with an international customer base. They provide fast and cost-effective shipping solutions worldwide.
IDS Fulfillment
IDS Fulfillment specializes in customizable fulfillment solutions. They offer services such as kitting, assembly, and customization, making them suitable for consumer electronics businesses with unique packaging or assembly requirements.
Fulfillment Works
Fulfillment Works offers a wide range of fulfillment services tailored to consumer electronics businesses. Their services include inventory management, order processing, kitting, and customization, enabling businesses to meet specific customer requirements.
Ruby Has Fulfillment
Ruby Has Fulfillment provides comprehensive fulfillment solutions with an emphasis on technology and scalability. Their advanced order management system and robust analytics help businesses optimize their operations.
Shipfusion
Shipfusion offers technology-driven fulfillment services, including real-time inventory visibility and integrated shipping solutions. Their automation capabilities and data-driven insights improve efficiency and customer satisfaction.
Fulfillrite
Fulfillrite focuses on providing fast and accurate fulfillment services. With their expertise in order processing and shipping, they help consumer electronics businesses meet customer expectations for timely delivery.
ShipCentral
ShipCentral specializes in scalable and cost-effective fulfillment solutions. Their services include inventory management, order processing, and shipping, enabling consumer electronics businesses to streamline their operations.
Fulfillment Bridge
Fulfillment Bridge offers global fulfillment services with a focus on fast and reliable shipping. They have a network of fulfillment centers worldwide, providing efficient order processing and international shipping options.
Challenges in Fulfilling Consumer Electronics
Fulfilling consumer electronics comes with its own set of challenges that businesses need to navigate successfully. Let’s explore some of the difficulties involved in fulfilling electronics orders and how partnering with a reliable 3PL provider can help overcome them.
Managing Various Types of Electronics
Consumer electronics encompass a wide range of products with different sizes, shapes, and fragility levels. Effectively managing the diverse inventory requires specialized handling and storage solutions.
Handling Returns
The electronics industry experiences a significant number of product returns due to various reasons such as defects, customer dissatisfaction, or compatibility issues. Efficiently managing the returns process while minimizing costs and maintaining customer satisfaction is crucial.
Challenges of the Consumer Electronics Supply Chain and Their Solutions
The consumer electronics supply chain faces unique challenges that can impact the smooth flow of products. Here are a few key challenges and their corresponding solutions:
- Inventory Management and SKU Monitoring: Consumer electronics often have a large number of SKUs, making inventory management complex. Monitoring stock levels, tracking individual SKUs, and ensuring accurate inventory information is crucial to prevent stockouts and improve order fulfillment rates. Leveraging advanced technology and systems provided by a 3PL can streamline this process.
- Safeguarding Inventory in Fulfillment Centers: Consumer electronics are valuable and can be prone to theft or damage. Implementing robust security measures, including surveillance systems, restricted access, and inventory control procedures, can safeguard inventory in fulfillment centers.
- Efficient Returns Management: As mentioned earlier, handling returns in the consumer electronics industry can be challenging. A reliable 3PL can streamline the returns process by implementing efficient reverse logistics strategies, including product inspection, refurbishment, and repackaging, ultimately reducing costs and improving customer satisfaction.
- Handling Spikes in Order Volume: Consumer electronics businesses often experience fluctuations in demand, particularly during product launches, sales events, or holiday seasons. Scaling up operations and managing spikes in order volume can be a significant challenge. Partnering with a flexible 3PL provider ensures the capacity to handle high order volumes efficiently.
Advantages of Outsourcing Electronics Fulfillment with a 3PL
Monitoring Inventory and SKUs
With numerous SKUs and constant inventory movement, monitoring inventory accurately is crucial. A reliable 3PL leverages advanced technology and systems to provide real-time visibility into inventory levels, ensuring efficient inventory management and minimizing stockouts.
Safeguarding Inventory in Fulfillment Centers
Fulfillment centers act as the central hub for storing, organizing, and shipping products to customers. And to ensure inventory security, access control systems and advanced surveillance technologies should be put into place. These, in addition to regular inventory audits, safeguard inventory and minimize losses.
Efficient Returns Management
3PL providers specialize in reverse logistics and have established processes to efficiently handle returns, minimizing costs and optimizing the returns experience for both businesses and consumers.
Handling Spikes in Order Volume
During peak seasons or promotional events, order volumes can skyrocket, putting a strain on internal resources. 3PL providers are equipped to handle such spikes by scaling their operations, ensuring timely order processing, and maintaining high service levels even during periods of increased demand.
How a 3PL Service Enhances Consumer Electronics Business
Cost-efficient, Streamlined, Service-oriented 3PL Services
By leveraging the expertise and resources of a 3PL, electronics companies can achieve cost efficiencies, streamline their operations, and enhance overall service levels. 3PL providers bring industry-specific knowledge, specialized infrastructure, and efficient processes to ensure optimal supply chain management.
Third-Party Logistics and Customer Service
Outsourcing fulfillment to a 3PL allows businesses to focus on core competencies while leaving the logistics and fulfillment tasks to the experts. This enables businesses to provide exceptional customer service by ensuring accurate and timely order fulfillment, effective returns management, and efficient last-mile delivery.
Leveraging 3PL and Digitization for Optimal Supply Chain Management
With the advent of digitization and advanced logistics technology, 3PL providers can offer enhanced visibility, real-time tracking, and data-driven insights to optimize supply chain management.
Considerations for Consumer Electronics Fulfillment
Inventory Management for Consumer Electronics Fulfillment
Effective inventory management is crucial in consumer electronics fulfillment due to the diverse range of products and their varying demand patterns. Implementing robust inventory management practices, including accurate forecasting, SKU optimization, and replenishment strategies, can help businesses maintain optimal stock levels and minimize stockouts.
Role of Packaging in Consumer Electronics Fulfillment
Packaging plays a vital role in consumer electronics fulfillment, ensuring the safe and secure delivery of products to customers. It is essential to use appropriate packaging materials that protect electronics from damage during transit. Additionally, branding and presentation of packages can enhance the overall customer experience.
Benefits of Electronics Fulfillment with a 3PL
Cost Savings on Delivery
3PL providers have established relationships with carriers and can negotiate favorable shipping rates, resulting in cost savings on delivery for electronics businesses. Additionally, their expertise in logistics allows for optimized route planning and shipment consolidation, further reducing transportation costs.
Real-time Updates on Orders, Tracking & Returns
By partnering with a 3PL, electronics businesses gain access to advanced tracking and order management systems. Real-time updates on order status, tracking information, and returns processing provide enhanced visibility and transparency throughout the fulfillment process.
Scaling Your Brand with Confidence
As your consumer electronics business grows, a 3PL can scale its operations to accommodate increased order volumes and expanding customer base. This scalability provides the confidence to grow your brand without worrying about fulfillment constraints.
Solutions for Growth and Efficiency Across Your Business
Beyond fulfillment, a 3PL can offer additional services to support your business’s growth and efficiency. These may include value-added services such as product assembly, customization, and repair, as well as supply chain consulting to optimize processes and identify areas for improvement.
Secure Storage Facilities
Given the value of consumer electronics, it is crucial to partner with a 3PL that offers secure warehousing facilities. Look for providers that have robust security measures in place, including surveillance systems, access controls, and proper handling procedures to safeguard your inventory.

Key Takeaways
Consumer electronics fulfillment presents unique challenges that can be efficiently addressed by partnering with a reliable 3PL provider. Outsourcing fulfillment to a 3PL offers benefits such as cost savings, real-time order tracking, scalability, and access to specialized expertise. So don’t wait. Stop trying to handle orders all on your own and focus on creating efficiency in your supply chain by partnering with the right 3PL for your business!
Frequently Asked Questions
How Does a 3PL Work?
A 3PL works by taking over logistics and supply chain operations on behalf of a business. This includes tasks such as warehousing, inventory management, order fulfillment, transportation, and more. The 3PL provider integrates seamlessly with the business’s operations, leveraging their expertise, resources, and technology to streamline processes and optimize efficiency.
Examples of 3PL for Consumer Electronics
When evaluating whether a 3PL is suited for consumer electronics, there are several key factors to consider. Firstly, the 3PL should have experience and expertise in handling consumer electronics products, understanding their unique characteristics and requirements. This includes factors such as proper handling, storage, and packaging of delicate or valuable electronic devices. Additionally, the 3PL should have a proven track record of accuracy and efficiency in fulfilling consumer electronics orders, as well as effective management of returns and reverse logistics.
Jul 14, 2023 | Blog
eCommerce shipping is a key link of the supply chain that can make or break your business. Think that’s a bit of an overstatement? Well, last-mile delivery is recorded as the most costly part of the order fulfillment process – it’s one of the most pressing logistical challenges. Plus, if order inaccuracies occur, and items are shipped to the wrong location, you’ll have to face the additional costs of returns and refunds.
This is why it’s so important to optimize the shipping process. You need to cut down labor costs, transit times, fuel costs, and establish a seamless workflow. Easier said than done, though, right?
In this guide, we’re going to take a look at how you can optimize the shipping process from different angles. Questions such as how much to charge your customers, what sort of hits your business should absorb, how to protect your own investment, and which data-driven tools to use, will be addressed and answered.
Jul 14, 2023 | Blog
3PL Myths and Misconceptions
There are some common myths and misconceptions when it comes to using a 3PL provider. Here are a few you may have heard:
Myth: “It’s too expensive to use a 3PL.”
In reality, using a 3PL can actually save your business money in the long run. A 3PL has economies of scale and can often negotiate better rates for things like warehousing and transportation. And by outsourcing logistics to a 3PL, you’ll have more time and resources to focus on growing your business, which can ultimately lead to more revenue.
Myth: “A 3PL will take over my business.”
A 3PL is there to support your business, not take it over. The idea is to work together to create a logistics solution that works for you. You’ll still be in control of your inventory and customer relationships.
Myth: “I’ll lose control of my inventory.”
When working with a 3PL, you’ll have access to real-time inventory data, giving you more control and visibility over your inventory than ever before. Plus, 3PLs often have advanced inventory management systems in place, which can help you keep track of your inventory and reduce the risk of stockouts.
Myth: “A 3PL can only handle basic logistics tasks.”
3PLs have a wide range of capabilities, and many offer a variety of services beyond just storage and transportation. For example, many 3PLs can also handle things like order fulfillment, reverse logistics, and even eCommerce integration.
Why Do Companies Choose to Work With a 3PL Provider?
Companies choose to work with a 3PL provider despite the misconceptions surrounding the use of 3PL because it is often the most cost-effective solution for their needs. Not only can 3PLs negotiate better rates for warehousing and transportation, but they have also put in the money to develop a logistical infrastructure. While companies like Walmart might have the capacity to spend the cash required for such an infrastructure, many other companies do not. In addition to this, they are also logistics experts and can help you strategize the best approach for your business.
What Is a Reason for Using a 3PL Logistics Partner?
Let’s go back to Sarah who runs “Fashion Avenue”. Before using a logistics provider, her business was growing quickly, and she found herself spending more and more time on manual tasks. Despite her best efforts, she was struggling to keep up with the volume of orders and was frequently running out of stock. But her day-to-day changed when she decided to partner with a 3PL logistics provider. The 3PL provider was able to take over the handling of her inventory, packing, and shipping orders, and coordinating with carriers. This freed up Sarah’s time and resources, allowing her to focus on growing her business. Ultimately, picking a 3PL logistics provider saved Sarah both time and money. And it can do the same for your business as well.
What Is the Difference Between a 3PL Logistics Partner and a Broker?
A 3PL logistics partner is a comprehensive and integrated solution for your logistics needs, providing a wide range of services such as warehouse management, inventory control, transportation management, and other logistics services. They are a partner in your business and work closely with you to create a logistics strategy unique to your specific needs. On the other hand, a Broker is a middleman who connects shippers with carriers and other logistics providers. A broker is not responsible for the physical handling or storage of goods and typically provides less visibility and control over the logistics process.
What Industries Use 3PL Logistics Partners the Most?
3PL logistics partners are the go-to solution for many industries that require a full-service logistics provider. They rely on the expertise and resources this logistical partner has to offer. Industries such as e-commerce and retail, manufacturing and production, healthcare and pharmaceuticals, food and beverage, automotive, industrial and heavy machinery, fashion and apparel, and chemical and hazardous materials all extensively use 3PL logistics partners to manage their logistics operations.
How Do You Manage a 3PL Logistics Partner?
Managing a 3PL logistics partner effectively is crucial for a smooth and successful logistics operation. You should clearly communicate your logistics needs, goals, and expectations to the 3PL logistics partner, including setting performance metrics and service level agreements (SLAs) that both parties agree on. Performance should be continuously monitored against the agreed-upon metrics and SLAs, and regular data and reports requested to help measure performance, identify trends and make informed decisions.
How Can I Monitor My Third-Party Logistics Partner Performance?
Monitoring the performance of third-party logistics providers is critical to ensure that your logistics operations run smoothly and meet your business needs. So how do you monitor your 3PL partner’s performance?
- Service Level Agreements (SLAs): For example, you might set an SLA that requires your 3PL partner to ship 95% of orders within 24 hours of receipt.
- Key Performance Indicators (KPIs): For example, you might set a KPI to track the number of stockouts, the accuracy of orders, or the on-time delivery rate of your 3PL partner.
- Data and reporting: You could request a report that shows the number of orders shipped, the number of orders with errors, or the average time it takes to ship an order.
- Audits and inspections: These will help you identify issues and ensure the 3PL is following your agreed-upon procedures and standards.
Key Takeaways
Your business and your customers deserve the best. They depend on you to get their orders shipped on time and in one piece. Moving to a third-party logistics company for these needs allows you to keep your promises to those who buy your products. With this partnership, your orders can get there faster, with fewer mistakes, at a lower cost than if you were trying to achieve the same on your own. Meaning a 3PL solution is your ticket to keeping up with the competition!
eCommerce Integration With 3PL FAQs
How Do You Integrate With 3PL?
Integrating with a 3PL logistics provider is a process that requires clear communication, collaboration, and planning. Start by reviewing your logistics needs, goals, and expectations with the 3PL logistics partner, including setting performance metrics and service level agreements (SLAs) that both parties agree on. Have a plan which outlines the logistics processes and procedures and includes details such as inventory management, shipping, and returns. Finally, monitor the performance of the 3PL logistics partner against the agreed-upon metrics and SLAs, and look for opportunities for improvement.
What is 3PL in eCommerce?
A 3PL will handle the warehousing, shipping, and fulfillment of orders for an eCommerce business. This can include tasks such as receiving and storing inventory, picking and packing orders, and arranging for shipping and delivery. Using a 3PL provider can also help eCommerce businesses focus on their core business, such as product development, marketing, and customer service, instead of worrying about logistics operations.
What Are eCommerce Integrations?
eCommerce integrations refer to the connections and links established between an eCommerce platform and other software systems or tools used to manage and run an online business. These integrations can help automate and streamline business processes. Here are a few examples of eCommerce integrations:
- Payment gateways: PayPal, Stripe, Square
- Shipping and logistics: FedEx, UPS, DHL
- Inventory management: ShipHero, TradeGecko, Stitch Labs, Brightpearl
- Marketing automation: Klaviyo, Constant Contact
- Accounting and finance: QuickBooks, Xero, Zoho Books
- Customer relationship management (CRM): Salesforce, HubSpot, Pipedrive
- Dropshipping integrations: Oberlo, AliExpress, Spocket
Jul 14, 2023 | Blog
The secret to success with any eCommerce business is to keep your customers happy. Rapid order fulfillment, free shipping, and excellent customer service are some of the best ways to do that. When determining an eCommerce business plan, many fail to factor in (or underestimate) product returns.
Returns are a necessary evil for any eCommerce business, and if you don’t handle them properly, they could swiftly break you. Frequent returns negatively impact your profit margins but also destroy conversion rates, bring down customer loyalty, and threaten the survival of your business as a whole. Developing and enforcing a strong returns policy is a must if you want your business to be successful. Counteracting return fraud should also be a focus to further prevent lost profits.
In this article, we’ll cover the ways in which your return policy impacts sales and how to change your policy to benefit your business. We’ll also cover some of the best eCommerce return practices to make sure that returns don’t ruin your business.
How Do eCommerce Returns Affect Your Profitability?
To a certain degree, keeping your customers happy is about transparency. Customer expectations in the world of online shopping are high considering they can switch to a competitor’s site or Amazon in just a few seconds.
The customer experience in today’s world is critical to success. Your customers want to know that the products they are purchasing are of the highest quality and they are getting the best value for their money. Customers want to know their order will be processed quickly and efficiently and that they can contact customer service with questions or concerns, which will be resolved in a timely manner. They also want to know what your return policy is upfront, before clicking “buy”.
Your eCommerce return policy affects your business more than you may realize. According to research, about 67% of online shoppers will check a company’s return policy before buying. What do customers like and dislike about return policies? Let’s take a look:
- About 80% of consumers surveyed expect free returns.
- Only 25% of online merchants offer free returns.
- Over 83% of consumers read a company’s return policy before buying.
- About 71% of customers decide not to purchase when restocking fees are charged for returns.
As an eCommerce business owner, you need to account for all variables when it comes to profitability. While it might cost your company money to offer free returns, doing so could, in turn, boost your sales. In fact, customers are twice as likely to make a large purchase (over $1,000) online if free returns are offered.
To give you an example of what a good return policy can do for your business, consider the Zappos model. They were the first eCommerce retailer to offer a 365-day, free two-way shipping, and returns policy. What’s more, the free return shipping policy allowed customers to return their shoes for any reason. This was absolutely unheard of in 1999.
According to Zappos’ VP of Services and Operations, the company’s best customers have the highest return rates (up to 50% of everything they purchase) but they also spend the most money which makes them the company’s most profitable customers. At first glance, it may sound like their return policy is hurting business but, over time, those loyal customers end up spending more, which offsets their returns.
Simply put, a lenient return policy (when properly executed) can make a huge difference for your business and for your profit margins by creating a more loyal customer base.
What Really Drives Returns?
In order to improve your returns policy, you first need to gain a better understanding of who is returning your goods and why. Here are some of the most common reasons for returns:
- Damaged Goods – Items arrive at the customer’s door having been damaged prior to or during the shipping process.
- Mis-Delivered or Undelivered Goods – Items fail to arrive at the desired destination.
- Malfunctioning Goods – Items arrive at the desired location but do not work properly.
- Gift Returns – Items are received as gifts and returned by the giftee if they don’t want the product.
- Exchanges – Items are exchanged for another item.
- Inaccurate Description – Items received are not as described, either in terms of size or style.
- Changed Mind – The customer simply changed their mind about the product.
In addition to identifying why certain items are being returned, it is also helpful to develop customer profiles to determine who is making the most returns and how to prevent it from damaging your business. For example, some customers intentionally take advantage of lenient return policies by purchasing items to wear once and have no intention of keeping them after. There are also others who order multiple sizes and options for the sole purpose of trying them on at home.
Having developed a better understanding of your customer base and the most common reasons for returns, you can now work on developing a stronger return policy.
Tips for Developing a Hassle-free Returns Policy
Now you understand that the majority of customers will check a company’s return policy before making a purchase. It is also important to note that nearly 50% of customers will continue buying from a company if they have a hassle-free return policy. So, how do you create a return policy that improves your profit margins while also retaining your customers?
Here are some simple tips to help you develop a strong return policy that wins over customers while keeping return rates low:
Offer Returns in a Specific Time Window
Your customers want to know that if they aren’t satisfied, they’ll be able to return the item easily. For example, if you sell footwear, your return policy can state that all shoes can be returned within 30 days if they’re still in good condition.
Keep your Return Policy Clear and Concise
A clear return policy makes it easy for customers to understand which products can be returned and which can’t. If you have products that have a separate return policy, be sure to list them on the product page so customers are aware of any special return policies.
Make your Policy Easy to Find
Your customer shouldn’t have to search for it. A strong return policy should show that you stand behind your product to instill confidence in your business to build trust with the consumer.
Never Copy a Return Policy from Another Company
You should personalize your return policy to your business and products. While there are templates available to help you craft a return policy, they’re meant to be customized to your brand’s unique return policy.
Try to Keep the Language Light
Avoid phrases like “you must” and “you are required to.” You want your returns process to be easy, not scary.
Set Clear Expectations
Some customers expect immediate refunds or a gift card when returning a product. Your return policy should list out the steps involved during the return process so they know how it all works. Make it clear whether you offer an exchange for returned products or if you provide store credit or a full refund.
The bane of any online retailer’s return policy is deciding between full refunds or store credit. While there is no one clear answer as to which one to choose, we recommend surveying your customers to see what they’d prefer.
Provide Specific Return & Exchange Instructions
Tell the customer whether they need to use the original packaging or if they can use their own. Tell them if they need to include the order slip and if they can print a return label online.
Educate your Staff
If they understand the return policy, they can communicate it to your customers quickly and efficiently. If your staff is confused about the returns policy, it could lead to negative interactions with customers when they try to return products.
No company is perfect but having a strong returns policy will prevent returns from destroying your business. Even with a strong policy, however, you should be prepared to take a hit now and again. If you make a mistake with shipping or packaging, you may be forced to eat the cost yourself for the sake of keeping your customer happy. Unlike physical stores, customers can’t just walk in and return a product at no cost to you. Always keep the customer and your long-term bottom line in mind.
What About Reverse Logistics?
The term reverse logistics is sometimes used interchangeably with returns, but they are not quite the same. Technically speaking, reverse logistics refers to monitoring the life-cycle of a product after it arrives at the customer’s door. This includes the ways the product can be reused, how it should be disposed of, and other ways to create value with an expired product – it also involves the return of products from the end consumer back to the manufacturer.
In order to develop a reverse logistics procedure, you need to first think about the different stages a product goes through during a return. First, you’ll need to consider the physical shipping of the returned product – how you will get it from the customer back to the warehouse. Next, you may need to test the returned item to identify existing flaws and document any problems. Then, you’ll need to repair, recycle, or restock the item.
To help you get a better understanding of the reverse logistics portion of your company’s supply chain, there are four key analytics to consider:
- Volume – Take a look at which products are being returned most often – if it’s a large volume of the same products, you may need to consider a recall or making changes to your production.
- Percent of Sales – What percent of your net sales is lost to returns and how many of the returned items can be reincorporated back into your inventory?
- Product Condition – See if you can identify a pattern of failure or malfunction to determine what is going wrong with the product and what condition it is in when it is returned.
- Financial Value – Are the returned products able to be recycled or resold? Think about ways to use returned items to minimize the blow to your profit margins.
Once you’ve gathered this information, you can gain a deeper understanding of your company’s reverse logistics and use that information to optimize your workflow. Improving the efficiency of your reverse logistics system provides numerous benefits, including the following:
Reduction in related costs
When you plan ahead for returns and implement a system to ensure that orders are fulfilled correctly, you can minimize related costs for administration, shipping, quality assurance, tech support, etc.
Faster processing
By implementing a reverse logistics system, you can increase the speed with which orders and returns are processed which keeps your customers happy.
Improved customer retention
A poor return policy can prevent a customer from coming back, but a strong policy instills confidence in the brand and makes customers more likely to purchase again, even after you’ve made a mistake.
Recoup your losses
By using a reverse logistics system to gather data on returns, sellers can decide how best to use returned products to reduce losses. You could fix and restock the product, scrap it for parts, or repurpose it in another market.
Final Thoughts
Handling returns in a quick and efficient manner is the key to keeping your customers happy. With a strong returns policy, you can minimize the damage caused by shipping errors, manufacturing defects, and other issues that necessitate a customer return. When your customers feel like they can trust your company to correct errors in a timely manner, they will be more likely to become repeat customers.