Mar 28, 2023 | Blog
The journey of goods from stores to your doorstep for same day delivery, often involves the delicate dance of shipping and handling. If you’ve ever been in a situation where you needed something delivered urgently, you’ve likely encountered the term “expedited shipping.” In this blog post, we delve into the world of expedited shipping to bring you a comprehensive understanding.
Expedited shipping is a term used by couriers and delivery services to describe a delivery process that is quicker than regular shipping or standard ground shipping. To give you an idea, think of it as ordering food at a restaurant but needing it faster than usual. You’d pay extra money for the speed, and expedited shipping works much the same way.
The Expedited Shipping Timeline
Delivery times for expedited shipping can vary quite a bit. The size of your package, the destination it’s being sent to, and the other expedited shipping speed of delivery or service you’re using can all play a part. Generally, however, you can expect your expedited shipment to take anywhere between 1-3 business days – a much shorter frame compared to regular ground shipping.
An interesting thing to note is that during expedited shipping services, drivers often make fewer stops, ensuring that packages get to their destinations as quickly as possible. The fewer the stops, the faster the journey.
Determining Expedited Shipping Rates
Expedited shipping rates can be influenced by several things. The shipping rates set by a variety of delivery services like USPS, couriers, or your local post office are one factor. These rates can depend on anything from the size and weight of your package to the shipping cost of the destination it’s going to.
But there’s more to it than average order value. For additional examples, some stores promise their shoppers free expedited shipping, at a flat rate, regardless of the order value. Often, discreet shipping might be offered as an add-on for the customer at an additional charge. While this could potentially cost the store money on larger orders, it could boost sales by offering an attractive convenience to the buyer. On the other hand, smaller orders might work out in favor of the store, balancing out the costs.
Additionally, businesses can sometimes negotiate discounts with shipping providers based on volume, adding another layer of complexity to shipping costs.
The Value Proposition of Expedited Shipping
Is expedited shipping worth it? The answer isn’t a one-size-fits-all. From a buyer’s perspective, if they need a product urgently, the expedited shipping option makes perfect sense. There’s also a psychological element to consider when offering expedited shipping – the quicker people get their goods, the more likely they are to become repeat shoppers.
From a business standpoint, these expedited shipping options can give them a chance to gain a competitive edge. If their competitors are offering this offer free expedited shipping service and they aren’t, they could miss out on chances for additional sales. They need to weigh this against the additional handling required and the potential for delays that might harm their reputation.
Expedited Shipping for International Orders
Expedited shipping isn’t just for domestic orders – it can also be used for international ones. Of course, this often comes with higher costs due to the need for customs clearances and the handling of additional documents. Delays might also be more common with express delivery or expedited shipments due to the workings of the post office in certain countries.
However, for time-sensitive items (for example, certain documents or perishable food items), offering expedited shipping or international shipping might be the only feasible shipping option.
Certainly! Here’s a revised version based on your instructions:
Technology and Expedited Shipping: How is Technology Used in Expedited Shipping?
Tracking Systems: Technology in expedited express shipping includes real-time tracking. Customers can see where their package is at any moment. It’s quick and clear.
Route Planning: Software plans the fastest routes, considering things like traffic. This makes shipping faster.
Warehouse Automation: Robots in warehouses pick and pack orders. This speeds up shipping.
AI Customer Service: AI chatbots answer questions about shipping right away. Customers get quick answers.
Ecommerce Integration: Online stores offer fast shipping options at checkout. It’s simple and fast.
Drones: Some companies use drones for delivery. They’re fast, especially in busy areas.
Technology makes standard and expedited shipping faster, quicker and more reliable.
Case Studies and Real-life Examples: What are Some Real-life Examples of Expedited Shipping?
Amazon Prime: Amazon’s quick shipping service is a famous example of the many expedited shipping services. They use many methods to ship fast.
Medical Industry: Hospitals use the expedited services for shipping for things like organs. Any delay can be a big problem.
Small Businesses: Some small businesses use fast, shipping and delivery services to compete with big companies. It makes customers happy and loyal.
Disaster Relief: Fast shipping helps in disasters by moving things like food and medicine quickly. It can save lives.
Failures: Some companies have problems with fast shipping. These stories teach other businesses what not to do.
Impact on Small Businesses: How Does Expedited Shipping Affect Small Businesses?
Small businesses often face unique challenges when it comes to expedited shipping. Unlike large corporations, they may not have the extensive infrastructure or bargaining power to get reduced rates. Every cost from shipping labels to inventory storage costs is a big deal for them. However, offering expedited shipping can be a way for small businesses to attract and retain customers by meeting their immediate needs. They might collaborate with larger carriers or find local courier services that specialize in fast delivery. By exploring these various expedited delivery options, small businesses strive to find a balance between the extra cost of expedited shipping and the potential increase in customer satisfaction and loyalty.
Carrier-Specific Practices: What Methods do Different Shipping Companies Use for Expedited Shipping?
Each shipping company, whether it’s a major global carrier like FedEx and UPS or a smaller local service, handles expedited shipping differently. Large carriers often have specific services tailored for rapid delivery, leveraging their vast networks and resources. Smaller companies might rely on personalized service and local knowledge to provide fast shipping. There’s a wide variety of services, pricing models, and guarantees across different carriers. Understanding these differences helps customers and businesses choose the right affordable expedited delivery option for their needs, ensuring that the packages reach their destination as quickly as possible.
Insurance and Liability: How are Lost or Damaged Fast-Shipped Packages Handled?
The topic of insurance and liability is a vital consideration in expedited shipping. When a package is lost or damaged, especially if it’s of high value or time-sensitive, it becomes a significant concern. Many carriers offer different levels of insurance coverage that protect against various risks. Some might cover just the value of the goods, while others might include shipping costs. Customers and businesses need to understand these insurance options, evaluating the terms and cost to decide if it’s worth the additional investment. Having the right insurance can give peace of mind and avoid potential disputes if something goes wrong during expedited shipping work.
Seasonal Fluctuations: How Does Expedited Shipping Change During Busy Times?
Expedited shipping faces unique challenges during peak seasons, such as holidays or major sales events. The increase in package volume puts more pressure on the delivery network, leading to potential delays and increased costs. Carriers may have to hire extra staff, extend working hours, or secure additional transportation to handle the surge. Customers might find that expedited shipping costs more or takes slightly longer, even with the premium service. Both businesses and customers must plan ahead, and clear communication becomes essential. By understanding how expedited and standard shipping shipping changes during these busy times, all parties can better navigate the complexities and ensure timely delivery.
Impact on Small Businesses: How Does Expedited Shipping Affect Small Businesses?
Small businesses face challenges with expedited shipping. They don’t have big networks like larger companies. But they can still get noticed by offering quick shipping. Working with bigger carriers or using local solutions can help. It’s all about finding the balance between costs and keeping customers happy.
Carrier-Specific Practices: What Methods do Different Shipping Companies Use for Expedited Shipping?
Different shipping companies have their own ways of handling fast shipping. Big names like FedEx and UPS offer special speedy services. Smaller ones might use a personal touch. Each one has unique services, prices, and guarantees. So, businesses and customers can find the right fit for their needs.
Insurance and Liability: How are Lost or Damaged Fast-Shipped Packages Handled?
If something goes wrong with a package in expedited shipping, insurance and liability become important. Carriers often offer coverage for the value of the goods and sometimes more. Customers and businesses should understand these terms. It helps to decide if the extra cost is worth it for the added peace of mind.
Seasonal Fluctuations: How Does Expedited Shipping Change During Busy Times?
During busy seasons like holidays, expedited shipping means more changes. More packages mean more pressure. Carriers might add staff or resources. Customers might see higher costs or slightly longer times. Both businesses and customers need to plan and communicate. It helps everyone deal with the busy shipping times more smoothly.
The Final Word
Expedited shipping plays a pivotal role in modern commerce. While it can cost more, the potential advantages often outweigh the expense. For instance, ensuring the timely delivery of a birthday gift, a vital business document, or an order from overseas, expedited shipping is an indispensable tool in the world of ecommerce.
One last thing to remember: the convenience of expedited overnight shipping now is at your fingertips – literally. Many online stores let you choose this overnight priority shipping only option right from their virtual shopping carts, and you can usually track your orders on your phone. This way, you can have peace of mind knowing exactly when your package will arrive.
We hope this blog post has given you a clearer look at the world of expedited shipping. As always, feel free to explore other posts on our website for more shipping and ecommerce insights.

Apr 21, 2023 | Blog
Ordering costs are expenses that businesses incur when making purchases. These setup costs can take many forms, from the price of raw materials and insurance to taxes and other fees. It’s important for businesses to understand these costs, so they can properly budget for them and make smart purchasing decisions.
Defining Ordering Costs
Ordering costs include all the expenses related to a purchase order and buying and receiving inventory items. These might be administrative costs such as paperwork, taxes, and insurance. It’s essential for businesses to be aware of these costs because they directly affect the total budget a company makes for purchasing inventory.
Types of Ordering Costs
There are several types of ordering costs that businesses need to account for. Some of these might be direct costs such as the cost of the goods themselves. Others might be indirect order costs, such as holding inventory, which includes costs like insurance and taxes. Changes in market conditions might also impact the total examples of ordering costs themselves, making it a complex problem for businesses to manage.
Calculating Ordering Costs: The Economic Order Quantity Formula
The Economic Order Quantity (EOQ) formula can be used to calculate the optimal number of inventory items a business should order at once. This quantity EOQ formula helps businesses balance the costs of ordering with the costs of your inventory position, thereby minimizing the total annual holding and ordering costs.
Holding Costs: Understanding the Other Half of Inventory Management
Holding costs are the other side of the inventory management coin. They represent all the costs associated with storing and maintaining inventory items. This could include costs incurred for storage space, insurance, taxes, and even potential loss due to theft or damage.
Calculating Holding Costs: The Average Inventory Formula
The Average Inventory Formula is used to calculate the total cost of holding inventory over a certain period. This formula allows businesses to estimate the total inventory cost and the annual inventory carrying cost. Understanding these costs helps businesses maintain a healthy balance in order cost of their inventory management.
How to Reduce Holding Costs: Strategies for Efficient Inventory Management
Holding costs, the expenses associated with inventory carrying costs, and with storing and maintaining inventory, can significantly impact a business’s bottom line. To enhance profitability and operational efficiency, organizations need to implement effective strategies to reduce holding costs while ensuring adequate inventory levels. Here are several actionable approaches to achieve efficient inventory reporting and minimize holding expenses:
1. Demand Forecasting and Inventory Planning
Accurate demand forecasting is essential to avoid overstocking or understocking inventory. Utilize historical data, market trends, and predictive analytics tools to forecast customer demand more precisely. With a clear understanding of demand patterns, businesses can optimize inventory levels and reduce the need for excess storage, ultimately lowering holding costs.
2. Implement Just-In-Time (JIT) Inventory
Just-In-Time inventory management aims to receive goods only as needed, eliminating the need for excess stockpiling. By maintaining lean inventory levels and having reliable supplier relationships, businesses can reduce holding costs associated with storing excessive quantities of goods.
3. Strategic ABC Analysis
Conduct an ABC analysis to categorize inventory items based on their value and usage. Classify items as A (high-value, low-quantity), B (moderate-value, moderate-quantity), and C (low-value, high-quantity). Focus on optimizing the replenishment and storage strategies for each category. This targeted approach ensures that valuable resources are allocated efficiently, reducing unnecessary holding costs.
4. Optimize Reorder Points
Determine the optimal reorder points for inventory items based on lead times, demand variability, and safety stock considerations. By setting reorder points accurately, businesses can avoid unnecessary stockpiling and prevent long periods of stockouts, leading to reduced holding costs and improved customer satisfaction.
5. Regular Inventory Audits
Conduct regular inventory audits to identify slow-moving or obsolete items. These items tie up valuable storage space and contribute to higher holding costs. By identifying and addressing such items promptly through promotions or liquidation, businesses can free up space, labor and resources for other expenses.
6. Supplier Collaboration and Consignment Agreements
Work closely with suppliers to establish consignment agreements where suppliers retain ownership of inventory until it’s used. This arrangement reduces the burden of holding costs on your company front end while ensuring a steady supply of materials when needed.
7. Optimize Warehouse Layout and Space Utilization
Efficiently organize your warehouse layout to maximize space utilization and labor costs. Implement vertical storage solutions, efficient racking systems, and clear aisle designs. By optimizing space usage, you can store more inventory without the need for excessive storage space, thereby reducing holding costs and shipping fees.
8. Use Technology for Real-Time Tracking
Leverage technology such as RFID tags and barcode systems for real-time inspection and tracking of inventory movements. This level of visibility enables better inventory management, reducing the chances of overstocking and improving inventory turnover rates.
9. Implement Vendor-Managed Inventory (VMI)
With VMI, suppliers monitor inventory levels at your location and restock as needed. This process eliminates the need for you to hold excess inventory, as your supplier manages replenishment. VMI fosters a collaborative relationship and ensures you have what you need when you need it.
10. Promotions and Bundling
Strategically plan promotions and bundle complementary items to clear out slow-moving inventory. By offering discounts or package deals, for example, you can encourage customers to buy items that might otherwise contribute to higher holding costs.
Efficiently managing holding costs requires a holistic approach that aligns inventory levels with actual demand. By implementing these strategies and continuously monitoring and adjusting your inventory management practices, you can strike the right balance between meeting customer needs and minimizing holding costs, contributing to your organization or company’s overall success.
Conclusion: Balancing Ordering and Holding Costs
Understanding ordering costs and holding costs is essential for businesses to manage their inventory effectively. By using tools like the EOQ and Average Inventory formulas, businesses can find the right balance between total ordering cost and purchasing and holding inventory. This ensures that they keep their total costs in check, enabling them to run their operations more efficiently and profitably.

Mar 28, 2023 | Blog
Effective warehouse operations rely on smart picking strategies. These strategies, involving everything from the placement of goods to the use of automation, are critical to improving customer service and the bottom line for warehouse managers.
Recognizing the Importance of Order Picking Methods
The process of order picking is integral to warehouse operations. The role of warehouse workers and order pickers, who hand-select goods from storage, is crucial to fulfilling customer orders efficiently. The right order picking methods can significantly improve operations, reducing downtime and human error, and operating costs while increasing profits.
Evaluating Different Picking Methods: One Size Doesn’t Fit All
Different facilities have different needs, and the size and nature of your warehouse operations matter. Companies must look at the specifics of their operation, such as the weight and size of goods, cross picking up, the layout of shelves and racks, and the demand for certain stock units. An organization’s choice in picking methods can impact everything from labor costs to customer service.
Understanding Piece Picking: The Basic Rule of Thumb
Piece picking is a common warehouse order picking strategy where order pickers select individual items for each customer order. This method is suitable for warehouses with a diverse stock range and smaller customer orders. However, the physical demands on staff and potential for the picking errors, may necessitate considering other strategies or technologies.
Exploring Zone Picking: Improving Flow and Control
“Zone picking method involves dividing the warehouse space into distinct zones. Each picker is responsible for one zone, picking all goods for customer orders from their area. This parallel picking method improves the flow and control of operations, reduces the distance people have to travel, and minimizes the risk of errors.
Delving into Batch Picking: Efficiency through Grouping
In batch picking, order pickers gather several customer orders at once. This approach reduces travel distance within the warehouse and can boost order picking efficiency. However, careful organization and control of discrete picking up are necessary to prevent mix-ups and ensure customer service quality.
Introducing Automation: The Future of Order Picking
Automation technologies, from scanners to automated storage and retrieval systems, offer vast improvements to warehouse picking, distribution centers and shipping operations strategies. While warehouse automations can be considered costly, they increase visibility of stock, minimize labor costs, and reduce the risk of human error. However, companies must weigh these benefits against the cost and potential disruption of implementing such systems.
Optimizing Stock Placement: Ergonomics and Profits
Ergonomics isn’t just about protecting staff. The placement of boxes, containers, and parts on racks and shelves can impact warehouse picking process, speed, risk of errors, and staff wellbeing. High-demand goods line items should be placed at eye-level for easy visibility and access, improving the flow of the picking process.
Utilizing Data and Technology: Webinars for Insight
Using data from warehouse operations can provide insight into things like stock cycle, sales trends, and the effectiveness of current picking methods and warehouse processes. Webinars and online learning can offer valuable advice on using this data for continuous improvement.
Batch Picking vs. Wave Picking: Finding the Right Balance
Batch picking and wave picking are two popular order picking methods that warehouses often employ to increase efficiency. Batch picking involves picking multiple orders simultaneously, while wave picking separates order picking process, and packing into distinct phases. Choosing between these methods depends on factors like order volume, product diversity, and staffing capabilities. Batch pick and pass picking suits warehouses with small orders, while wave picking is ideal for higher order volumes. The right balance between these methods can optimize productivity and minimize order fulfillment times.
Voice Picking Technology: A Revolution in Warehouse Efficiency
Voice picking technology has transformed warehouse operations by providing hands-free, voice-guided instructions to order pickers. This technology increases picking accuracy and speed, reduces training time for new employees, and enhances safety by allowing workers to keep their eyes and hands free. Voice picking systems also integrate with warehouse management systems (WMS), ensuring real-time updates on order lines and accurate inventory management. With its ability to streamline order fulfillment and picking processes, voice picking technology is becoming a must-have for modern warehouses.
Cross-Docking: Streamlining Warehousing and Distribution
Cross-docking is an innovative warehouse strategy for minimizing storage time by transferring goods directly from inbound to outbound trucks. This approach reduces handling costs, shortens delivery times, and lowers the need for long-term storage. Cross-docking is particularly effective for perishable items, time-sensitive products, and high-demand items. Implementing efficient cross-docking and best practices requires careful planning, coordination with suppliers and carriers, and a robust warehouse management system.
Picking Accuracy and Quality Control: Minimizing Errors in Operations
Picking accuracy is paramount to customer satisfaction and operational success. Implementing quality control measures in the whole order fulfillment process and picking and process improvements can significantly reduce errors and returns. Techniques like random order checks, barcode scanning, and verification systems help ensure that the right products are picked and packed accurately. Regular training programs, performance metrics, and continuous improvement initiatives contribute to maintaining high levels of picking accuracy.
Dynamic Slotting: Optimizing Warehouse Layout for Picking Efficiency
Dynamic slotting involves strategically placing products in the warehouse based on their popularity and demand patterns. High-demand items are positioned closer to the packing area of warehouse order to minimize travel time, while slower-moving items are stored further away. By optimizing the layout, different types of warehouses can improve picking efficiency, keep inventory accuracy reduce labor costs, and enhance order fulfillment speed. Dynamic slotting is an ongoing process that requires regular analysis of product data and adjustment of storage locations.
Remember that each a warehouse manager’s needs and operations are unique. Choosing the right warehouse order picking equipment, strategy or technology depends on factors like product characteristics, order volume, available resources, and technological capabilities. A comprehensive analysis of these factors, along with continuous evaluation and improvement, will lead to a warehouse that operates at peak efficiency, enhances customer satisfaction, and drives overall profitability.
Conclusion: Finding the Right Strategy for Your Warehouse
Determining the right picking strategy for your warehouse operations isn’t a one-size-fits-all affair. It’s about understanding your entire warehouse side’s specific needs, evaluating the nature of your stock and demands, managing inventory, and finding the right balance between labor, automation, and customer service. It’s a continuous cycle of improvement – because when it comes to warehouse operations, every little bit of efficiency translates into money saved and profits earned.

Aug 11, 2023 | 3PL Warehouse Management, Blog, Warehouse Operations
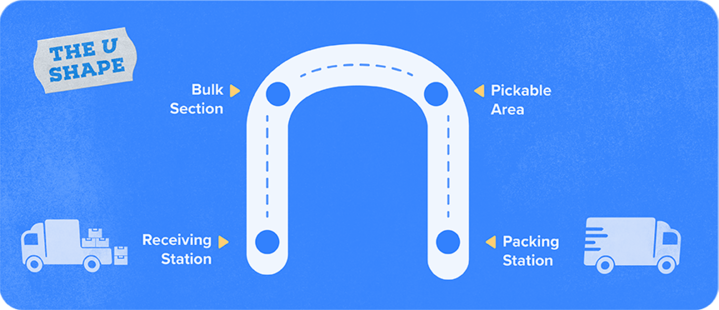
The Importance of Efficient Warehouse Flow
Efficient warehouse flow is crucial for any warehouse to run smoothly. A well-managed warehouse ensures products are received, stored, and distributed seamlessly. In this blog post, we’ll go over the basics of warehouse flow, from receiving to outbound packaging, and why optimizing each step is essential. Whether you’re a warehouse expert or a curious reader, this blog post will provide valuable insights into warehouse operations.
U-Shape Flow – How ShipHero Does It
Most warehouses have a square or rectangular shape with receiving and outbound doors on one side, creating a U-shaped flow. There is usually ample space between the dock and receiving area, where products are sorted. Having more room than you need to avoid congestion or delays will come in handy.
Receiving
Once products are ready to be received, they are taken to the receiving station. This can include fixed or mobile stations, depending on the volume of products being handled. Receiving is a critical aspect of warehousing, and nothing gets past the receiving station if it has not been checked or labeled. Items that pass inspection are ready to be put away, while non-compliant items are labeled accordingly.
Bulk Section
The next step in warehouse flow is the bulk section. This is where the overstock pallets are stored until they are needed. From there, products move to the pickable area, where pickers select items for packing. As inventory is moved out of the warehouse, items are moved from the bulk section to the pickable area, where pickers can easily access them.
Picking and Packing
Pickers typically move around the warehouse with carts, selecting individual units from bins. Once all necessary items have been selected, they move to the packing station. This is where orders are finalized, labeled, and packed into boxes.
Outbound Packages
After preparing your packages, they will be taken to the outbound dock to be shipped. We typically use collapsible bulk containers for storing outbound items. Choosing a reliable shipping method is important to ensure safe and secure delivery. We recommend reputable options like USPS or FedEx.
Why Warehouse Layout is Important
An efficient warehouse layout is vital for a successful logistics operation. The layout plays a significant role in productivity, cost-effectiveness, and customer satisfaction, making it an essential factor to consider when setting up a warehouse. Let’s look at the various aspects that an optimized warehouse layout can improve.
- Optimized Material Flow: Efficient warehouse layout improves material flow, reducing handling time and movements. This leads to quicker order fulfillment, shorter lead times, and improved customer service.
- Enhanced Productivity: A well-planned warehouse layout can boost productivity by reducing the time and energy needed to find, choose, and pack items. This means less travel distance for workers and higher throughput and order processing.
- Space Utilization: Layout planning to maximize available space helps reduce storage expenses, keep the area clean, and increase inventory storage capacity.
- Safety and Ergonomics: Prioritizing safety when designing warehouse layouts can prevent accidents, protect employees, and reduce damage to goods. Ergonomic warehouse designs can lessen worker fatigue and injuries.
- Inventory Accuracy: A good warehouse layout assigns specific locations for each SKU to improve inventory accuracy. This reduces the chances of misplacement or incorrect picking, resulting in more precise inventory counts and less risk of stockouts or overstocking.
- Efficient Order Fulfillment: A thoughtfully designed warehouse layout ensures that popular or fast-moving items are strategically placed closer to the shipping area, expediting the picking and packing process for high-demand products.
- Adaptability to Changing Needs: Flexible and easily adjustable warehouse layouts are crucial for businesses adapting to new market conditions. Seek arrangements to accommodate changing storage needs, new products, and different order profiles without disrupting ongoing operations.
- Integration with Technology: Efficient warehouse layouts that accommodate modern technologies like ShipHero WMS, barcode scanners, and automation are crucial for optimizing productivity, accuracy, and data-driven decision-making.
- Cost Optimization: An optimized warehouse layout directly impacts operational costs. You can achieve significant cost savings and allocate resources more strategically by reducing labor, storage, and material handling expenses.
- Competitive Advantage: A well-organized warehouse can give businesses a competitive edge by enabling faster order processing and lead times. This leads to better customer service, increasing customer satisfaction and loyalty.
So Many Benefits
Understanding warehouse flow is critical to running a successful operation. Utilizing the U-shape flow model and optimized warehouse layout can provide numerous benefits, such as faster material transit time, enhanced productivity, cost optimization, and more. It’s also important to recognize the impact of technology on efficient fulfillment delivery and provide an environment that is safe for employees. Having the proper infrastructure makes a big difference in improving customer experiences and ultimately attaining business success.
If you want to visualize efficient warehouse flow, click here to watch our detailed walkthrough videos for further insights into best practices for warehouse operations.

Mar 29, 2023 | Blog
Managing warehouse and store inventory is a balancing act that impacts everything from labor costs to customer service. Companies need to navigate a variety of challenges to maintain optimal inventory levels and meet demand.
What is inventory management in a warehouse?
How do you manage warehouse inventory for your stocks and e-stores? Warehouse inventory management is the process by which inventory is collected and stored in a warehouse, managed by personnel in storage warehouses and optimized storage capacity and prices; the entire process directly affecting fulfillment, shipping, and customer experiences.
How do warehouses keep track of inventory?
A Bar Code System allows the product label for information like description, location, prices. The label is automatically updated by scanning the barcode scanner device.
Understanding the Importance of Warehouse Inventory Management
Effective inventory management is crucial for companies to ensure they meet customer demand, reduce costs, and increase profits. It involves a multitude of tasks, such as forecasting demand, tracking stock movements, using warehouse inventory systems and auditing physical inventory. The right software solutions can make these activities more efficient and reduce the risk of errors and bottlenecks.
Techniques for Better Inventory Management
There are many techniques companies can use to manage their warehouse space and inventory more effectively. For example, ABC analysis is a method of categorizing and storing inventory based on its importance. Another technique is cycle counting, which involves regularly counting a subset of inventory to identify discrepancies. Both techniques can help prevent mistakes and improve accuracy.
Utilizing Technology in Inventory Management
The use of technology is becoming more common in real time inventory tracking and warehouse management software. Real-time data collection and optimization software can provide valuable insights into stock quantities, storage space capacity, and shifts in demand. These technologies can improve accuracy, minimize labor costs, and improve customer service by ensuring the right products are available when needed.
Efficient Storage and Retrieval Systems
How inventory is stored in a warehouse can significantly impact the picking and packing process and overall efficiency of warehouse workers. Organizing storage space with clearly marked bins, labels, and racks can help pickers locate items quickly and reduce mistakes. In addition, technologies like automated storage and retrieval systems can enhance these benefits.
Demand Forecasting: A Proactive Approach
Demand forecasting uses data to predict future sales trends. This can help companies manage their inventory more effectively, reducing the risk of overstocking or understocking items. For instance, by using good inventory management and accurately forecasting demand, companies can better plan their orders from suppliers, improving customer service and the bottom line.
Training and Incentive Programs: Empowering Your Staff
Training programs for warehouse staff can equip them with the skills they need to handle equipment safely and follow proper procedures. Furthermore, incentive pay programs can motivate staff to achieve goals and make continuous improvements. Both measures can reduce downtime, prevent accidents, and increase warehouse productivity further.
Inventory Auditing: Ensuring Accuracy
Regular inventory counts and auditing is an essential part of any warehouse inventory management system. Auditing involves physically counting inventory and comparing it to recorded quantities. This helps identify any discrepancies and opportunities for improvement.
Safety Measures in Inventory Management
Ensuring the safety of both the warehouse manager, staff and inventory is paramount to maintain smooth operations and prevent accidents. Implementing effective safety measures can protect warehouse employees and preserve inventory integrity:
- Proper Training: Provide comprehensive training to warehouse staff on the safe operation of equipment, handling hazardous materials, and following safety protocols.
- Safety Equipment: Supply personal protective equipment (PPE) such as gloves, helmets, and safety goggles to ensure workers are adequately protected.
- Clear Signage: Use clear and visible signage to indicate hazardous areas, emergency exits, and the location of safety equipment.
- Regular Inspections: Conduct regular safety inspections to identify potential hazards, faulty equipment, or unsafe practices.
- Emergency Preparedness: Establish emergency response plans, including evacuation procedures and first aid protocols, to ensure quick and effective responses in case of accidents.
Reverse Logistics and Returns Management
Efficiently managing returns tracking inventory and reverse logistics is crucial to maintain customer satisfaction and recover value from returned items. Here’s how to optimize returns using warehouse management systems:
- Streamlined Process: Design a clear and efficient returns process that includes easy-to-follow steps for customers and staff.
- Inspection and Classification: Implement a thorough inspection process to assess the condition of returned items. Classify them as resalable, refurbishable, or unusable.
- Automated System: Utilize inventory management software with integrated returns management features to track returned items, update inventory levels, and facilitate refunds.
- Restocking and Reselling: Quickly restock resalable items to minimize holding costs and potentially resell refurbished items at a reduced price.
- Customer Communication: Maintain transparent and timely communication with customers about their returns, refund status, and any applicable fees.
Inventory Turnover Ratio and its Implications
The inventory turnover ratio is a key performance metric for every type of warehouse that reflects how efficiently inventory is being managed. Here’s how to calculate the inventory software, and interpret it:
- Calculation: Calculate the inventory turnover ratio by dividing the cost of goods sold (COGS) by the average inventory value [(Beginning Inventory + Ending Inventory) / 2].
- Interpretation: A high turnover ratio indicates efficient inventory management, while a low ratio may signify overstocking or slow sales.
- Impact: A high ratio implies that inventory is being sold quickly, reducing holding costs and improving cash flow. A low ratio may lead to higher holding costs and potential obsolescence.
- Optimization: Balance inventory levels to align with demand, prevent stockouts, and avoid excessive holding costs. Adjust purchasing strategies based on the turnover ratio to optimize profitability.
Multi-Location Inventory Management
Managing inventory across multiple locations requires strategic coordination to ensure more efficient warehouse operations and minimize excess stock. Here’s how to optimize multi-location inventory with warehouse management solutions:
- Centralized Visibility: Implement inventory management software that offers real-time visibility into stock levels across all locations.
- Demand Forecasting: Analyze demand patterns at each location to allocate inventory according to demand fluctuations.
- Inventory Transfer: Set up a streamlined process for transferring excess stock from one location to another to prevent stockouts or overstocking.
- Optimal Distribution: Determine the optimal distribution strategy based on factors like transportation costs, demand proximity, and order fulfillment speed.
- Performance Metrics: Monitor performance metrics for each location, such as turnover ratios and holding costs, to identify areas for improvement and standardize best practices.
By addressing safety, returns, warehouse management system, turnover ratio, and multi-location challenges, companies can enhance their inventory management practices, reduce costs, and ensure smooth and efficient operations across the warehouse network.
Demand Forecasting for Effective Inventory Management
Accurate demand forecasting is the cornerstone of successful inventory and supply chain management. Follow these steps to make inventory control and forecast demand effectively:
- Historical Data Analysis: Study past sales to identify patterns and trends.
- Market Research: Gather insights on market trends, customer preferences, and external factors.
- Statistical Models: Use forecasting methods like moving averages and exponential smoothing.
- Collaboration: Involve sales, marketing, and production teams for well-rounded insights.
- Software Tools: Leverage inventory management software with forecasting capabilities.
Using Data Analytics in Inventory Management
Data analytics can revolutionize your inventory management system. Here’s how to harness its power:
- Data Collection: Gather data on sales, inventory levels, lead times, and customer behavior.
- Identify Trends: Use analytics tools to uncover patterns and trends in the data.
- Demand Patterns: Understand peak seasons, product lifecycles, and demand fluctuations.
- Optimize Reordering: Set automated reorder points and quantities based on analytics.
- Real-time Updates: Utilize real-time data for agile decision-making.
Just-in-Time (JIT) Inventory Management
JIT is a strategy to manage inventory and minimize holding costs while meeting demand. Implement JIT with these steps:
- Demand Forecasting: Accurate demand prediction is crucial for JIT success.
- Supplier Relationships: Build strong relationships to ensure timely deliveries.
- Reduced Lead Time: Minimize lead time between order placement and delivery.
- Lean Inventory: Maintain only the necessary inventory levels to meet immediate demand.
- Continuous Improvement: Monitor and adjust processes for optimal JIT implementation.
The Role of Technology in Inventory Management
Technology empowers efficient and inventory management systems. Leverage technology to automate inventory tracking with these strategies:
- Inventory Management Software: Choose software for real-time tracking and accurate stock control.
- Barcode Scanning: Use barcodes for error-free inventory tracking and quick data entry.
- RFID Technology: Implement RFID tags for automated and detailed inventory tracking.
- Automation Solutions: Integrate automated systems for order fulfillment and tracking.
- Cloud-based Systems: Utilize cloud technology for remote access and scalability.
Sustainability in Inventory Management
Sustainable inventory management best practices contribute to efficient warehouse inventory management processes and environmental responsibility. Adopt sustainable approaches:
- Eco-friendly Packaging: Opt for biodegradable or recyclable packaging materials.
- Energy-efficient Warehousing: Implement energy-saving solutions like solar power and LED lighting.
- Reducing Waste: Minimize excess inventory to reduce waste and storage costs.
- Reverse Logistics: Establish processes for recycling and reusing returned products.
- Supplier Selection: Choose suppliers with sustainable practices for a greener supply chain.
By applying demand forecasting, data analytics, JIT strategies, technology integration, and sustainability principles, businesses can optimize warehouse management focuses and inventory management systems, streamline operations, and achieve greater profitability.
Conclusion: Achieving Balance in Warehouse Inventory Management
Effective, warehouse management and other inventory management solutions is a complex process that requires a blend of techniques, technologies, and training. By striking the right balance, companies can improve their warehouse operations, enhance customer service, and ultimately increase their bottom line. It’s a challenging endeavor, but with the right investment in solutions and continuous improvement, it’s an advantage that can lead to significant benefits.

Mar 28, 2023 | Blog
Warehouses and fulfillment centers both play essential roles in supply chain operations, but people often get confused about their specific functions. While they share some commonalities such as the need for space utilization and product flow, understanding their differences is vital for efficient planning and quality control in logistics processes.
What is a Warehouse?
For most businesses, a warehouse serves as a large storage facility where the layout’s design, including the arrangement of aisles, racks, and skus, is pivotal for space optimization and quick product retrieval. This design not only aids pickers in navigating the various warehouse space, reducing confusion and time spent searching for items but also has a direct impact on productivity. Employees in a warehouse face challenges, and their training is paramount. They handle various tasks, from manual labeling of products to making job adjustments due to inventory changes or the introduction of new categories. With different sizes and amounts of items to manage, a proper plan to tackle potential problems and issues is crucial for smooth operations.
What is a Fulfillment Center?
A fulfillment center, on the other hand, focuses on order processing and packaging for sales. Its primary reason for existence is to fulfill customer orders efficiently. Here, warehouse optimization methods, like zoning lease warehouse space and categorizing items into different zones, streamline the picking fulfillment process. Robots, automated systems, and IoT devices play a pivotal role in amplifying productivity, diminishing human error, and ensuring the quality of service, thus reducing expenses related to mistakes.
Main Differences Between a Warehouse and a Fulfillment Center
The fundamental difference between a warehouse and a fulfillment center lies in their functions: storage vs. order fulfillment. This distinction reflects in their layouts: while warehouses emphasize maximizing floor space with options like high-capacity storage systems or pallet racks, fulfillment centers stress efficient routes and zones for fast retrieval and packaging shipping orders. Additionally, technology, which is often an example of warehouse automation, is more prevalent in a fulfillment center vs. centers. Given the complexity of an average order and the demand for rapid order completion, tools ranging from automated retrieval systems to IoT-enabled checklists become pivotal in a fulfillment center’s efforts to avoid delays and stockouts.
Why Does it Matter?
Understanding these differences isn’t just something to check off a list. It has a direct impact on a company’s bottom line, customer satisfaction, and business to business’ reputation. A business experiencing high sales volumes might find the quick and efficient methods of a fulfillment center more advantageous, leading to faster deliveries and satisfied customers. However, those handling a larger inventory might prefer the vast more storage space and organization offered by a warehouse.
Costs Matter
When choosing between warehouses and fulfillment centers, understanding costs is vital. Initially, warehouses might seem more expensive than distribution or most fulfillment centers, due to infrastructure. However, in the long run, the advanced tech and speedy services of fulfillment centers might add up. Always consider factors like rental rates, tech upgrades, staffing, and operational expenses to make a wise decision.
Growing Your Business
As businesses evolve, so do their needs for physical space. Warehouses are ideal for storing inventory and holding vast amounts of stock. On the other hand, fulfillment centers are geared towards handling spikes in orders, especially during peak times. So, when pondering where to invest, think about which facility will adapt to your growth trajectory.
Tech Talk
Technology usage differs between the two. Warehouses often incorporate systems to oversee expansive inventories. In many ecommerce businesses by contrast, fulfillment centers prioritize technology that ensures swift customer order processing and dispatch. Consider which type of tech support will be more scalable and affordable for your operations as they expand.
Keeping Track of Stock
Inventory management remains central to ecommerce companies’ business. Warehouses focus on maintaining extensive inventories and ensuring they’re easily accessible. Fulfillment centers emphasize fast movement to facilitate quick shipping. The real question is, which system ensures products are always available and ready for customers?
Handling Returns
In the digital age e commerce, returns are part and parcel of the business to consumer online shopping. While fulfillment centers are designed to process returns efficiently, warehouses might have a slightly slower system. Analyze which setup simplifies the return process and enhances customer satisfaction.
Stay Safe
Protection isn’t just about physical goods but also data security and fulfillment services. Warehouses might employ advanced CCTV systems, while fulfillment centers could integrate robust cybersecurity measures, especially when handling customer data. It’s crucial to weigh which facility online store offers a comprehensive safety net.
Think Green
Environmental considerations are no longer an afterthought. Fulfillment centers might emphasize sustainable packaging, whereas warehouses and shipping carriers could adopt energy-efficient systems. Determine which aligns better with your own warehouse or company’s eco-friendly objectives.
Location, Location!
Location plays a pivotal role in logistics and order fulfillment services for companies. Warehouses might be more cost-effective in outskirts, but fulfillment centers benefit from being near urban areas for prompt deliveries. Reflect on which geographical positioning aligns with your distribution strategy.
Jobs and Duties
The roles of employees differ by fulfillment center operations warehouse. In warehouses, they’re predominantly engaged in stock management. However, in fulfillment centers, there’s a mix of order processing, tech management, and customer service. Assess which facility offers roles that align more with your operational needs.
Real Stories
Consider a budding online business. Initially, a fulfillment center might suffice due to limited orders. However, as scale increases, a warehouse could offer more economical storage and fulfillment solutions store excess inventory. Such practical scenarios can guide your decision-making. Which facility mirrors your business’s journey?
Make it Personal
Personalization is the key to modern ecommerce retailers’ consumer satisfaction. Fulfillment centers, with their quick processing, might be better equipped to handle custom orders. However, warehouses can stock a broader range store inventory of unique products. Decide which setup will better cater to your clientele’s specific requirements.
What’s Next?
The future beckons with more technological integrations. Warehouses might soon see more robotic assistants, while fulfillment centers could leverage AI for predictive analytics. Stay future-ready by choosing the facility, warehousing solution or fulfillment company that’s more adaptable to emerging technologies.
Rules to Follow
Compliance is vital. Both facilities have distinct guidelines to follow:
- Warehouses need to adhere to specific storage regulations, especially if they house perishable or hazardous materials.
- Fulfillment centers must stay updated on shipping protocols and regulations.
It’s paramount to ensure that your chosen facility adheres to all the required norms for your product type.
Planning for Problems
Contingencies are essential. Both facilities must have plans to address challenges such as:
- Natural disasters like floods or earthquakes.
- Sudden demand surges due to seasonal trends or promotions.
- Technological failures, be it software glitches or equipment malfunctions.
- Security breaches, both physical (theft) and digital (hacks).
- Supply chain disruptions, which can arise from global events or local transportation issues.
It’s essential to evaluate which infrastructure is better equipped to handle unforeseen adversities.
Cost Implications
Delving deeper into the cost structures of both setups:
Warehouses:
- Rental Costs: Often located in outskirts, which might lead to lower rentals but higher transportation expenses.
- Maintenance: Regular upkeep of storage systems, machinery, and the facility itself.
- Inventory Costs: Holding vast inventories can lead to depreciation or wastage, especially for perishable goods.
- Manpower: Costs associated with training and salaries of warehouse personnel.
- Technology Upgrades: Incorporating latest tech tools or machinery can lead to significant expenses.
Fulfillment Centers:
- Rental Costs: Being near urban centers, rentals can be higher.
- Operational Expenses: Costs linked to quick order processing, shipping, and returns.
- Tech Investments: Warehouse automation and cutting-edge tech might require substantial initial investment but can reduce
Conclusion
In summing up, it’s essential to consider the specific needs of your business, the kinds of products you manage, and your sales volume when choosing between a warehouse and a fulfillment or distribution center. A well-planned strategy and professional fulfillment center, backed by the right skills and tools, can help minimize waste, boost efficiency, and enhance your business’s overall performance.

Dec 9, 2022 | Blog
Maintaining an organized warehouse and storage area is a fundamental element for any company, especially when handling substantial quantities of material. This article will delve into the sequence of methods that will optimize your warehouse bin storage system, with a focus on layout, shelving, aisles, and more.
What is a Warehouse Bin Storage System?
A warehouse bin storage system is a method of arranging inventory in specific spaces within a warehouse, aiding in efficient inventory management. Correct identification and labeling bin warehouse systems play a vital role in preventing errors and make it easier for your team to search for items in your own warehouse management system. Discover more about warehouse bin storage systems here.
Understanding the Layout of Your Warehouse
The layout of storage rooms in your warehouse, including the floor space planning, directly impacts the efficiency of your operations. Well-organized aisles, zones, and areas, marked with clear arrows, ensure a smooth pick path for workers. The use of devices like a phone for material tracking can also enhance the effectiveness of your layout, improving service for customers. Since there are 6 different types of warehouses, it’s important to factor in that bin layouts vastly differ from one another.
Naming Convention and Labeling System
Adopting a consistent naming convention and labeling system is crucial. A common method includes a combination of letters and characters to denote different elements, such as racks, shelves, and bins. Additionally, a location numbering scheme can be implemented to ease and further streamline the inventory process. A properly maintained warehouse labeling system can greatly reduce errors and confusion among workers.
Choosing the Right Inventory Management System
The right inventory management software and system can revolutionize your store and warehouse operations. Tools like Shiphero can help manage your stores efficiently by providing real-time inventory updates, enabling you to position your inventory in the most effective way.
Organizing Your Warehouse with Zones and Aisles
Zones and aisles in your warehouse design should be designed with the flow of people and materials in mind. Effective sequencing of these areas in your warehouse layout can help minimize unnecessary movements and maximize efficiency.
Warehouse Labeling and Identification
Warehouse labeling and identification are not just about sticking names to bins. They are about creating a system where every position of available space, every unit, every rack, and every shelf has a unique identifier. This system aids workers in quickly finding and storing items, reducing errors and boosting customer satisfaction.
Implementing Automation in Bin Storage System
Automated Storage and Retrieval Systems (AS/RS) are computer-controlled systems that can significantly improve the efficiency of bin storage systems. They are designed to increase the speed of retrieval, decrease manual labor, and minimize human error at rates. Besides, automated systems can help optimize warehouse space due to their ability to support higher and denser storage.
Inventory Turnover Rate
Inventory turnover rate is a metric that shows the number of times a business has sold and replaced inventory during a specific period. A high turnover rate indicates effective selling and replenishing. This means less capital tied up and reduced storage costs. A well-organized bin storage system can significantly increase this rate by ensuring faster retrieval times and reducing instances of misplaced items.
Seasonal Variation in Inventory
Seasonal demands can cause fluctuations in inventory volumes in warehouses. An optimized bin storage system should have a flexible layout that can be easily reconfigured. During peak seasons, your ideal warehouse layout should be able to accommodate larger inventories without compromising on organization or retrieval times.
Temperature-Controlled Bin Storage
Certain items, like perishable foods or sensitive electronic components, need specific temperature conditions to maintain their quality. Temperature-controlled areas can be included in optimized bin storage systems. Advanced systems can even offer varying temperature zones within the same warehouse floor.
Sustainability in Bin Storage System
An environmentally friendly warehouse is a critical requirement in today’s world. Using recyclable bins, optimizing energy usage, and incorporating natural light where possible are ways to make your bin storage system more sustainable. Additionally, an efficient warehouse layout optimization minimizes unnecessary movements, thereby saving energy.
Regulations and Compliance
Compliance with safety and inventory management regulations is crucial for maintaining your warehouse’s credibility. This includes guidelines for stacking height, aisle width, and hazardous material handling equipment storage, among others. An optimized bin storage system ensures these regulations are met, thereby reducing the risk of legal issues.
Bin Storage System Software
A wide range of warehouse management software is available today that can help manage your bin storage system more efficiently. The features include real-time inventory tracking, automated data collection, and advanced analytics that provide insights into warehouse operations.
Employee Training for Bin Storage System
Despite having an optimized bin storage system, it won’t be effective unless your staff is well-trained in how to use it properly. Regular training ensures that all employees are familiar with the system, can locate items quickly, and know how to handle any issues that may arise. This not only enhances efficiency but also improves workplace safety.
Warehouse Safety and Efficiency: The Essentials
Ensure Safety Protocols in Warehouse Storage Rooms
The best warehouses put safety first. Clear aisles and effective labels help reduce accidents. Warehouse signs can highlight hazards, while safety training teaches staff to handle materials correctly. So, your warehouse becomes a safe place to work, not just an efficient one.
Tech Boosts Warehouse Efficiency
Efficient warehouses use the right technology. Adding RFID tags, barcode scanners, and warehouse management software (WMS) to your setup boosts real-time tracking and cuts down errors. To make these tech tools work, staff need training—a step you can’t skip.
Staff Training Matters
You need well-trained staff for a top-notch warehouse. Regular move reviews and training updates on the storage system, new tech, and safety processes are vital. So, if your staff knows their stuff, your entire warehouse will work better.
Layouts that Cut Costs
A smart, efficient warehouse layout design does more than just organize and keep things smooth—it saves money. Fewer unnecessary movements mean less time wasted, and fewer errors mean less money spent on fixing them. It’s the secret to running a warehouse that’s cost-effective, not just operational.
Regular Audits Keep Things Running Smoothly
You can’t forget about regular audits. They check that everything’s working as it should and spot areas for improvement. With regular audits, your whole warehouse operation will always be at its best, delivering top efficiency and productivity all the time.
Efficient Bin Storage System Setup Tips
Grouping Items: ABC Way
Group your items based on their traits, such as size, weight, and how often they’re used in existing warehouses. The ABC analysis is your best friend here. ‘A’ items are popular, ‘B’ items are less so, and ‘C’ items are the wallflowers. The outcome? Picking processes are streamlined, and workers cut down on their cardio in the warehouse.
Smart Placement
Think of usage patterns. Your fast-moving items should be neighbors with the dispatch areas, slashing retrieval times. Meanwhile, slow movers can chill in the less accessible spots. This “product slotting” tactic ensures every inch of your warehouse floor plan works hard and your productivity is on point.
Labels: A Necessity
Labels on your bin locations are the tour guides of your warehouse. Workers find items quicker when labels on storage bins are readable and packed with info such as product name, SKU, and bin location. So, time spent on the “Where’s Waldo” of items? Significantly reduced.
Vertical Space: Use it
Don’t ignore your vertical wall space – it’s a hidden gem of storage space and capacity. Stack those bins and use taller storage units. But remember, safety first – no heavy or oft-used items in the stratosphere.
Layout Design: The Fishbone Advantage
Design your bin rows’ layout to put Usain Bolt to shame – minimize travel time. A method to swear by is the “fishbone” aisle design, a straight-line path perfect for item retrieval.
Choose the Right Type of Storage Bins
Bigger isn’t always better. Choose the right bin for your items. Some items need bins with dividers; others demand larger, robust bins. The right bin not only keeps your items snug and safe but makes accessing them a breeze.
With these elements, you’re on track to add up to a bin storage system that takes your warehouse layout from good to great.
Final Thoughts on Warehouse Bin Storage System Best Practices
Every company has a reason to keep their warehouse organized. Whether it’s for inventory system efficiency, error reduction, or simply to maintain a well-organized warehouse, implementing these best practices can enhance your operations. A well-structured warehouse layout design, consistent naming conventions, and easy and effective labeling systems all contribute to a more efficient and productive warehouse.
—
For More Information About ShipHero
Whether you want to let go of running your warehouse or run your warehouse better, you can do both – and so much more – with ShipHero.
Click HERE to Schedule a Meeting with Our Sales Team.
Follow us today on Twitter and LinkedIn.
Dec 30, 2022 | Blog
Automating your warehouse involves a variety of factors, from the size of the warehouse to floor space to safety measures. It’s about integrating automation technologies into warehouse systems, such as warehouse robots and automated guided systems, to optimize order fulfillment and enhance customer satisfaction. These automated warehouse systems are designed to improve order accuracy and streamline the movement of goods.
What is Warehouse Automation?
The goal of warehouse automation is to automate as many repetitive tasks and processes as possible within a warehouse with the goal of increasing speed and efficiency and reducing human assistance. This automation can come in both the form of software and physical robotics which move throughout the warehouse. Talking to an expert can be highly helpful when trying to decide how to automate your warehouse as they will assess your current warehouse workers, processes, and your goals, to help you find the technology to make those goals a reality.
How Automation Pays Off
Yes, warehouse automation can cost a lot upfront. But the return on investment (ROI) can be worth it. Think about:
- Labor Savings – Less labor needed can mean big cost savings over time.
- Higher Productivity – Tech can work all the time, which means more output and more revenue.
- Fewer Errors – Tech makes fewer mistakes than people, which cuts down on costs.
- Better Space Use – Some tech, like AS/RS, can use vertical space, saving costs in warehouse space.
Yes, the upfront cost is high, but long-term savings and efficiency costs with industrial automation can lead to a positive ROI over time.
What Influences the Costs of Warehouse Automation?
The cost of warehouse automation depends on numerous factors. Size matters; large-scale operations may need thousands of pallets moved daily, which requires a significant investment in automation technologies. On the other hand, small-scale operations might only need a few automated forklifts or drones to improve efficiency and reduce warehouse labor costs further. The people involved in these operations also play a role in determining the cost.
Other cost-influencing factors include the complexity of your supply chains, the level of human intervention currently required per automated solution, and the dimensions of your fully automated solution, warehouse system and infrastructure.
For instance, retailers like Walmart may have multiple large-scale distribution centers requiring advanced automation. These are the things to consider when planning for warehouse automation.
The Costs of Different Automation Technologies
There’s a wide range of various warehouse management and automation systems available, each with its unique cost basis. Conveyor belts, automated storage and retrieval systems and cloud computing can provide enhanced visibility into the picking process and minimize error rates, but they also involve substantial initial expenses and ongoing maintenance costs. These technologies provide valuable insights into warehouse management system operations.
Here are some general stats for your warehouse costs with industrial automation costs available.
- If you want a system which focuses on picking improvement, you will likely find the cost to be between $500,000 to $1 million
- In searching for a mechanized operation system you’ll find the cost range between $1 million to $5 million, and some enterprise systems can even get up to $15 million
- If you want to look at a “dark warehouse” with no operators, you could expect around $25 million
- But these are just estimates. Each warehouse is unique with different needs which means the price to automate your warehouse operations will be specific to you.
More advanced options, such as collaborative mobile robots such as warehouse robots and cobots (collaborative robots), might have higher upfront operating costs. However, their benefits like improved safety, productivity, and error-proofing of automated systems may make them a worthwhile investment in certain cases.
Leveraging Government Aids for Automation
To encourage businesses to upgrade their tech, governments often provide grants and tax incentives. If your automation includes AI, robotics, or similar technologies, you might qualify for these benefits. Tax credits or accelerated depreciation could also be part of your financial strategy. This varies by region and business, so seek advice from a local business counselor or tax professional.
Calculating Total Ownership Cost in Automation
The total cost of ownership (TCO) is essential when considering warehouse automation. This figure includes your initial investment, plus ongoing costs like maintenance, upgrades, and staff training. Regular upkeep keeps your automation tools running well.
Over time, you’ll need to upgrade your system to stay on the cutting edge. Plus, your team will need training to use these new tools. Calculating TCO gives you a realistic picture of your investment and helps you make wise choices about which automation technologies offer the best return.
Real-world Examples of Warehouse Automation Success
- Amazon – Amazon’s automated warehouses host over 200,000 robots globally as of 2020. Robots move shelves to workers, saving time and effort. The result? They can handle up to 700 orders every hour.
- Ocado – Ocado, a UK online grocery, uses “swarm” robots to pick groceries. With precision and speed, they handle over 3.5 million items or 65,000 orders weekly.
- Adidas – Adidas’ SPEEDFACTORY is mostly using automated systems. The result is quick response to demand, less overproduction, and fewer transport distances.
- Zalando – Zalando used robots to deal with growing order numbers. Robots improved efficiency and cut down processing time.
Balancing Costs and Benefits of Warehouse Automation Solutions
Warehouse automation is not merely a cost but an investment. With the growth of online sales and the e-commerce market, companies need to deliver results quickly and accurately to their customers. Enhanced productivity and reliability through automation technologies can significantly impact your bottom line. The reasons for implementing warehouse services and automation solutions often outweigh the costs.
Additionally, industrial automation systems can also provide scalability and flexibility to existing labor,, which is vital in adapting to changes in customer demand. For example, a sudden surge in orders can be handled more efficiently with an automated system than with manual labor.
When Does Automation Make Sense?
It makes sense when the warehouse automation cost outweighs the existing warehouse operating budget and expenses. Managers need to keep in mind the risk versus reward. The key is to find a balance between significant cost savings investing in technology and automation cost while ensuring it delivers the right results in terms of productivity, safety, and customer satisfaction.
For instance, if a large portion of your expenses goes towards warehouse automation, reducing costs go towards moving and tracking goods manually, your warehouse automation RoI will be high. Moreover, if error rates are high due to human error and intervention in manual tasks, technologies such as artificial intelligence could offer valuable error-proofing measures.
Factors to Consider when Implementing warehouse automation solutions
When you’re choosing automation tech, think about: Budget – What are the costs of buying, installing, and upkeep of automation equipment? Remember to weigh initial costs against long-term savings. Operations Size – How big is your warehouse and how many goods do you handle? This will help you decide what tech will help most.
Fragile items may need different automated storage and retrieval when put to light systems rather than heavy ones. Existing Systems – Current systems in your warehouse might affect which tech fits best. Future Plans – If you plan to grow your warehouse or operations, your tech needs to grow too.
How Warehouse Automation Impacts Other Operations
Automation doesn’t just affect your warehouse. In fact, automation can affect other major parts of your business in a good way. As an example, if you automate as many processes as possible within your warehouse using both robotics and inventory management software, you’ll see a ripple effect towards other aspects of your business.
Think about how this automated solution would roll over to your other operations. Especially cost to automate, with higher accuracy and more data to feed major decisions within your company. The automation you implement today will continually service your business down the road.
Future Trends in Warehouse Automation
The whole warehouse floor space and automation landscape is continuously evolving with technological advancements. Let’s delve into a few future trends that experts predict will shape the whole warehouse space industry:
Enhanced Machine Learning and AI Capabilities
Artificial Intelligence solutions are playing an ever-increasing role in automation. Advanced algorithms can analyze large volumes of data to forecast demand, optimize inventory, and streamline the supply chain to develop more complicated automation solutions. We’ll likely see even more integration of these technologies with cloud computing into warehouse operations.
Collaborative Mobile Robots (Cobots)
As warehouse robotics technology advances, we’re likely to see increased use of Cobots – robots that are designed to interact with humans in a shared workspace. They enhance human capabilities, allowing for higher productivity levels. Collaborative mobile robots are predicted to work alongside humans, not replace them.
Autonomous Mobile Robots (AMRs)
AMRs are a game-changer for warehouse operations. They can navigate additional warehouse space without human intervention, significantly increasing productivity and efficiency. Experts forecast that AMRs will be more integrated into warehouse operations in the future, handling tasks like picking, packing, and transporting goods.
Internet of Things (IoT) and Smart Warehouses
IoT allows for real-time tracking and data collection, leading to enhanced operational efficiency. The concept of “smart warehouses” is anticipated to become more prevalent, utilizing IoT for inventory management, predictive maintenance, and energy management.
Drone Technology
Aerial inventory technology could soon play a bigger role in warehouse operations. They can be used for tasks like inventory checks and transporting small items within the same warehouse layout, reducing human effort and time. Drones equipped with RFID technology can quickly locate and identify items in large warehouses.
Advanced Analytics
The future of warehouse operations will involve making data-driven decisions. Advanced analytics tools can provide insights from vast amounts of data, enabling better demand forecasting, optimized logistics, and improved efficiency.
Sustainability Focus
As businesses strive to reduce their environmental impact, we’ll see more efforts towards making warehouse operations eco-friendly. Automation can contribute to this goal by reducing waste and improving energy efficiency.
Enhanced Cybersecurity Measures
As warehouses become more automated and digital, the importance of cybersecurity grows. Future trends are likely to see increased focus on securing systems and data.
These future trends highlight the potential for innovation and transformation within the warehouse automation space. As automated warehouse technology continues to advance, different warehouses that embrace these trends are likely to see significant improvements in efficiency, productivity, and overall operational effectiveness.
Final Thoughts on Warehouse Automation Costs
Investing in warehouse automation systems requires careful consideration of a variety of factors, beyond smart warehouse cost, including size, safety, and the nature of your supply chain.
The goal of successful warehouse automation strategies for operators should always be to improve efficiency, reduce waste, and increase customer satisfaction. While costs can be high, the potential benefits for productivity and growth can make automation a vital arm of modern warehouse operations.
In the past, robotics have specifically focused on the manufacturing sectors, but now they are hitting the logistics sector with powerful improvements in automated warehouse systems. Warehouse automation may have a big price tag up front, but these processes bring your facility into the future and allow you to compete faster and more accurately than other warehouse processes which don’t yet have automation within them.
You’ll find many cost reductions both in labor and space come with automating your warehouse. However the transition to an automated warehouse system and facility can’t be taken lightly, it must be deliberately strategic with a plan that could last months or even years to implement.

Mar 28, 2023 | Blog
The main purpose of poly mailers is to provide a secure and efficient poly shipping bags’ solution. These are versatile shipping bags, popularly used by every brand shop for mailing bags of items, including a variety of things like DVDs, small items like phone cases, and even magazines. The interior is often spacious enough to accommodate various dimensions, sizes and shapes.
What are Poly Mailers?
Poly mailers bags, also known as polythene bags or plastic mailers’ bags, are a popular choice in the realm of shipping supplies. Their popularity stems from their lightweight design, low amount, and tear proof capabilities, which can help reduce postage costs with carriers like USPS. They also offer protection from moisture and minor damages, ensuring the packages reach their destination in good health.
Different Types of Poly Mailers
There are different types of poly mailers, each with a unique purpose. The most common ones are the standard poly mailers, poly bubble mailers, poly shipping bags, and the sustainable packaging option – compostable mailers. Kraft mailers, another option, have a sturdy build and offer the same opening mechanism with a peelable lip. This guide will help you understand the difference between each type of poly mailers and their benefits.
Standard Poly Mailers: Standard poly mailers are the most commonly used shipping mailers. Brands often make poly shipping bags and use these for shipping items such as clothes, shoes, and documents. These poly mailers are made of a thin layer of polyethylene, which is a type of recycled plastic. They often have a peel-and-seal opening for easy packaging and tamper-evident envelopes for security.
Poly Bubble Mailers: Poly bubble mailers serve a similar purpose but come with a layer of bubble padding inside. This extra padding makes them suitable for shipping fragile items like electronics. Unlike traditional packing peanuts, bubble mailers’ padding ensures secure packaging without the mess. The same mailers’ exterior is smooth, perfect for attaching shipping labels and enhancing the visibility of branding.
Compostable Mailers: Compostable mailers are a green alternative to regular plastic shipping bags. They are made from compostable materials, providing a more eco-friendly shipping solution. They are becoming increasingly popular among businesses conscious of their low environmental impact.
Custom Poly Mailers: Custom poly mailers are perfect for businesses looking to add a personal touch to their website and shipments. They can be custom-printed with brand logos or other designs, increasing brand visibility and reinforcing branding.
It’s important to note that the length and size of these mailers vary by site and shop. Be sure to check the dimensions before making a purchase from your shop or preferred packaging company. The right size can ensure the safety of your items and reduce expedited shipping costs.
Poly mailers, in all their forms, offer several benefits. They’re lightweight, which can save you money on postage. They’re also waterproof, protecting your packages from moisture damage. Their tamper-evident feature adds an extra layer of security, ensuring your items reach their destination intact. Moreover, they’re customizable, allowing you to add your products’ own style and personal touch, reinforcing your brand’s identity with every shipment you ship.
Switching to poly mailers can offer numerous advantages over traditional cartons or paper mailers. Not only are they lighter and more protective, but they’re also more flexible, able to accommodate and ship a wide range of sizes of items.
For packaging materials like poly bags or poly mailers, consider the contents, the ideal shipping conditions, and the potential for damages. Your choice of packaging used can make a significant difference in your brand’s reputation and the environment.
Conclusion
So, whether you’re shipping clothes, electronics, or using discreet shipping; poly mailers can be a reliable and cost-effective solution. But remember, the key lies in choosing the right type that best serves your purpose.
FAQs
Can you put poly mailers in the mailbox?
Yes, you can put poly mailers in the mailbox. They are the bags designed to fit in standard mailboxes and are often the shipping bags used by USPS.
Are poly mailers recyclable?
Standard poly mailers made from polythene, a type of recycled plastic, are recyclable. However, it’s always good to check with your local recycling program to be sure.
Can poly mailers go through USPS?
Yes, poly mailers can go through USPS. They are a popular packaging choice for many products from many brands due to their light weight and durability, which make them ideal for shipping various items.
How do you seal a poly mailer?
Most poly mailers come with a peel-and-seal closure. Simply peel off the strip to expose, add the adhesive, fold the lip over, add, and press to secure the seal.
Are poly mailers waterproof?
Yes, poly mailers are waterproof. They are waterproof and are designed to resist moisture, offering extra protection for your items during transit.
Are bubble mailers recyclable?
Poly bubble mailers are typically not recyclable due to their interior layer of bubble padding. However, compostable poly mailers are, an eco-friendly alternative, are made from compostable materials and are recyclable.

May 14, 2021 | Blog
Every Friday for the past 5 months, a chosen lot of lucky subscribers have received The Packet email newsletter of top e-commerce news and headlines. Together we’ve laughed, cried, and learned. But most importantly, laughed. Now, we’re expanding our audience to all of you!
The Packet’s mission is to get people excited about the world around them, with a focus on spicing up the e-commerce and logistics industry. There are so many stories to share about people who create, people who build, and people who lead. The Packet is your weekly bite-sized chunks of news so you can feel more knowledgeable and confident in the world around you, and also have something to talk about whenever dinner parties are a thing again.
Why The Packet?
With all the sources of news and information out there, who has time to parse through and find truly meaningful content while also trying to grasp whatever the author is saying (or paid to say). The Packet is free, fun and formulated out of love for the e-commerce and logistics industry. No ads, no sponsored segments, completely unbiased, and we love poking fun at Daddy Bezos. (It’s like the Skimm but sometimes funny)
Like a Friend’s montage episode, let’s roll some top stories from weeks past. If you like what you see, join our community of Packeteers every Friday by subscribing here. And be sure to join the conversation on Facebook, Instagram, Twitter, and Youtube.
E-Commerce News and Headlines
The Packet
After tireless digging and tugging, the mega-ton blockage that has been constipating global trade for the past six days has finally been cleared from the Suez Canal. The global trade community has given a collective sigh of relief as vessels are now starting to pass through.
What caused this?
Besides a lack of fiber (kidding), a seasonal dust storm, known as the khamsin, blowing winds at 40 knots caused the Ever Given to veer too far right and become embedded in the canal wall. While this is the story for now, navigation experts and engineers at the Suez Canal Authority are investigating the crash for technical and human error — this could have massive insurance implications and lawsuits if a responsible party is identified.
How did they get it out?
A full moon emerged (you can’t make this up) and brought in a high tide that buoyed the engineers efforts to refloat the ship. If this attempt failed, the tide would have fallen and they would have been forced to spend weeks unloading thousands of containers to help the Ever Given sit higher in the water. In total, hundreds of thousands of cubic feet of sand were removed.
The Fallout
Shipping operators estimate $12 billion of cargo is stranded along the 120-mile canal or idling outside it. Other shipping operators have already re-routed ships around the Cape of Good Hope, adding weeks and fuel consumption to the voyage. Experts estimate that this will result in another jam once all the vessels reach their destination at the same time, and over 360 vessels are waiting to pass through the canal. As a result, shipping and oil prices have risen, and the already beleaguered logistics industry will likely face additional delays and costs.
This post has been sponsored by: MiraLAX. Blockage in your canal? MiraLAX.”
Walmart announced that they will be repurposing one North Dallas location into a fulfillment center dedicated entirely to online delivery and curbside pickup, with no more in-store shopping. As a proverbial canary in the low-price coal mine, this could signal a permanent shift towards local delivery and curbside pickup over conventional brick-and-mortar shopping.
>>Busch Beer is for the dogs
Tired of sharing your beer with your dog? Busch Beer has announced a contest to hire a doggo “Chief Tasting Officer” for its popular Busch Dog Brew, and the winner could take home $20,000! To enter, post a picture of your pooch on social media with the hashtag #BuschCTOcontest… so animal services can come pick them up. JK sounds fun, good luck.
Where to Read the Latest E-Commerce News
For the entrepreneurs who like to stay on top of trends, for the curious who love to have a global world view, and for the intellectuals who live on the edge of levity, The Packet is for you.