Dec 1, 2023 | Blog, Warehouse Operations
Managing a warehouse is about more than picking, packing, and shipping. Special projects set you apart from your competition, pad your bottom line, and help your organization to operate more efficiently and achieve its goals.
This article will discuss the role, types, mechanics, benefits, challenges, and considerations involved in special projects.
Understanding Special Projects
A special project is any request outside the normal pick-pack, receiving, or shipping processes. These requests could range from designing a custom packaging solution for a new product line to relabeling a batch of products.
In any warehouse operation, special projects can play a crucial role in helping a business adapt and innovate in response to new challenges or opportunities. By taking advantage of special projects, companies can stay ahead of the curve, improve their processes, and maintain a competitive edge.
Types of Special Projects
- Kitting: Packing multiple products under one SKU is known as kitting. Kitting combines two or more related items into one neat package or bundle. Instead of forcing customers to browse numerous options, kitted bundles make getting what they want effortless.
- FBA or Walmart Prep: Some 3PLs offer Walmart and FBA prep services for inbound receiving rules, including ASIN labeling, order packaging, and fulfillment center shipping.
- Wholesale/Retail Order Prep: 3PLs can provide transportation, order fulfillment, and inventory management services such as warehousing, distribution, shipping, handling, and tracking.
- Inventory Removal or Disposal Request: When a client wants items stored in a fulfillment center, returned, recycled, or thrown away.
- Barcoding Products: Barcode printing is time-consuming, but special projects can optimize the process by considering space, accuracy, and speed.
Process Optimization in Warehousing
The demand for companies to produce more with less has never been more pressing. Process optimization in a warehouse minimizes room for error, resulting in increased productivity and decreased operational expenses.
Using technology integration, companies can leverage predictive analytics to better forecast seasonal trends in demand and allocate resources accordingly.
The Mechanics of Special Projects
Every stage of setting up for special projects demands attention to detail, from project planning to monitoring and evaluation. With the right mechanics, special projects in the warehouse can be executed confidently and efficiently.
Project Planning
Work orders are critical for project planning in ShipHero facilities, providing a solid foundation for successful execution. With the ability to attach vital project details like images, videos, and documents, this feature ensures that every aspect of the project is accounted for, minimizing the chance of errors. You can easily track inventory movements in real-time, update progress, and assign tasks.
Watch our video walkthrough right here to learn more about work orders.
Execution
Collaboration between people with unique expertise is key to the success of these projects. Investing in employee training and development is also crucial, as it ensures your team has the knowledge and skills needed to tackle any project.
Implementing new technologies like WorkforceHero can connect employees with special projects, track data and locations in real-time, and follow your team’s progress. WorkforceHero informs decisions more comprehensively, reduces idle time by allowing you to pre-assign tasks ahead of your team’s arrival, and alerts potential improvements.
With the ability to track person-hours dedicated to each job or project, you’ll never forget to bill a client again.
Monitoring and Evaluation
Monitoring and evaluating metrics is important to ensure a warehouse operates smoothly and enables prompt and effective action to prevent supply chain failure.
It’s also essential to have a sophisticated system that can analyze and interpret large amounts of data, such as ShipHero WMS and our WorkforceHero. By continually striving for improvement and being adaptable to changing circumstances, your warehouse can thrive and maintain its effectiveness over the long term.
Watch our video walkthrough right here to learn more about WorkforceHero.
Benefits of Special Projects in a Warehouse
Prepping for special projects in a warehouse can offer several benefits to enhance overall efficiency, productivity, and operations.
- Process Improvement: Analyze and improve workflows to increase efficiency and reduce costs.
- Capacity Expansion: Improve warehouse capacity for special projects by optimizing storage space, implementing new shelving systems, or reorganizing inventory.
- Technology Integration: Use automation, robotics, or WMS to streamline operations and reduce errors.
- Inventory Accuracy: Update tracking and management systems to improve inventory accuracy, reduce stocking problems, and lower costs.
- Cost Reduction: Optimize processes to reduce labor and storage costs.
- Customer Satisfaction: Better warehouse operations resulting from special projects can improve order accuracy, faster order fulfillment, and shorter delivery times, enhancing customer satisfaction.
- Flexibility and Scalability: Special projects can make the warehouse more adaptable to changing business needs and market demands.
- Resource Allocation: Special projects help identify resource needs and allocate them more effectively, whether labor, equipment, or technology investments.
- Competitive Advantage: Special projects can give a competitive advantage by improving warehouse operations for faster response times, lower costs, and better service.
- Employee Development: Special projects improve employee skills and cross-train them, which can increase job satisfaction.
By implementing special projects in a warehouse, businesses can reap many benefits that improve operations, reduce costs, and enhance their competitiveness.
Challenges and Considerations
Special projects in warehouse operations are a unique challenge that requires effective project management.
The primary challenge is time. Effective time management through proper planning, scheduling, and monitoring to meet the deadline is essential.
Then, the project scope must be well-defined, with specific goals and deliverables outlined to ensure focus and desired outcomes.
Finally, it is essential to keep in mind the significant cost constraint. The project expenses include several factors, including monetary fees, labor, vendors, and quality control.
Workforce Training
A specific aspect to consider is the potential for workforce training and development. Warehouse workers can easily take on new challenges by providing specialized training.
The commitment and expertise of a well-trained warehouse team make them a valuable asset, enabling your business to stay ahead of the competition and be prepared for any unforeseen challenges.
Integration with Existing Systems
Warehouse operations can be complex and challenging, from managing space and inventory to mitigating risk and preparing for unexpected fluctuations in demand. Tackling these challenges is easy with the help of a warehouse management system (WMS).
As a smart nerve center for your warehouse, a WMS can provide powerful insights and optimizations that streamline your operations, protect your inventory, and drive profits.
Integration with existing systems is key, and ShipHero offers powerful integrations that ensure every part of your warehouse is covered, giving you visibility into all corners of your operation.
With ShipHero on your side, you can overcome any challenge and take your warehouse operations to new heights.
Harness the Power of Special Projects
Special projects can have a significant impact on your warehouse operations. Optimize your processes, collaborate with your team, and train your workforce to ensure their success.
While special projects can improve efficiency, enhance customer satisfaction, and increase competitiveness, they can be challenging to implement without proper workforce training and WMS integration. Evaluate your current approach and invest in advanced WMS integration for long-term success.

Key Takeaways
- Special projects are requests outside the normal pick-pack, receiving and shipping processes.
- Special projects include kitting, FBA or Walmart prep, wholesale/retail order prep, inventory removal or disposal requests, and barcoding products.
- Process optimization minimizes room for error and increases productivity with new technology integration.
- The mechanics of a special project involve project planning with work orders, execution with team collaboration and training, and monitoring/evaluating to assess outcomes.
- Benefits include process improvement, capacity expansion, technology integration, cost reduction, customer satisfaction, flexibility/scalability, resource allocation, competitive advantage, and employee development.
- Challenges and considerations involve expectations management, clearly defining the project scope, and highlighting cost constraint awareness.
- Workforce training and WMS integration are key to successful execution.
Oct 20, 2023 | Best Practices, Blog, Fulfillment, Warehouse Management Software, Warehouse Operations
Optimizing Kitting Strategies for Peak Season | Warehouse Operations
Are you feeling the pressure of peak season looming over you? We’ve been in your shoes and we know how to make it easier. We’ll dive deep into how you can improve your kitting services to boost your bottom line, from examining your warehouse layout to implementing practical automation rules.
We also consulted a few kitting pros, Alex Lewkowict of One23 Fulfillment and ShipHero kitting superstar Heather Schwartz, Director of High Touch Fulfillment, PBI, for insight into how to make kitting work for you. Let’s get kitting!
Why Kitting Matters During Peak
Kits offer best-selling products in one attractive package at an irresistible price. Customers love the convenience of these ready-made gift options (especially during the holidays), making them an easy one-click purchase. By promoting kits, eCommerce businesses can drive sales rapidly and effortlessly. With a little pre-planning, you can meet your client’s needs without hassle in your warehouse. Make sure everyone stays merry and bright!
Kitting Preparation | Before Peak
The Warehouse Layout Dilemma
Efficient kitting preparation is essential for businesses to meet peak season demands. One of the significant challenges of kitting is determining the best warehouse layout. Without a defined strategy, warehouses can end up wasting valuable space and manpower, which can lead to delays and errors throughout the shipping process. Planning ahead is essential to optimizing your physical layout for a kitting system that minimizes risk.
Balancing Disruption vs. Efficiency
It may be worth considering a dynamic “hot” pick zone to balance disruption and efficiency in your warehouse. By analyzing your SKU velocity, you can quickly identify the best locations for your fastest-moving items and create a designated area to improve efficiency.
This approach can be beneficial for high-volume items with low SKU counts and items frequently promoted by your marketing team. By implementing a hot pick zone, you can take control of your warehouse operations and streamline your processes for improved productivity and profitability.
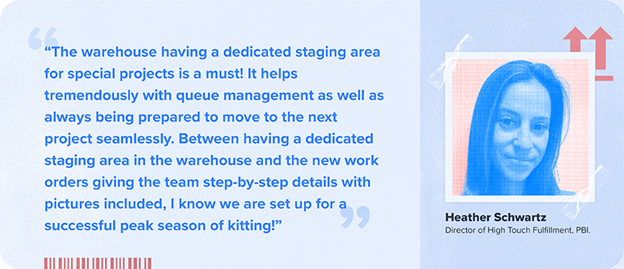
Change is Good
Alex Lewkowict overcame challenges managing kitting demands during past peak seasons by changing the kitting processes in the warehouse. One of his most notable changes was creating a dispatching station outside the pack line to streamline the packaging process.
Additionally, he constructed a more efficient pick wall using three shelves and 17 SKUs to handle the volume effectively. This allowed for quick replenishment of inventory behind the pick wall and placement of products in a temporary pallet location for easy access.
As a result, up to 500 items per hour were processed, and the need for an additional picker was eliminated. With Alex’s approach to identifying and addressing bottlenecks, kitting processes at One23 Fulfillment have a near-zero error rate at peak season.
Kitting Training for Peak
Identifying essential skills can make or break a company’s success. For example, Alex flew 10 people out from his Palm Beach warehouse to assist Las Vegas with the sudden surge in demand, exemplifying the importance of adaptability.
By recognizing the strengths of the East Coast warehouse and shifting resources accordingly, Alex was able to maintain a 95% success rate in fulfilling orders within 24 hours. This kind of strategic thinking is essential in navigating the ever-changing landscape of modern business.
Training Programs and Methods
From safety protocols to customer service, employees should be equipped with the knowledge and skills to handle various situations. Properly trained staff can uphold the company’s standards, minimize risks and ensure the satisfaction of customers.
Communication is critical, as Alex noted after visiting other warehouses where employees didn’t understand the significance of the peak season. It is crucial to ensure that your team is fully equipped to handle the increase in volume while still providing top-notch service.
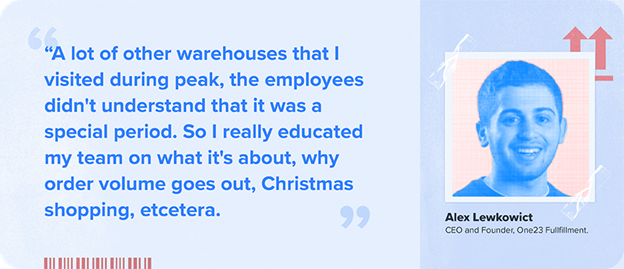
Kitting Preparation | During Peak
Kitting Strategies
As we’ve learned, don’t make drastic changes during peak season. You want to do your best to avoid bottlenecks, delays, and damages during this time. Kitting is huge for your clients, and knocking it out of the park is essential. You can optimize your kitting process and increase transparency with technology like:
- Warehouse Management System (WMS)
- Barcode and RFID Tags
- Mobile-Powered Carts
- Automated Picking Tools
- Batch and Lot Tracking
The combination of mobile carts and barcodes or RFID tags with an inventory management system can significantly expedite the process.
Just-In-Time Kitting
Effective kitting strategies are critical for managing supply chains during peak seasons. One such strategy that has proven successful is Just-In-Time (JIT) kitting. By assembling kits in the warehouse and delivering them as needed, businesses can be more responsive to demand while keeping inventory levels low. This approach can also streamline processes and make it easier for 3PLs to adapt to changing circumstances.
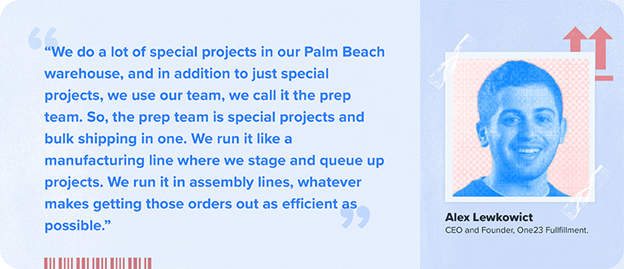
Automation Rules
Automating your kitting system helps you use your warehouse space and resources better and leads to faster product completion and delivery. An automated system eliminates the guesswork for your pickers and packers, ensuring they can complete their tasks quickly and accurately every time.
Focus Areas for Automation
ShipHero’s WMS automation is a straightforward way to automate your warehouse.
- Inserts and Packaging
- Include a warehouse note with orders that contain SKUs that require extra instructions for packaging.
- The Box Type Selection feature is handy when handling fragile items that require special packaging.
- You can include inserts here, such as thank-you notes and coupons.
- VIP Handling
- You can add a gift SKU or marketing insert to these orders, provide express shipping, and prioritize those orders on the day they need to be shipped.
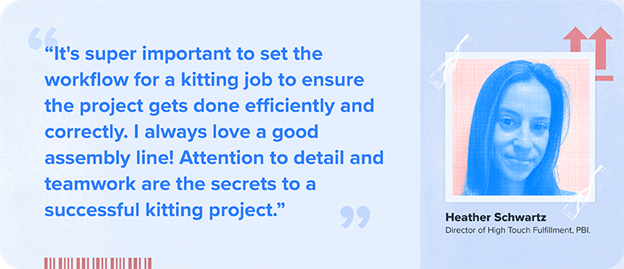
Kitting Preparation | After Peak
Post-Peak Assessment and Adjustments
Once the pressure of peak season ends, start thinking of reverting changes made to your warehouse during the peak rush.
This means moving items that were temporarily placed closer to packers back to their original positions and considering whether kitted items need to be disassembled and put back into their original inventory areas. Strategic reorganization of your warehouse layout through redesign is a big undertaking, but it is necessary for adapting to ever-changing market demands.
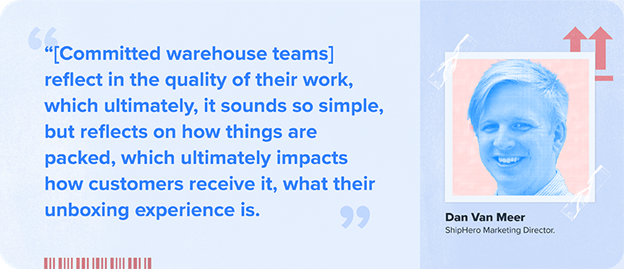
Warehouse Kitting Success
Kitting requires strategic planning and thoughtful execution, considering preparation for items like warehouse layout, employee training, automation rules, and strategic reorganization. Following our advice, you can make this peak season a successful experience.
You now have all the tools to effectively streamline your kitting services for peak season. You can ensure that the process runs smoothly with hard work and dedication. Take charge of your success and start taking action now. Don’t let this opportunity slip away; make this your most successful year yet!
Key Takeaways
- Planning ahead is essential to optimizing kitting services for peak season demands by considering all aspects of the warehouse layout.
- Consider a dynamic hot pick zone to balance disruption and efficiency in the warehouse.
- Implement changes such as creating dispatching stations outside pack lines and more efficient pick walls to improve productivity and profitability.
- Train staff properly on safety protocols, customer service, and the importance of proper preparation.
- Just-in-time kitting is an effective strategy for managing supply chains during peak season.
- Automating your kitting system can expedite product completion and delivery.
- Revert changes made during peak back to their original positions post-peak.

Oct 6, 2023 | Blog, Fulfillment, Warehouse Operations
Staying ahead of the curve is crucial in the fast-paced third-party logistics (3PL) world. That’s precisely what 360Pro Fulfillment, a rising star in the fulfillment industry, achieved by teaming up with ShipHero. In this blog, we’ll dive into their journey and explore how ShipHero’s innovative software solution turned their challenges into triumphs.
Meet 360Pro Fulfillment: A New Player with a Fresh Approach
Founded in 2021, 360Pro Fulfillment is a three-person team with big dreams. Their mission? To provide top-notch 3PL services that streamline supply chain operations and put smiles on their clients’ faces. In a recent chat with Sean Doherty, Director of 360Pro Fulfillment, we uncovered their unwavering commitment to customer satisfaction and innovation. With a dynamic team like theirs, 360Pro Fulfillment is undoubtedly one to watch in the coming years.
Navigating a Maze of Challenges
Before the ShipHero partnership, 360Pro Fulfillment was entangled in a web of frustration. Their previous 3PL software provider left them dealing with inventory discrepancies and needing better process alignment. They needed a game-changer, and it came in the form of ShipHero.
“Sitting in the client seat, we wanted a different system – and then getting to know the other side of that equation where we’re the 3PL. I think I have a much different understanding of the system compared to what I did with Shipstation.” -Sean Doherty, Director of 360Pro Fulfillment.
Experience Smooth Sailing Ahead
ShipHero didn’t just solve their problems; it set them up for success. They received a comprehensive suite of services, including 3PL software, client portals, and seamless QuickBooks invoicing through CSVs generated by ShipHero. Even as a remote owner/operator, Sean found the platform incredibly user-friendly and intuitive. And let’s not forget the mobile app for order fulfillment, a real game-changer!
But it didn’t stop at the ease of use. ShipHero offered invaluable support in onboarding and connecting new clients. This made transitions seamless, fostering better collaboration and a smooth learning curve. Their tech support was top-notch, ensuring quick issue resolution and boosting overall satisfaction.
“One of the most attractive features was the onboarding that was offered. We had weekly calls, and it was a really great introduction. Then, between calls, I could access the different videos and articles to bring myself up to speed.” -Sean Doherty, Director of 360Pro Fulfillment.
Growth and Collaboration
Thanks to ShipHero, 360Pro Fulfillment has expanded its client base and improved collaborations. ShipHero’s resources empowered Sean to guide clients through integration and connection processes, providing real-time data access for informed decision-making.
Sean’s ambitious goal of reaching one million orders annually suddenly became more achievable as ShipHero proved its mettle during significant events, like a Good Morning America promotion that triggered a flood of orders.
“Have had a goal now to get to 1,000,000 orders on a yearly basis, and that was set because USPS tells me our next price break would be at a million orders. So we haven’t reached it yet, but I’ve always been fully confident that we will get there.” -Sean Doherty, Director of 360Pro Fulfillment.
ShipHero’s Game-Changing Impact
360Pro Fulfillment is a staunch advocate for ShipHero, citing its user-friendly interface, responsive tech support, and robust resources as key strengths. The platform has been the linchpin in their global scaling journey, fortifying their position in the fulfillment industry.
As 360Pro Fulfillment grows, its strategic approach to order fulfillment will revolve around ShipHero’s software. This includes delving into bulk shipping and mobile picking features to enhance results and performance.
“Our team is much more a Bulk Ship mentality team. They really like using the Bulk Ship feature and printing through the desktop. They have fun with the mobile app and they’re all able to use it.” -Sean Doherty, Director of 360Pro Fulfillment.
The Bottom Line: Unleash Confidence and Peace of Mind with ShipHero
360Pro Fulfillment’s journey is a testament to ShipHero’s transformative power. They’ve achieved seamless and efficient fulfillment services with a user-friendly interface, a reliable support team, and nifty features like Bulk Ship and PostHero. If you’re in the 3PL game and seeking a software solution that simplifies warehouse operations and ensures accurate fulfillment, ShipHero should be on your radar.
ShipHero isn’t just a partner; it’s a catalyst for growth and efficiency in the dynamic third-party logistics world. Don’t miss out on the transformation – take your fulfillment game to the next level with ShipHero.

Sep 1, 2023 | 3PL Warehouse Management, Best Practices, Blog, Fulfillment, Warehouse Operations
When preparing goods for shipment, the packing station is a crucial stage that requires careful attention to detail. Optimizing packing flow and station setup ensures accuracy and speed, thus reducing mistakes and improving the overall efficiency of your fulfillment operation. This article will discuss the importance of packing station setup and flow in successful order fulfillment.
Key Principles and Purpose
We recommend following a few basic principles.
- Avoid rushing to pack orders; take the time to check items before fulfillment to reduce the likelihood of returns.
- Store order preparation supplies in one location for quicker packaging and prevent potential order delays or losses.
- Designate a storage area for packaged products before shipping.
Watch one of our informative videos where our CEO, Aaron Rubin, shares valuable insights on setting up a successful packing station – right here! Some principles he discusses include minimizing touches, maintaining one-direction flow, and avoiding the use of keyboards and mice.
The Purpose of a Packing Station Setup
Determine the primary goal and select the appropriate tools and materials. If you’re working at a shipping station, your tasks may include combining orders, performing final quality checks, packaging, addressing and labeling, generating a manifest, and staging.
You can develop a packing station tailored to your requirements by organizing and defining these tasks. Planning final checks to ensure the products are of the highest quality is essential. Identify the locations where the inspections will occur and devise a strategy to manage damaged or defective items.
Packing Station Flow
To optimize your fulfillment process, pay close attention to the flow of your packing station. Ensure that the products are moving clearly and consistently throughout each stage of the packing process. One way is by implementing signs or arrows dictating the proper directions. Additionally, designing your packing station for a seamless transition between each step can lead to a more efficient work environment.
When setting up your workstation, consider how items will be received. Will they come in via a conveyor belt system, or will you need a manual or cart-based system? If you’re using a conveyor belt, it’s best to have a custom standalone workbench over it.
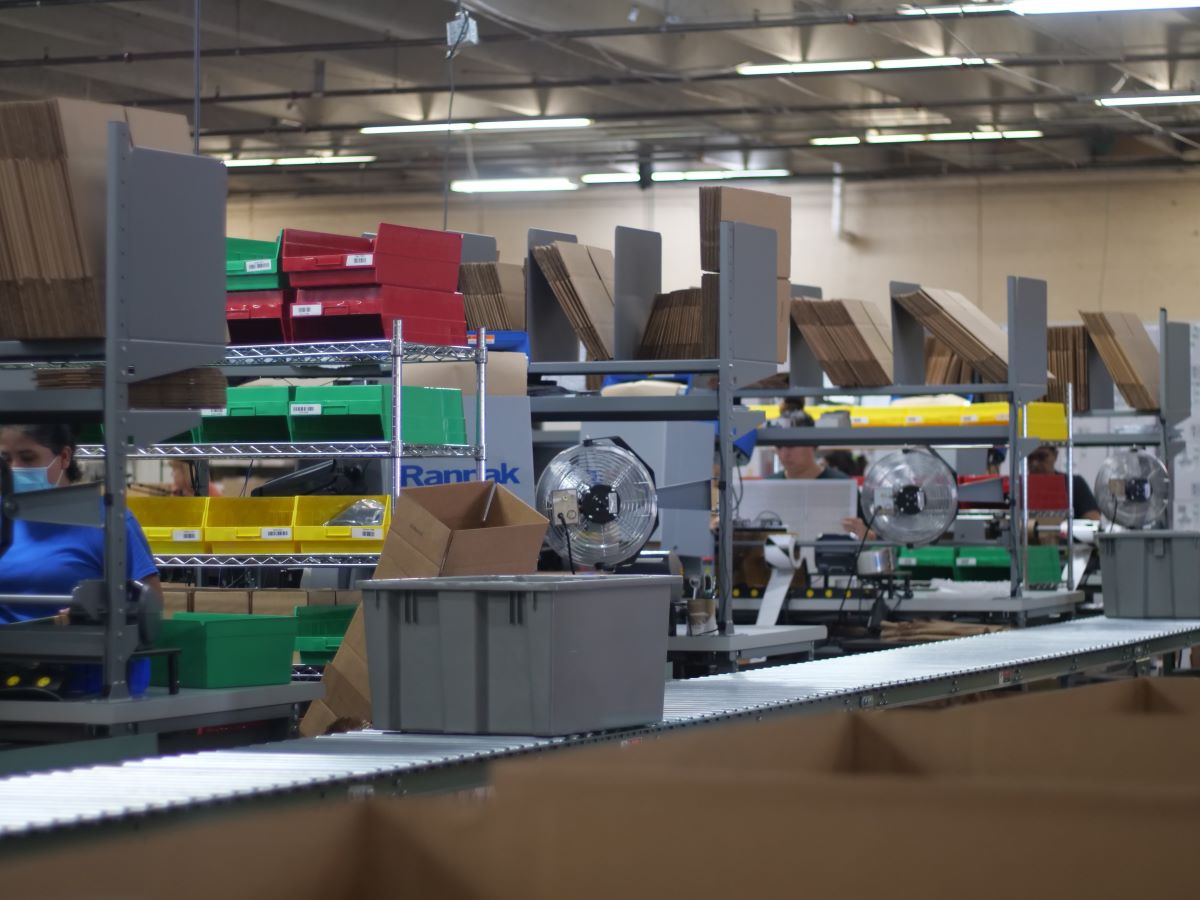
Setting Up an Effective Packing Station
When setting up a packing station in your warehouse, there are two factors for you to begin with – proximity and materials. It’s important to position the packing station close to the picking areas. This will allow for swift movement of items from picking to packing, minimizing delays.
When it comes to materials, prioritize the items used most often. Ensure your packing area has an adequate supply of commonly used items so your employees can keep the orders moving smoothly.
Essential Packing Station Equipment and Tools
Having the appropriate equipment and tools to create a practical packing station is important. Some essential items to include are:
- Packaging Materials: Boxes, bubble wrap, packing peanuts, envelopes, labels, stationery, and void fill.
- Tools: Heat sealer, stapler gun, glue, and scales.
- Quality Control Tools: Weigh scales, computers, monitors, printers, scanners, label printers, and barcode scanners.
Once you have the appropriate tools and equipment, your packing station will be fully equipped to handle any shipment promptly.
Ergonomic Design Considerations for Packing Station Setup
When planning the layout of a packing station, it is crucial to consider ergonomics. Properly arranging goods and materials reduces the risk of work-related injuries, while worker morale and productivity can be increased.
The necessary tools and materials should be easily accessible to the packer and organized by the frequency and sequence of their use. Remember to include features such as optimal workstation height, sufficient lighting, and comfortable seating.
Replenishment
It’s crucial to prioritize the replenishment process, which is often overlooked but can significantly impact operations. You can make the most of your replenishment process by following best practices and choosing the most suitable method for your specific needs.
Also, remember to have a solid emergency plan for replenishment needs. You can streamline this process by configuring triggers in your WMS for automatic re-ordering or using collaborative robots to assist with picking and restocking.
It’s essential to maintain an organized and easily accessible stock of packing supplies and tools for your workers. Remember to replenish these items from behind the packing station to avoid hindering workflow in the front.
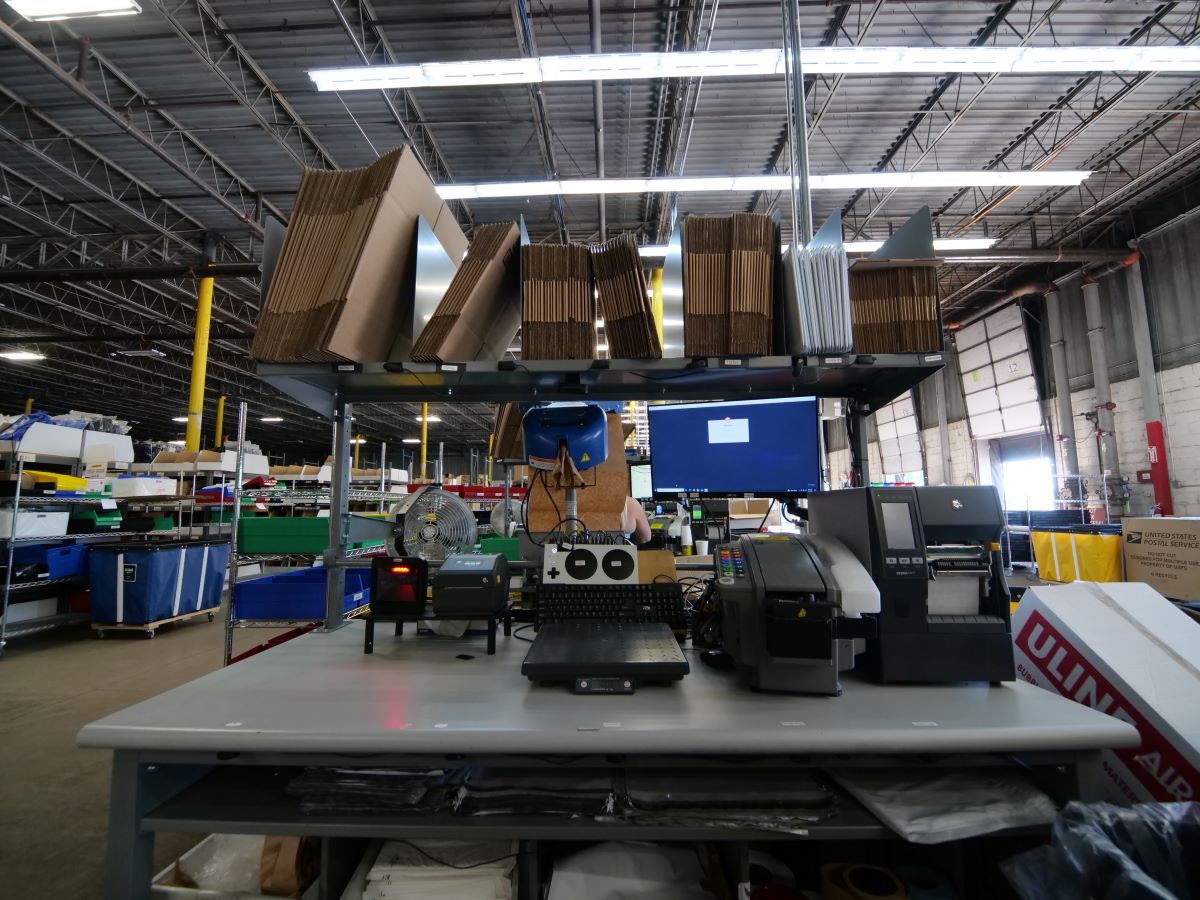
The Significance of a Packing Station in Ensuring Error-Free Fulfillment
To guarantee accurate order fulfillment, utilizing technology that automates processes and integrates with warehouse management systems is essential. This can include automated sorting and routing of packages, which can help reduce errors and prevent bottlenecks
We strive to enhance the packing process with inventive solutions, including one-touch and hands-free pack stations. By minimizing the handling of items, we can optimize the process. We provide adaptable pack stations that cater to different requirements.
Handheld barcode scanners have undoubtedly changed the warehouse picking and packing game. However, there’s no denying the lag between scanning barcodes and continuing work can be incredibly frustrating, adding unnecessary seconds to each order. To overcome this inefficiency, our team searched high and low for a non-wearable option that was both durable and cost-effective. Our solution came from an unlikely source: the gaming industry. With the Xbox® adaptive game controller, we found a way to streamline our packing stations without breaking the bank. When paired with the Logitech® button kit and some innovative open-source software, this controller has revolutionized how we pack orders.

Maximize your 3PL and Warehouse Potential
As we have seen, the packing station is an important component of any order fulfillment process. It is essential to consider principles such as minimizing touches, maintaining one-direction flow, and avoiding keyboard or mouse use when designing a packing station setup. Furthermore, having the necessary equipment and tools available and being mindful of ergonomic design considerations facilitates accuracy. By integrating warehouse management systems with automation technologies, companies can ensure effective order fulfillment while minimizing errors. Ultimately, it’s important to take stock of your current workflow and processes to identify opportunities for improvements that could give your organization an edge in the ever-evolving eCommerce landscape. Now it’s time to ask yourself: How does your packing station add up to the competition?

Aug 11, 2023 | 3PL Warehouse Management, Blog, Warehouse Operations
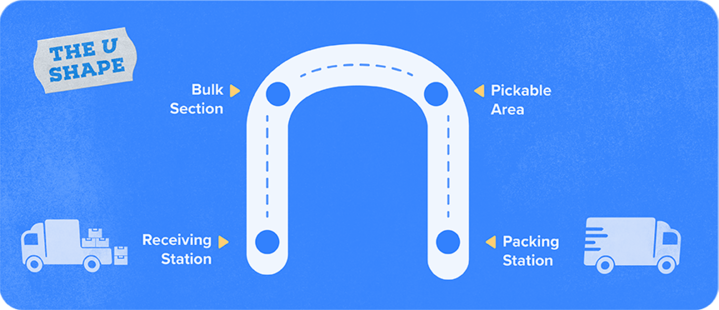
The Importance of Efficient Warehouse Flow
Efficient warehouse flow is crucial for any warehouse to run smoothly. A well-managed warehouse ensures products are received, stored, and distributed seamlessly. In this blog post, we’ll go over the basics of warehouse flow, from receiving to outbound packaging, and why optimizing each step is essential. Whether you’re a warehouse expert or a curious reader, this blog post will provide valuable insights into warehouse operations.
U-Shape Flow – How ShipHero Does It
Most warehouses have a square or rectangular shape with receiving and outbound doors on one side, creating a U-shaped flow. There is usually ample space between the dock and receiving area, where products are sorted. Having more room than you need to avoid congestion or delays will come in handy.
Receiving
Once products are ready to be received, they are taken to the receiving station. This can include fixed or mobile stations, depending on the volume of products being handled. Receiving is a critical aspect of warehousing, and nothing gets past the receiving station if it has not been checked or labeled. Items that pass inspection are ready to be put away, while non-compliant items are labeled accordingly.
Bulk Section
The next step in warehouse flow is the bulk section. This is where the overstock pallets are stored until they are needed. From there, products move to the pickable area, where pickers select items for packing. As inventory is moved out of the warehouse, items are moved from the bulk section to the pickable area, where pickers can easily access them.
Picking and Packing
Pickers typically move around the warehouse with carts, selecting individual units from bins. Once all necessary items have been selected, they move to the packing station. This is where orders are finalized, labeled, and packed into boxes.
Outbound Packages
After preparing your packages, they will be taken to the outbound dock to be shipped. We typically use collapsible bulk containers for storing outbound items. Choosing a reliable shipping method is important to ensure safe and secure delivery. We recommend reputable options like USPS or FedEx.
Why Warehouse Layout is Important
An efficient warehouse layout is vital for a successful logistics operation. The layout plays a significant role in productivity, cost-effectiveness, and customer satisfaction, making it an essential factor to consider when setting up a warehouse. Let’s look at the various aspects that an optimized warehouse layout can improve.
- Optimized Material Flow: Efficient warehouse layout improves material flow, reducing handling time and movements. This leads to quicker order fulfillment, shorter lead times, and improved customer service.
- Enhanced Productivity: A well-planned warehouse layout can boost productivity by reducing the time and energy needed to find, choose, and pack items. This means less travel distance for workers and higher throughput and order processing.
- Space Utilization: Layout planning to maximize available space helps reduce storage expenses, keep the area clean, and increase inventory storage capacity.
- Safety and Ergonomics: Prioritizing safety when designing warehouse layouts can prevent accidents, protect employees, and reduce damage to goods. Ergonomic warehouse designs can lessen worker fatigue and injuries.
- Inventory Accuracy: A good warehouse layout assigns specific locations for each SKU to improve inventory accuracy. This reduces the chances of misplacement or incorrect picking, resulting in more precise inventory counts and less risk of stockouts or overstocking.
- Efficient Order Fulfillment: A thoughtfully designed warehouse layout ensures that popular or fast-moving items are strategically placed closer to the shipping area, expediting the picking and packing process for high-demand products.
- Adaptability to Changing Needs: Flexible and easily adjustable warehouse layouts are crucial for businesses adapting to new market conditions. Seek arrangements to accommodate changing storage needs, new products, and different order profiles without disrupting ongoing operations.
- Integration with Technology: Efficient warehouse layouts that accommodate modern technologies like ShipHero WMS, barcode scanners, and automation are crucial for optimizing productivity, accuracy, and data-driven decision-making.
- Cost Optimization: An optimized warehouse layout directly impacts operational costs. You can achieve significant cost savings and allocate resources more strategically by reducing labor, storage, and material handling expenses.
- Competitive Advantage: A well-organized warehouse can give businesses a competitive edge by enabling faster order processing and lead times. This leads to better customer service, increasing customer satisfaction and loyalty.
So Many Benefits
Understanding warehouse flow is critical to running a successful operation. Utilizing the U-shape flow model and optimized warehouse layout can provide numerous benefits, such as faster material transit time, enhanced productivity, cost optimization, and more. It’s also important to recognize the impact of technology on efficient fulfillment delivery and provide an environment that is safe for employees. Having the proper infrastructure makes a big difference in improving customer experiences and ultimately attaining business success.
If you want to visualize efficient warehouse flow, click here to watch our detailed walkthrough videos for further insights into best practices for warehouse operations.
