Oct 17, 2022 | Blog
One of the biggest challenges facing the owners of eCommerce businesses is managing inventory. If you don’t have an accurate picture of the inventory that’s in highest demand by your target audience, you may end up not having enough inventory to fulfill orders, or you could end up overstocking items that aren’t selling.Â
There are several different ways to approach inventory management. One approach that may be used to increase efficiency is known as a just-in-time inventory system, sometimes called JIT or JST Inventory. Â
What is a Just-in-Time Inventory System?
A just-in-time inventory system is an inventory management system in which goods are received from suppliers only when needed. Different businesses may have different ways of implementing this method, but the idea is that the production and shipping of products is based on actual orders. Raw materials for production arrive when production begins and not sooner. The goal is to eliminate waste and limit the amount of inventory on hand.
For an eCommerce business to be successful, client satisfaction has to be a top priority. Just-in-time inventory control helps to optimize inventory so that your company only has on hand what’s actually needed. This can help to improve your return on investment by reducing nonessential costs.
Benefits of Just in Time Inventory Control
There are several benefits of using JIT. Some benefits of using this method of inventory management include:
- Less waste – Since this system revolves around client demand, there’s less waste involving unneeded items. When you only order what you need, you don’t end up with excessive unusable inventory. This allows manufacturers to quickly move on to production of different items if necessary.
- Saves money – There’s a lower upfront investment since less money is spent unnecessarily on raw materials. Labor expenses may be lower when there’s less inventory to handle.
- Reduced storage needs – Unwanted and unsold inventory doesn’t take up valuable warehouse storage space. This may eliminate the need for a large warehouse and can also reduce storage overhead costs such as rent and electricity.
- Eliminates or reduces production delays – When only wanted items are being produced, there’s less chance your clients might be impacted by production delays.
Using this method can improve productivity and delivery times since the time and resources needed for order fulfillment aren’t being spent on unnecessary stock. Less inventory means less chance of items held in storage being damaged. It also means it’s less likely you will end up with stock nobody wants that has to be cleared at a lower price.
JIT can be especially beneficial to new businesses that don’t have a lot of cash available that would normally need to be tied up in inventory. This approach can help to reduce costs so it’s a good idea to use this method when you have limited warehouse space or limited staff to manage inventory or perform inventory audits.
Drawbacks to Just in Time Inventory
While there are many benefits to using the just-in-time system, there are a few possible drawbacks to keep in mind when choosing to use this method of inventory management. One risk that businesses take when they use just-in-time inventory control is that a disruption in the supply chain means there’s usually no backup stock to fill new orders. This could end up delaying production and delivery when clients place additional orders. This type of disruption means sales could come to a halt.
If orders for products are more than the amount forecasted, shortages can create delays in fulfilling orders. For just-in-time inventory to work, your business needs to be able to rely on timeliness and top performance from suppliers. There are no guarantees that suppliers can consistently deliver items promptly. Sourcing raw materials locally can help shorten the time it takes to receive materials.
Tracking and Organizing Inventory
Just-in-time processing requires accurate data to manage inventory, meaning that all inventory has to be carefully tracked and organized. It’s imperative that your eCommerce business accurately determines inventory forecasts.
An effective way to do this is by using real-time inventory tracking with SKUs, which are stock-keeping units. The technology behind SKUs makes it possible to track stock digitally. This can help you to be aware of what items are in the highest demand and when items need to be replenished.
Is Just-in-Time Inventory Management Right for Your Business?
Just-in-time inventory management is often a good choice for small businesses that need to limit the amount of money they invest in inventory upfront. With fewer items in inventory, the return on investment may be higher. Another benefit to keeping fewer items in inventory is improved quality control. With fewer items to manage, there’s a better chance of a lower rate of breakage and improved ability to find production errors.
A just-in-time system can cut costs and reduce waste but there’s little room for error or supply chain disruption. In order for a just-in-time system to run smoothly, it’s important to accurately forecast orders and track current stock using available real-time technology.
To find out more about ShipHero’s fully outsourced fulfillment solution, talk to one of our Fulfillment Experts today.
Click HERE to Schedule a Meeting with Our Sales Team.Â
About ShipHero
ShipHero is a US-based, leading solution provider in the fast growing eCommerce fulfillment space. ShipHero served over $5 billion of eCommerce orders in 2020 and is growing rapidly. ShipHero provides warehouse management software for brands that operate their own warehouses as well as outsourced fulfillment as a service from ShipHero owned and operated North American warehouses. Some notable customers include Universal Music Group, Glossier and Canadian Tire. ShipHero is a Shopify Plus partner and more than 10% of Shopify Plus stores globally use ShipHero.
Follow us today on Twitter and LinkedIn.
Oct 17, 2022 | Blog
Understanding the contrasts between push and pull supply chain strategies is key to effective operations, especially in a world of fluctuating customer demands. As the scale of these demands grows, the question arises: which strategy is most effective for my operation? Â
This article discusses the importance of these strategies, their impact, and real-life examples.
What is a Push System?
A push system anticipates supply chain operation plans, inventory levels and activities in advance, based on forecasts and projections. It represents the initial point of the supply chain cycle, focusing on the warehousing and transportation of goods. A push system helps you anticipate future demand and manage inventory accordingly.
The push strategy focuses on predictions. It uses forecasts to plan inventory levels, procurement, and the distribution centers’ activities. While this supply chain strategy still requires a level of predictability, it is robust against demand uncertainty and maximizes capacity utilization in the best warehouse fulfillment centers. This strategy is an innovation in the supply chain and production process that helps in solving the problem of demand uncertainty. However, its effectiveness depends on the accuracy of methods of how to forecast demand and the data used.
What is a Pull System?
A pull strategy, on the other hand, responds directly to customer demand, ensuring flexibility and efficiency. Both strategies aim to deliver the right products at the right times. Read more about push and pull strategies here.
In contrast, the pull strategy is customer-first. It bases operations on actual customer demand rather than predictions, offering flexibility in response to changes in immediate consumer demand and patterns. This strategy plays a key card in meeting immediate customer needs, hence enhancing customer experience. It provides solutions to the problem of sudden changes in demand.
Pull Supply Chain Strategies
Pull strategies are a form of stock management in just-in-time. They aim at minimizing stock and focusing on last-minute supply. Under this strategy, the product is pushed into the supply chain whenever customer demands justify it. Those companies that operate under this strategy are examples of companies that wait until they have received an order to build their own computers and sell the product. A pull strategy can help businesses minimize costs by carrying as much inventory that can’t be sold. If a company doesn’t increase production in definite quantities, it risks losing the supply and demand for fewer products.
Real-World Example: How Walmart’s Supply Chain uses a hybrid push-pull system
Walmart provides an excellent example of the use cases of both push and pull warehousing strategies at scale. Their utilization of a hybrid push-pull strategy with data insights for inventory management and demand response illustrates the importance of these strategies in different steps for enhancing customer satisfaction, reducing waste, and increasing revenue. This is a use case that shows how these strategies matter in real-world situations.
Impact of Push and Pull Strategies on the Bullwhip Effect and Consumer Demand
The bullwhip effect describes the magnified fluctuations in orders that often occur in most businesses as customer demand ripples through the supply chain. Effective use of push and pull strategies can help mitigate this effect, creating a more balanced and responsive supply chain. This is where the goal of these strategies comes into play.
Impact of Technology on Both Push vs Pull Systems in Supply Chain Strategy
Technology is an instrumental tool for both push-and-pull supply chain strategies. Under a push supply chain strategy, technologies like AI and machine learning can improve the accuracy of forecasting, helping businesses better anticipate customer demand and plan their inventory accordingly.
On the other hand, in a pull strategy, technologies like IoT can enhance real-time visibility into customer demand, triggering the production or delivery of goods exactly when needed. Also, technologies like blockchain can provide a secure and transparent way of tracking goods in both pull systems and strategies, thereby reducing risks and improving trust.
How do Inventory Management Strategies Change Between a Push and Pull System?
In terms of inventory management and manufacturing processes, a push strategy often relies on maintaining safety stocks to buffer against forecast inaccuracies and sudden demand changes. Techniques like the Economic Order Quantity (EOQ) model can be used to balance order size and frequency, minimizing overall inventory costs. Conversely, a pull production strategy typically employs methods like Just-in-Time (JIT) inventory, where goods are produced or ordered to meet actual demand. This approach minimizes stockholding costs but requires accurate demand sensing and quick response capabilities.
Risk Management in Supply Chain
Risk management in a supply chain varies between push strategies and pull strategies. A push strategy can guard against supply disruptions by maintaining a safe stock, but there is a risk of overproduction if demand forecasts are inaccurate. On the other hand, a pull production strategy, relying on actual demand, can minimize overproduction and stockholding costs. However, it requires a more robust system to prevent stockouts during sudden demand surges or supply interruptions.
Choosing Between Push and Pull Strategies
Choosing between a push and pull strategy for your own supply chain management strategy involves considering several factors, each with its unique impact on your supply chain efficiency and operation:
- Business Model and Product Nature:
The nature of your products and your business model plays a significant role. Are your products long-lasting, or do they have short lifecycles? Is your market stable, or does it fluctuate frequently?
- Demand Predictability
If your business experiences predictable demand patterns, a push strategy could be effective. It allows for accurate forecasting, efficient inventory planning, production scheduling, and engaging with distributors. However, the risk here is overproduction if demand is overestimated or changes unexpectedly.
- Market Volatility
On the contrary, if your market is highly volatile, a pull strategy might be better. This strategy is flexible and customer-centric, enabling you to respond swiftly to demand changes. By focusing on customer demand sensing, real-time communication, just-in-time inventory, and strong supplier engagement, waste can be significantly reduced, and customer satisfaction can be improved.
- Real-Time Data Management
The pull strategy’s effectiveness largely depends on your ability to manage real-time data and ensure supplier flexibility. Thus, your infrastructure capability to handle real-time data should be a key consideration.
In summary, the choice between push and pull-based supply chain management strategies should be made after carefully analyzing your capacity for demand forecasting, understanding the volatility of your supply chain partners and market, considering your product lifecycle, and assessing your capability to manage real-time data. Such comprehensive analysis can guide you in implementing the most effective strategy for your supply chain.
Implementing a Push Strategy in Your Supply Chain
Implementing a push strategy in your supply chain inventory system can be an effective way to control your inventory and manage demand. Here are some steps to a push system to follow:
Accurate Demand Forecasting
Use historical data, market trends, and predictive analytics tools to generate accurate demand forecasts. Understand the patterns, peak times, and seasonality in your business.
Inventory Planning
Based on both production and demand forecasts, plan your inventory. This includes determining safety stock levels to buffer against unexpected changes in demand or supply.
Production Scheduling
Schedule production to match the forecasted demand. This ensures that sufficient goods and raw materials are produced in advance to meet customer needs.
Distributor/ Retailer Engagement
Engage with distributors or retailers to ensure that products are delivered at the retail store at the right time. This requires effective communication and coordination.
Monitoring and Adjusting
Regularly review the forecast accuracy and make necessary adjustments. This ensures your push strategy remains effective even as market conditions change.
A push strategy requires a robust infrastructure for data collection, storage space analysis, and communication with production processes. Also, it requires a certain level of predictability in future demand itself. If implemented effectively, a push strategy can help you maximize your supply chain’s efficiency and utilization.
Implementing a Pull Strategy in Your Supply Chain
A full pull system and strategy is driven by actual customer demand, allowing for a more flexible and responsive supply chain. Here’s how to make pull systems and implement it:
Customer Demand Sensing
Implement real-time data collection systems to sense and meet customer demand more accurately. This data integration ability could involve point-of-sale data, online traffic analytics, or customer feedback.
Real-time Communication
Set up real-time communication with suppliers and manufacturers. When a sale is made, the information is instantly relayed, triggering a replenishment order.
Just-in-Time Inventory
Adopt a Just-in-Time (JIT) inventory approach. Produce or order goods as needed based on actual or anticipated demand, reducing costs and minimizing inventory costs.
Supplier Engagement
Establish strong relationships with suppliers. The pull strategy requires suppliers to be flexible and responsive to changes in demand.
Continuous Monitoring and Adjusting
Keep track of key performance indicators such as lead times, order fulfillment rates, and stockout rates. Use this data to continuously optimize your pull strategy.
While a pull strategy requires a significant level of coordination and real-time data visibility, it can reduce waste, minimize stockouts, and improve customer satisfaction. Implementing a pull strategy is particularly effective in highly volatile markets or for products with short lifecycles.
Concluding Thoughts
In a rapidly changing world, it is essential for retailers to adapt their supply chain strategy strategies to stay ahead in their operations. With careful planning and capacity utilization, supply chains can effectively meet customer demands. The result is a more efficient and responsive supply chain that benefits economies at large. After all, in the world of supply chain management, retailers hold the cards and everything counts.
To find out more about ShipHero’s fully outsourced fulfillment solution, talk to one of our Fulfillment Experts today.
Click HERE to Schedule a Meeting with Our Sales Team.Â
About ShipHero
ShipHero is a US-based, leading solution provider in the fast growing eCommerce fulfillment space. ShipHero served over $5 billion of eCommerce orders in 2020 and is growing rapidly. ShipHero provides warehouse management software for brands that operate their own warehouses as well as outsourced fulfillment as a service from ShipHero owned and operated North American warehouses. Some notable customers include Universal Music Group, Glossier and Canadian Tire. ShipHero is a Shopify Plus partner and more than 10% of Shopify Plus stores globally use ShipHero.
Follow us today on Twitter and LinkedIn.
Oct 17, 2022 | Blog
Proactive inventory management is a vital part of running a successful eCommerce business. While managing inventory can be challenging, using a proactive rather than a reactive approach to inventory management may help to prevent problems such as inventory shortages, concerns about storage space and delayed fulfillment of orders.Â
When inventory isn’t effectively managed, clients may end up dissatisfied over out-of-stock items and the reputation of your company may be damaged. The best practice in inventory management is to be as proactive as possible.
Collect Inventory Control Data
Inventory control is the process of managing inventory levels in the warehouse and other locations. An effective inventory control system monitors the movement and storage of items and can help with forecasting and reordering. Effectively controlling inventory requires knowing what’s in stock and where it’s located while keeping items in inventory organized and in good condition.
Effective inventory management depends on knowing when to reorder products and how much to order to ensure that the right amount of inventory is on hand at the right location. To improve inventory control practices, start with collecting data on practices that involve your inventory from initial orders to shipping and receiving to restocking.Â
Identifying Inventory Control Problems
A good place to start working to identify inventory control problems is by reviewing past trends, particularly times when there was a problem with the amount of inventory on hand. Have you been scrambling to fill orders because of insufficient inventory? Or is unwanted inventory taking up valuable warehouse space?Â
Inventory that’s held too long has an increased risk of damage and keeping too much inventory ties up capital that could better be used elsewhere. All aspects of your stock must be tracked and managed, which includes tracking the quality of stock you receive from suppliers. How often is merchandise returned because it’s defective or broken?Â
Using Technology for Automatic Stock Control
Small businesses may use a spreadsheet as a manual inventory control technique but using manual processes to control inventory can be labor intensive and increases the risk of human error. Continuous advances in technology make stock management much simpler than it used to be, and automated systems can keep track of stock levels and can easily provide an accurate picture of inventory at multiple locations.
Review your current processes and identify tasks that can be automated. Stock management using automated systems and processes starts by assigning a unique identifier for each item known as an SKU (stock keeping unit). These unique identifiers make it easy to determine where the item is located and whether demand is higher for certain items or certain colors. Fast-moving and in-demand items are easily identified and time isn’t wasted trying to locate specific items.
Software to Improve Inventory Control
Inventory control software makes it easier to be proactive about tracking inventory as well as keeping track of packing and shipping information. Inventory costs can be kept under better control by using real-time updates on stock movements so that stock levels can be monitored automatically and alerts can be provided when stock is low and needs to be replenished.Â
Real-time tracking provides up-to-date information that can guide your business decisions. Leveraging the information provided by real-time metrics provides performance information that can help you stay ahead of your competitors.
Categorize Your Inventory
Look for ways to categorize your inventory based on demand. Are some items seasonal or in demand only at certain times? Your inventory can be categorized by groups such as profit margin and cost of storing it.Â
Collect data from all areas of operation, which includes shipping and receiving along with inventory being held on hand. Review the methods you’re currently using to categorize inventory and how effectively it’s working to meet demand. A good way to be proactive is to gain a clear understanding of the entire supply chain such as shipping times and results you can expect from receiving and shipping items. Consider errors that have been made and what changes could be made to reduce the possibility of making a similar mistake.
Optimizing Inventory Control
Having a proactive inventory management system in place means utilizing available technology and continually working to improve inventory control practices. Manual processes and outdated software can slow the growth of your business and lead to costly errors.
There are many factors involved in identifying and maintaining optimal stock levels. Understocking and overstocking both need to be avoided. Setting minimal stock levels can help prevent running out of items. Track items regularly to identify what’s highest and lowest in demand.
Proactive inventory management includes ensuring that inventory records are accurate. Plan on performing regular audits to identify inaccuracies, theft or damaged items. An inventory audit provides detailed information on the value of your inventory and can help to optimize inventory control and contribute to a more proactive way of managing inventory.
To find out more about ShipHero’s fully outsourced fulfillment solution, talk to one of our Fulfillment Experts today.
Click HERE to Schedule a Meeting with Our Sales Team.Â
About ShipHero
ShipHero is a US-based, leading solution provider in the fast growing eCommerce fulfillment space. ShipHero served over $5 billion of eCommerce orders in 2020 and is growing rapidly. ShipHero provides warehouse management software for brands that operate their own warehouses as well as outsourced fulfillment as a service from ShipHero owned and operated North American warehouses. Some notable customers include Universal Music Group, Glossier and Canadian Tire. ShipHero is a Shopify Plus partner and more than 10% of Shopify Plus stores globally use ShipHero.
Follow us today on Twitter and LinkedIn.
Oct 14, 2022 | Blog
At ShipHero, we are thrilled to work with some awesome brands that make and sell awesome products. We’ve rounded up a handful of our favorites to highlight for this holiday season. Read on and make your shopping list with some of the hottest gifts on the market this year from the most interesting brands.
Bushbalm
Bushbalm is the skincare everywhere brand, focusing on ingrown hairs, razor burn, and more.Â
The Hottest Bushbalm Gift This Holiday?
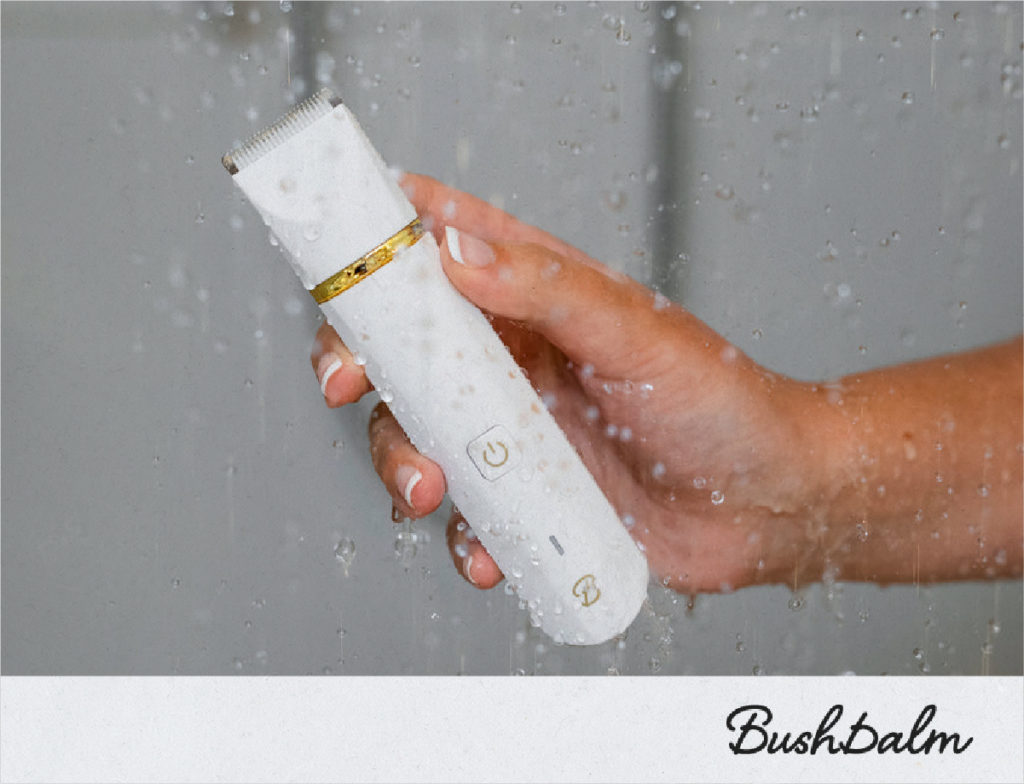
The Francesca Pubic Hair Trimmer
The Francesca Pubic Hair Trimmer was designed with comfort in mind, making it easy to use whether you trim, groom, or remove your body hair. It’s conveniently waterproof and features a strong 6000 RPM motor, up to 5 hours of battery life, as well as a USB cord for recharging. The pre-wax and shaving guard gives you the optimal height for trimming anywhere hair grows on your body. Think bikini line, legs, underarms, and neck.
Guest In Residence
Introducing Guest In Residence, a 100% cashmere knitwear brand envisioned by Creative Director Gigi Hadid.
The Hottest Guest In Residence Gift This Holiday?
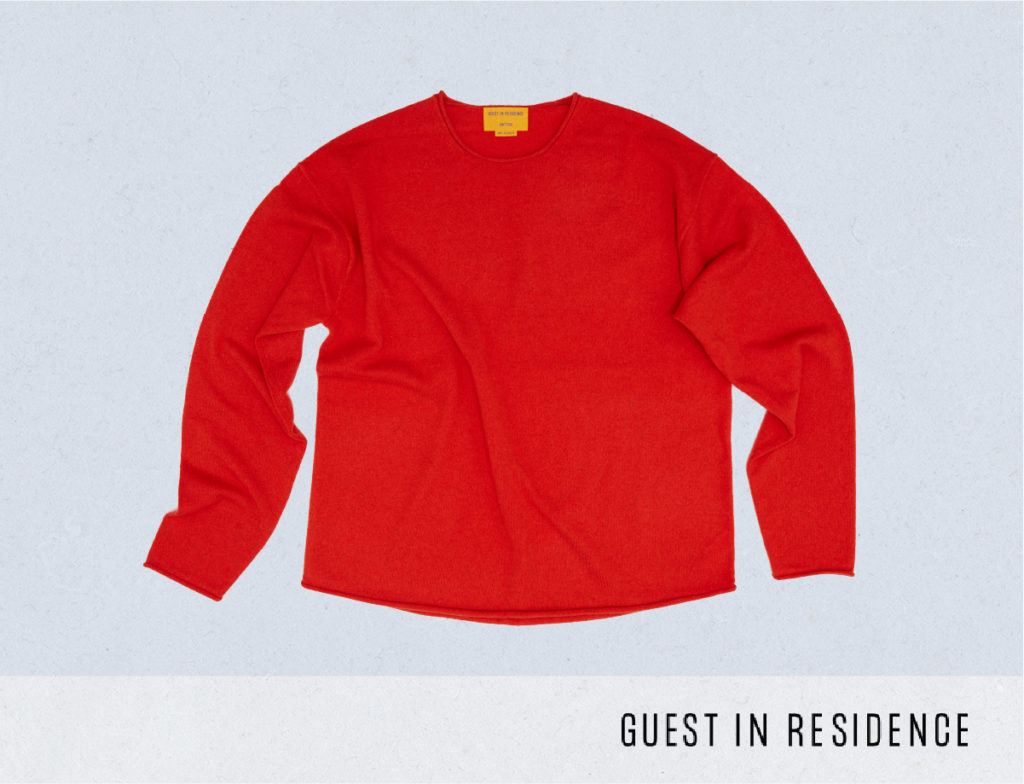
Unisex Oversized CrewÂ
Unisex oversized crew tee has a unisex fit to Men’s sizing, Women should size down for a less oversized fit. 100% Cashmere – Light-weight knit. Premium cashmere sourced from inner Mongolia, manufactured in China.
Miribel Naturals
Miribel Naturals is a natural, vegan, cruelty-free curly hair product brand. We focus on your hair health, rather than texture, so you can rock your natural born waves, curls, and coils.
The Hottest Miribel Naturals Gift This Holiday?
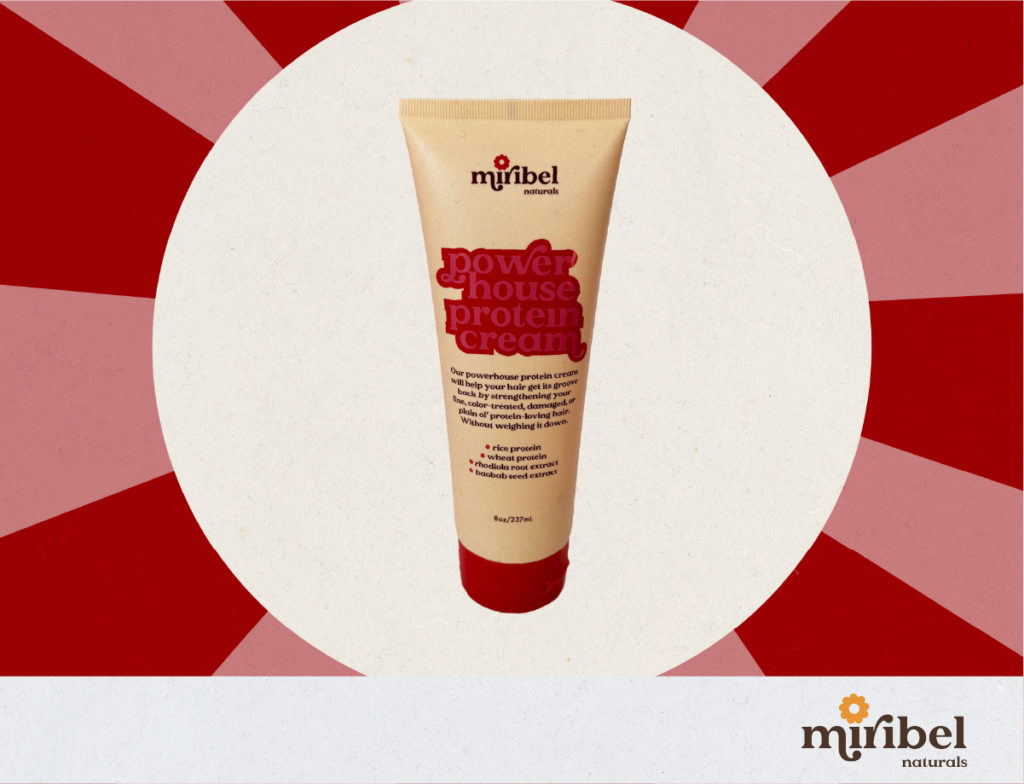
Powerhouse Protein Cream
If you’re a curly girl whose hair has seen better days, our Powerhouse Protein Cream is here to bring it back to life!
Add it to your line-up to restore strength and bounce to your hair with naturally sourced proteins. Reshape and condition your hair without ever weighing it so you can experience the true power of big bouncy, beautiful curls.
Ondo
ONDO socks use innovative fabrics traceable from seed to sewn, made with the highest-quality craftsmanship and committed to ethical manufacturing from suppliers with proven track records.
The Hottest Ondo Gift This Holiday?
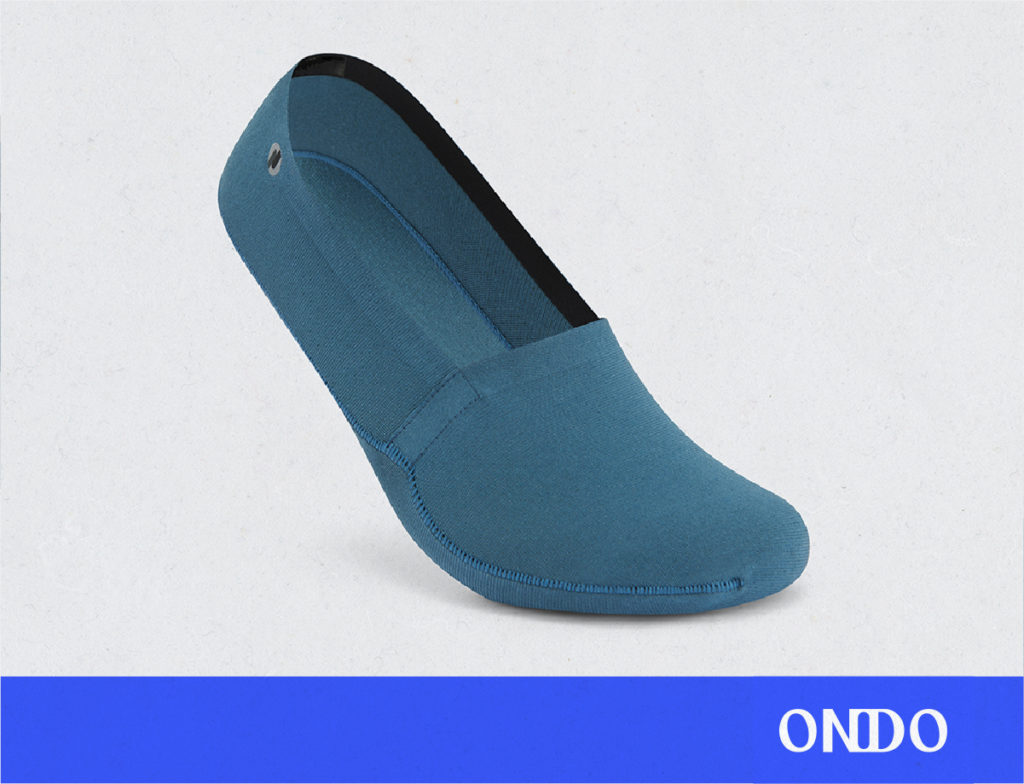
Organic Cotton No Show Socks
Made from a unique blend of certified organic cotton and innovative ‘aerolight’â„¢ fiber, our Organic Cotton No Show Socks are too good to show off. Literally. Comfortable yet low-cut to sit undetected, they’re the perfect union of fashion and function. ONDOs are available in five different sizes and offer unforgettable style for the discerning eye.
schleich
schleich® has over 300 toys in their assortment! A schleich® toy in a child‘s hand is an invitation into stories still unwritten. And we can‘t wait to hear the stories you‘ll tell!
The Hottest schleich Gift This Holiday?
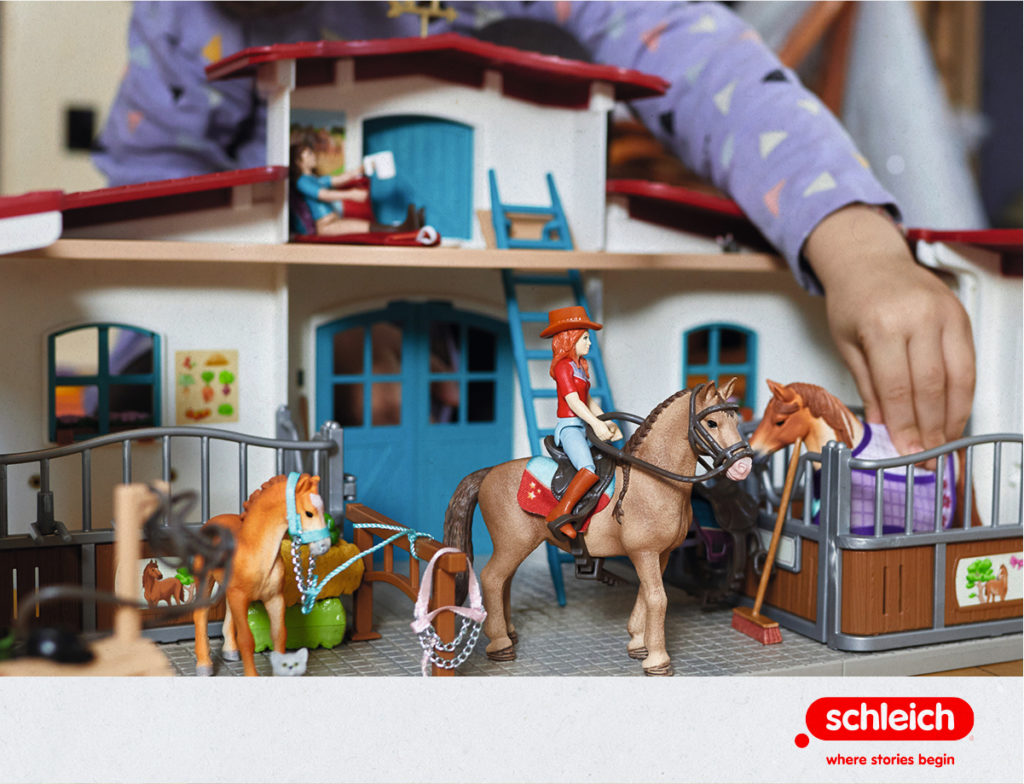
Horse Club Lakeside Riding Center
Yaaaaaawn! Wake up, sleepy head! While you’ve been snoozing in the loft, other equestrians at Lakeside Riding Center have been getting time in the saddle. Shimmy down the ladder and hurry to the stalls, where your horse is nibbling hay and waiting patiently. Ooooh, maybe after practicing your saddle gait you could take a trail ride to the Rider Café (playset sold separately) for a slice of fresh-baked apple pie! It’s gonna be a full day at Lakeside!
SodaStream
Create sparkling water experiences in the comfort of your own home. By transforming ordinary water into fresh sparkling beverages with the push of a button, SodaStream supports you to make better choices for yourself, your loved ones, and the planet.
The Hottest SodaStream Gift This Holiday?
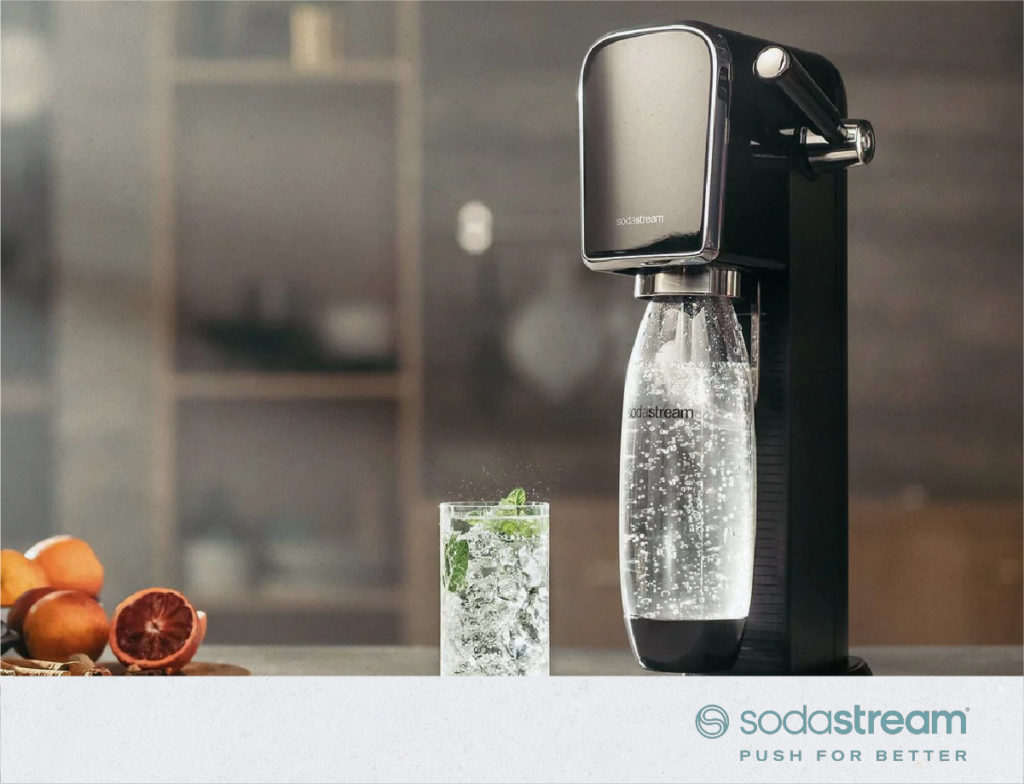
SodaStream Art
Sleek, sophisticated design with stainless steel accents that suits any kitchen. The carbonating lever and empowering new design makes it easy and fun to make fresh sparkling drinks more often with SodaStream Art. Featuring a dishwasher safe bottle and new Quick Connect technology for fast and easy CO2 cylinder insertion.
Wondery
We are Wondery! The outdoors are made for everyone. Our goal is to represent the vast diversity of woman identifying and non-binary individuals in our products, marketing, branding, advertising, events, and internally within our company.
The Hottest Wondery Gift This Holiday?
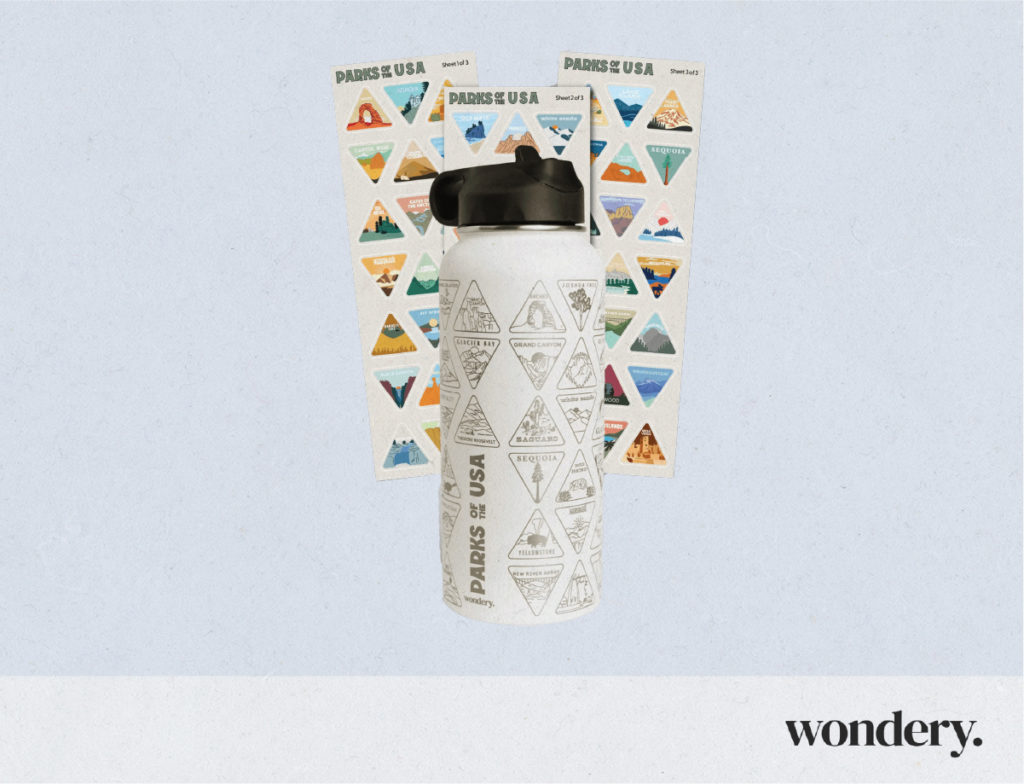
Parks of the USA Bucket List Water Bottle
Where have you traveled to? Our official Wondery Parks of the USA Bucket List Water Bottle keeps track of all your adventures and helps you stay hydrated.
We’ve designed unique depictions of your favorite parks in a beautiful laser engraving, along with vibrant corresponding weatherproof vinyl stickers that will be sure to strike conversation on the trail, at work, or in the classroom. What better to commemorate your journeys than crossing parks off your bucket list?
Holiday Shopping Starts Now
Whether you’re looking for the perfect gift or the perfect gift card, the time to start your holiday shopping is now! ShipHero is proud to work with these clients. Our Warehouse Management Software and Fulfillment Solution make it easier for eCommerce brands like these to ship eCommerce. We hope this list gives you a great jumpstart to your shopping this year.
For More Information About ShipHeroÂ
Whether you want to let go of running your own warehouse, or run your warehouse better, you can do both – and so much more – with ShipHero.

About ShipHero
ShipHero is a US-based, leading solution provider in the fast growing eCommerce fulfillment space. ShipHero served over $5 billion of eCommerce orders in 2020 and is growing rapidly. ShipHero provides warehouse management software for brands that operate their own warehouses as well as outsourced fulfillment as a service from ShipHero owned and operated North American warehouses. Some notable customers include Universal Music Group, Glossier and Canadian Tire. ShipHero is a Shopify Plus partner and more than 10% of Shopify Plus stores globally use ShipHero.
Follow us today on Twitter and LinkedIn.
Oct 7, 2022 | Blog
When was the last time you took a close look at your supply chain? If it’s been awhile, you might be costing your business money, as research shows that companies with optimized supply chains spend 15 percent less on related costs. Recognizing that supply chains play a key role in helping companies run smoothly, savvy owners and managers go above and beyond to provide on time delivery of products. However, in the wake of the COVID-19 pandemic, shortages and disruptions have proven to be the new normal of supply chains. If you want to stay competitive, it’s crucial to keep abreast of the latest customer spending habits and supply train trends while taking advantage of available tools and technologies.Â
Supply Chain Disruption in 2022 and Beyond
The forecast for supply chain disruptions in 2022 may seem less dismal than it did in 2020 and 2021. While the country has yet to recover completely from the COVID-19 pandemic and inflation remains at a record high, both consumer spending and employment levels are on the rise. Moreover, companies are no longer facing the pandemic-led supply shortages seen in the last two years.Â
Still, experts anticipate that a new problem may arise in the form of softening consumer demand. As the need for new merchandise drops, businesses may see economic growth slow while inventory piles up in warehouses. In particular, customers may be shifting their spending away from products and toward services, a trend that could pose a problem for a large sector of the business world.Â
Supply chain issues could also be impacted by the Great Resignation, which is seeing workers abandon their jobs in record numbers. Overall 48 million employees quit their jobs in 2021, with another 8.6 million leaving in the first two months of 2022 alone. The issue is particularly prevalent among workers in supply chain-related fields. If you rely on shipping, transportation or warehouse workers to get your products to market, it’s likely you’ll continue to see disruptions in the coming months.Â
How to Handle Supply Chain Disruptions
The good news is that companies are getting better at forecasting potential supply chain issues and adjusting their policies accordingly. Here are some ways to navigate US supply chain disruptions to keep your business competitive.Â
Get Flexible
Flexibility is key when it comes to surviving the ups and downs of the supply chain. One of the ways companies can manage supply chain disruptions in 2022 is to adopt elastic logistics practices. The ability to scale operations and resources depending on demand and shortages, elastic logistics is key to surviving the market fluctuations common post COVID. By incorporating new technologies, companies can better manage a range of issues from overstocking to route optimization.Â
Invest in AI
AI is one of the best solutions to the current supply chain issues. In particular, businesses can utilize predictive analysis tools to improve both visibility and operations. Research shows that more than half of businesses would like more supply chain visibility. Along with providing more transparency, artificial intelligence can help with data analysis, predicting demand, shipping routes, fulfillment and more.Â
Consider the Cloud
Cloud-based software is crucial for businesses hoping to simplify the fulfillment process. By adopting supply chain as a service models and outsourcing logistics and inventory management, companies can get their goods to clients faster and with less disruption. Not only can the cloud give supply chain managers an end-to-end view of the supply chain, but it also lets them access data from anywhere and share it with teammates. Additionally, software programs like the one available through ShipHero make it possible to reduce overhead by minimizing spending associated with infrastructure, maintenance and more.Â
Lessen Supply Chain Disruptions
Between continuing pandemic anxieties and unpredictable customer behavior, forecasting the future of the supply chain can be a challenge. Fortunately, your company can stay competitive by adopting the most up-to-date supply chain shortage solutions. Do your homework to give your business the best shot at success.
For more information about how ShipHero Fulfillment can help you manage the strain of supply chain disruptions, schedule a meeting with a member of our sales team today.Â

Maggie M. Barnett, Esq. COO of ShipHero
ShipHero
About the author: Maggie M. Barnett, Esq., is the COO of ShipHero. She is responsible for planning and executing the overall operational, legal, managerial and administrative procedures, reporting structures and operational controls of the organization. Barnett’s greatest strengths are leadership, risk mitigation, change management and a passion for business transformation. She is known for her expertise in delivering operational excellence and an ability to provide guidance and mitigating risk. Her leadership of ShipHero is grounded in a servant mentality, always doing the right thing for our stakeholders. Her passion for ShipHero comes from the ability to drive operational excellence throughout the organization impacting the lives of our employees, customers, and partners.
Follow Maggie on Twitter & LinkedIn.