Mar 24, 2023 | Blog, Fulfillment, Warehouse Management Software
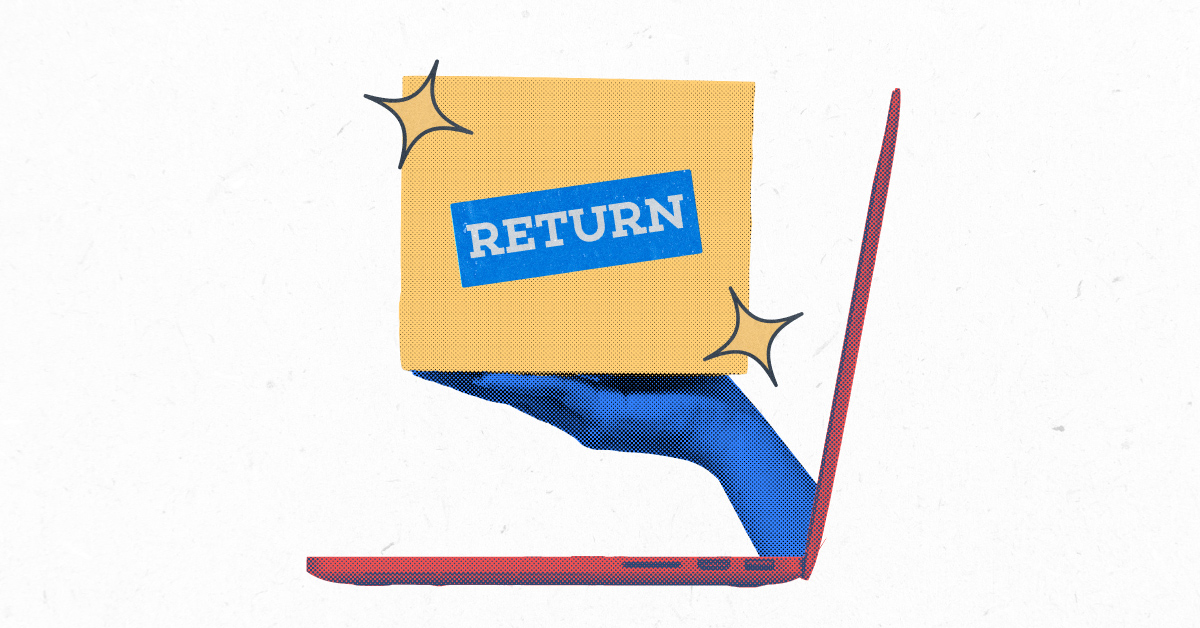
Modern eCommerce companies have revolutionized the game when it comes to returning items. From no-hassle pickups and convenient return windows, these businesses have made returns less of a dreaded task for customers looking to shop online. In this blog post, we’ll discuss some innovators in the space and how they’ve set themselves up for success with seamless processes that keep shoppers returning. Keep reading to learn more about how these companies are improving the return process and how you can too!
eCommerce Product Return Rate
Embracing returns can skyrocket second-chance sales, strengthen customer loyalty, and ultimately pump up your profits! Let’s dive into some fascinating eCommerce return stats showcasing how impactful returns can be on your business.
- The average eCommerce return rate is 16%.
- For every $100 in returned products accepted, online retailers lose $10.30 to return fraud.
- Fifty-eight percent of U.S. consumers make purchases with the intent to return.
- Ninety-two percent of customers will make another purchase if the returns process is easy.
- Offering free returns can boost conversions on high-ticket items by 17%.
- Eighty percent of consumers say returns are the most important factor when considering the overall order experience.
- Only 22% of shoppers said their most recent return experiences were easy.
eCommerce Return Reasons
The same survey found that three out of four consumers (76%) had returned an item they had just purchased. However, 78% of those surveyed felt the returns process was inconvenient. According to the survey, the top five reasons are:
- Return label not included in the shipping box (22%).
- Return shipping isn’t free (20%).
- Refunds take too long to be issued (19%).
- Lack of communication from e-tailer on return status (16%).
- Time and effort of dropping off returns with a mail carrier (13%)
Why are these return stats important? Well, it illustrates a few areas eCommerce companies can target when aiming to enhance their business strategies and seize every sales opportunity.
eCommerce Companies that Have Changed the Return Game
Chewy
Who would’ve thought: the pet store giving you paw-sitively excellent service? Chewy, one of the mascot stores of returning items stress-free, has a return policy of 365 days! They also meow-ve mountains to let you give that item to your pup’s buddies or donation sites.
Sure, most stores want customers’ happiness, but Chewy ensures their shopping experience meets their expectations with all the love a purring customer needs. After all, it’s so important for pet parents that their fur babies get the best.
Zappos
Unlike other online shoe companies, Zappos doesn’t cut corners when it comes to customer service! They already give their customers 365 days to return items for free, but their VIP program takes returns one step further with their Rapid Refunds benefit.
Zappos has become legendary for its speedy and simple return process by offering immediate refunds as soon as UPS scans the package. This makes the whole process a better experience and builds customer loyalty.
Casper (Mattress)
Casper has an excellent policy allowing customers to try their products confidently. Their generous 100-night trial allows customers ample time to decide whether they’ve made the right purchase.
Even better, Casper offers a thoughtful solution for customers wishing to return their products – donating them to a local charity instead of shipping them back. This way, their customers don’t need to feel bad about their decision.
How to Reduce Returns in eCommerce?
In today’s fast-paced retail world, companies have gone above and beyond to eliminate the dreaded ‘return anxiety’ by implementing transparent and painless return processes. They’ve created frictionless, convenient, and easy returns that appeal to customers, making returning a product less daunting. By utilizing these strategies, businesses save the sale and foster customer loyalty.
Emerging Trends
- Predictive analytics, for example, can empower businesses to pinpoint which products are most likely to be returned, allowing companies to address potential issues.
- Real-time data analysis can help tackle fraudulent returns and potential cyber threats, ensuring a secure shopping experience.
- AI-powered chatbots provide customers with instant support and guide them through the returns process more easily.
- Blockchain technology in the returns landscape grants increased transparency and accountability, offering peace of mind to all parties involved.
Embracing these innovative approaches will undoubtedly lead to reduced costs, improved efficiency, and an engaging and customer-centric return process.
Get Your Returns Game Up to Speed
From Chewy to Zappos, these companies have certainly changed the eCommerce returns game. Despite its higher costs, companies that focus on customer experience considerably reduce their return rates by offering an enjoyable user experience for unsatisfied customers. We can all learn from innovative eCommerce businesses prioritizing customer satisfaction above all else. Overall, managing product returns is not as difficult as it seems with the right strategies and innovations employed.
Mar 17, 2023 | Blog, Fulfillment, Warehouse Management Software
Are you running an eCommerce business and looking for ways to optimize reverse logistics? Look no further! We’ve got the perfect solution: 6 strategies that will help your business reduce costs, improve customer service, and create a more streamlined reverse logistics process. No matter the size of your business, these strategies can help ensure that customer returns go smoothly. Take a look at the 6 methods below to get started on optimizing your reverse logistics today!
#1 Improve Visibility
A savvy returns management team knows they can accomplish more tasks in less time when they have better visibility into their supply chain—ultimately producing fewer losses from those ever-pesky returned items. Having the right tools and procedures to improve visibility is one key to unlocking a more efficient reverse logistics system!
Seeing what’s coming back in the returns process should be a crystal clear, no-hassle event. Like smart labels on packages, understanding what arrives and from whom – can open the door to transparency.
That way, you’ll know ahead of time when to roll up your sleeves to adjust operations and better prepare for occasions when returns land on your doorstep. With a better view of the returned items, you can easily measure incoming volumes and stop the problems in their tracks!
#2 Streamline Processes
Returns can be a nightmare. But by streamlining the process and reducing the steps needed to handle them, you can make this tedious task go as smoothly as possible. After all, ensuring your customers are satisfied is always goal number one.
Streamlining returns processes is a great way to save time and money. With data-driven KPIs, businesses can quickly identify potential issues before they arise and make appropriate adjustments to reduce labor, costs, and other expenses associated with the process.
To increase efficiency even more, implementing supply chain strategies at the store level is the key to success – that way, you can see exactly what products need returning and where they need to be sent for maximum time and cost savings. Ensuring consumer triggers are noted allows companies to minimize future return instances, further reducing associated costs.
#3 Leverage Technology
Leveraging technology is critical to optimizing reverse logistics. After all, the most effectively executed processes involve communication, coordination, and automation – all of which can be facilitated via modern reverse logistics technology.
Automation and technology can help you find efficiencies that make a huge difference in how quickly your products return to your shelves. Plus, barcode scanning, RFID tracking, and automated sortation remove the guesswork while giving you immediate answers about each returned items’ where, when and why.
Connecting those processes related to forward logistics, reverse logistics, and inventory management will result in smoother transactions and a streamlined approach to eCommerce delivery. Tech helps your reverse logistics operations get smarter, so you can stay ahead of the game – and competition.
#4 Reduce Waste
Reducing waste through reverse logistics is not just good for the environment; it’s great for your business too! By implementing a waste reduction strategy, you can minimize your carbon footprint from returns and lower disposal costs.
Then, leveraging the five Rs of reverse logistics — returns, reselling, repairs, repackaging, and recycling — is an excellent way to optimize your process while cutting down on waste. Start by measuring your success in each department so you can establish goals for reducing losses. Connecting the dots between the 5 Rs and optimization is a surefire way to ensure your reverse logistics processes run smoothly.
#5 Improve Customer Experience
Everyone understands the frustrations of a poor return experience. That’s why optimizing reverse logistics ensures customers have a great experience when returning items.
Communication is vital – keeping customers in the loop throughout the process and setting manageable expectations. Simple notifications when the driver picks up the product, when their returns arrive at the service center, and when reimbursement has been paid will ensure transparency across your reverse logistics flow.
In addition, providing a convenient returns system with various options can eliminate any extra hassle and ensure they remain satisfied every step of the way. Put simply, take your returns one step further – after all, upgraded customer experiences are just one more way to keep your loyal customers coming back for more!
#6 Analyze Data
Data lets you read between the lines when it comes to reverse logistics. By closely scrutinizing what the numbers say, you can gain hints and tips on optimizing your returns process for maximum efficiency. Whether tracking volumes, timing out processing cycles or noting costs, data analysis helps you identify trends and improve your reverse logistics strategy over time.
Reverse logistics analytics can also help you do more than just manage returns – it can actively work to minimize returns and reduce fraud in the long run. By leveraging reverse logistics analytics to identify which items and reasons for return are most likely, companies can adjust their sales and forward logistics processes accordingly. Moreover, reverse logistics software helps companies verify the validity of returned items quickly; with reverse logistics analytics, fraudulent returns can become a thing of the past.
Unlock the Power of Successful Reverse Logistics
Despite the myths and misconceptions associated with reverse logistics, it is a process that has immense potential to optimize value creation. Ultimately, the strategies mentioned above allow businesses to save costs and create stronger customer relationships. From improving visibility to leveraging technology and reducing waste – companies can benefit from various advantages by investing in effective reverse logistics technologies and techniques.
With the right approach and an eye for detail, companies can use specific techniques to make the most out of their operations. So, if you are seeking to maximize your company’s bottom line while striving to achieve customer satisfaction, these 6 strategies can be beneficial in streamlining your reverse logistics processes. Subscribe to our blog for great tips on optimizing your reverse logistics today!

—
Aaron Rubin, Founder & CEO – ShipHero
About the author: Aaron Rubin is the Founder & CEO of ShipHero. He is responsible for planning and executing the overall vision and strategy of the organization. Rubin’s greatest strengths are leadership, change management, strategic planning, and a passion for progression. He is known for having his finger on the pulse of ShipHero’s significant initiatives, entrepreneurial spirit, and keen business acumen. His leadership of ShipHero is grounded in providing excellent customer service that drives improved business operations. His passion for ShipHero comes from the culture and his ability to impact the lives of employees, customers, partners, and investors.
Follow Aaron on Twitter & LinkedIn.
Mar 10, 2023 | Blog, Fulfillment, Warehouse Management Software
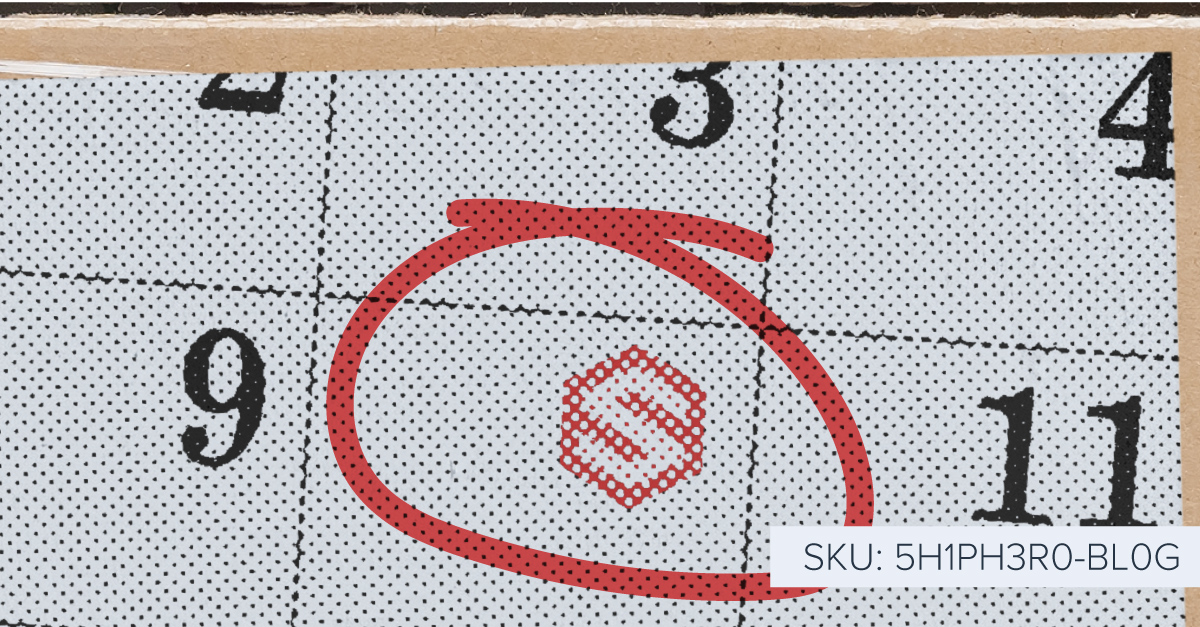
The end of the year is always a busy time for retailers, and with holiday shopping inevitably bringing more returns, there’s a lot to keep track of. Many eCommerce businesses and retailers carry over the hit on their inventory clear into Q3-Q4 of the following year, which can be detrimental to your business. Stop the vicious circle and make the most of Q1-Q3, so returns don’t have as much impact in Q4. Here are some tips on how to do just that.
Understand Returns
Understanding the various types of returns and their respective impacts on a store is crucial for any business looking to get ahead. You should consider what those returns might cost to process and complete a product return rate analysis to gain insight into customer behaviors and quality control issues.
Then, looking beyond just percentages of gross demand, it is essential that all areas that could have an influence on return rates – such as inaccurate content, damage in transit, picking errors, and supplier QA problems – be accounted for and actively managed. After all, with each return comes a chance to learn more about customers and products.
Crunching the numbers on returns can be enlightening – not just for you but for your customers, too. If you find the cost of handling the returned item is bordering on the price of creating another product or procuring one from a distributor, issuing an easy refund and keeping the original item may be a smart play.
The “Just Keep It” return policy sounds almost too good to be true for consumers who get their money back and get to keep the product. But that’s exactly what happens. Instead of piling returned merchandise onto the growing inventory heap, stores are considering just handing customers their money back and letting them hang onto the product. Some retailers advise customers to just keep or donate their return after issuing a refund.
Planning Ahead
As you look ahead to Q4, one of the smartest moves you can make is to plan for what you want to accomplish in Q1-Q3. No matter how prepared you think you are, things can get hectic when the end of the year rolls around and the holiday season kicks into high gear.
Planning your operational activities now will help your team optimize and handle customer returns in Q4. As you plan for key dates, such as holidays, you can reduce future returns by planning your inventory needs.
Returns can be more expensive than orders, so minimizing those costs over time is important. You can use simple strategies like a more detailed product description or updated product photos. Taking proactive steps ahead of this year’s holiday season will ensure a smoother experience. Part of planning ahead could include the following steps:
Establish a Clear Return Policy
A clear return policy empowers customers to make informed decisions and shop confidently. This is because they know that if their purchase doesn’t fit just right, they will be able to get their money back.
By combining this transparent policy with insights into how often customers return items, you can tweak your strategy as needed – allowing shoppers to benefit from the right balance of affordability and quality. So look under the hood of your return policy today and ensure it’s optimized for maximum customer satisfaction.
Educate Your Employees
When it comes to refunds, educating employees is a must! After all, they are the ones dealing with customers and helping them get what’s owed. Knowing common types of returns and their potential pitfalls can help keep the process hiccup-free – leading to happy customers and satisfied employees. Investing in excellent customer service ensures that refunds are handled with friendliness, quickness, and accuracy so customers don’t feel let down by their experience or discouraged from shopping again.
Add Automation
No business enjoys processing returns, but it doesn’t have to be a chore. You can save time and energy by using an automated return management system. With these systems, labels are generated, items are tracked, and data is easily stored; the whole process is basically automated.
Automation can be a game changer for returns processing. Enabling faster, more accurate data capture and freeing up customer service teams to handle more pressing issues. Additionally, automation makes customers feel supported throughout their journey with packing, shipping, and tracking updates.
By removing manual administrative tasks, retailers and customers are more likely to communicate effectively, improving loyalty and lifetime value. The earlier you implement automation, the greater the chance of saving time and effort and preventing errors. So, come Q4, your returns won’t come back to haunt you since your data and inventory are updated.
Manage Inventory and Forecasting
There is no doubt that planning ahead of the holidays can make a big difference between your business’s success and failure during peak season. Keeping an eye on inventory levels is one of the most important things you can do to weather peak periods with the least disruption people.
Any sudden change in demand or return items will cause an even more significant snowball effect that will be hard to reverse. It doesn’t take a crystal ball to see out into the future, but it does take vigilance and a bit of savvy forecasting to do so. The more you prepare for the season, the more likely you will stay ahead of the competition.
Consider Reverse Logistics Services
Third-party logistics providers (3PL), like ShipHero, provide software and automated tracking that goes beyond a typical WMS. When it comes to handling your returns like a pro, ShipHero’s open API and tracking capabilities offer limitless possibilities.
You can rest easy knowing that Q4 won’t be a fright fest by having seamless integration with leading eCommerce and vendors. There’s no denying that returns present certain challenges, but with ShipHero, you get a warehouse management system that can adapt to these changes quickly.
Time to Get a Head Start
It is a great time to get a head start on your Q4 financial results in Q1-Q3. If you plan carefully, understand returns, educate your customers, automate, and keep an eye on inventory, you can minimize any impact from returns in Q4. Keep these tips in mind to ensure your business remains profitable and successful all year long.

Mar 3, 2023 | Blog, Fulfillment, Warehouse Management Software
In eCommerce and retail, reverse logistics can be a complicated concept to wrap your head around. But understanding this process isn’t just crucial for warehouse managers—it’s absolutely essential! To show you how easy it is to get into gear with reverse logistics, we’ve crafted this comprehensive guide full of helpful tips, tricks, and advice on everything from streamlining returns to optimizing inventory flow. Read on if you’re ready to make reverse logistics work in your favor!
In eCommerce, returns aren’t just about the refund – it’s also about how long it takes to process those items. With labor shortages, retailers are feeling the pinch more than ever. According to eCommerce statistics gathered by the National Retail Federation and Appriss Retail, return merchandise was worth a whopping $816 billion last year – without any change in the average rate of return of 16.5%. But don’t panic just yet! Investing in a WMS (Warehouse Management System) for reverse logistics can help warehouse managers separate physical returns from accounting while contributing to sustainability and financial health.
What is Reverse Logistics?
Reverse logistics sounds like a spaceship’s reverse engineering, but it refers to the work done after something has been sent out for consumption. So when you return that shirt you never wore, dispose of some sort of electronic device, get things repaired and shipped back, or recall products due to an issue – that’s what reverse logistics is all about. It’s what happens when something goes awry between point A (source) and point B (consumption).
Whether it’s eCommerce returns solutions or something else, reverse logistics helps companies make the most out of what they do not want – by recovering resources to maximize worth and minimizing the environmental costs associated with returned products and materials. It can also delight customers by providing satisfying exchange and return options due to its efficient nature.
How Reverse Logistics Works
Reverse logistics is vital to the success of eCommerce returns. The process includes multiple steps, with careful planning and coordination necessary to maximize efficiency and minimize costs. Despite its complexity, it offers a great opportunity for businesses to cut costs while improving customer satisfaction and brand loyalty. The general steps in reverse logistics are:
- Product Returns: Getting returned products from customers or retailers is the first step in reverse logistics. Returns are then categorized by condition, the reason for return, and destination.
- Inspection and Assessment: Following the return of products, they are inspected and assessed to determine whether they can be resold, refurbished, recycled, or disposed of. By identifying the value of returned products, you can choose how to handle them.
- Refurbishment and Repair: Generally, if returned products need minor repairs or refurbishment, they can be repaired and made ready for resale or reuse. In this step, the products are repaired, cleaned, and repackaged to make them sellable again.
- Recycling and Disposal: Recycling or disposing of returned items may be necessary if they are damaged, expired, or unsellable. During this step, the products are separated into different waste streams and disposed of responsibly.
- Logistics and Transportation: Logistics providers can coordinate with repair centers, recycling facilities, or resale channels to ensure the products are delivered to the appropriate locations.
Types of Reverse Logistics
There are several types of reverse logistics, each designed to handle a specific aspect of the product lifecycle and recover value from returned products. Some common types of reverse logistics include:
- Returns Management: In this process, we handle returns from customers or prevent returns from happening in the first place.
- Return Policy and Procedure (RPP): RPPs are the policies about returns a company shares with its customers.
- Remanufacturing or Refurbishment: Remanufacturing, refurbishing, and reconditioning involve repairing, rebuilding, and reworking products.
- Unsold Goods: For unsold goods, reverse logistics handles returns from retailers to manufacturers.
- End-of-Life (EOL): EOL means a product is no longer useful, doesn’t work, doesn’t meet a customer’s needs, or is replaced with a newer version.
- Delivery Failure: Whenever a failed delivery occurs, drivers return the product to sorting centers, who then return it to the source.
5 Rs of Reverse Logistics
The 5 Rs are principles that help businesses maximize returned products’ value while lowering supply chain waste. By following them closely, companies can recover assets from formerly unusable goods and reduce the environmental impact on our world! Let’s dive into each one.
- Returns: Managing product returns includes issuing return authorizations, receiving and inspecting returned products, and managing the reverse flow of products.
- Recalls: Due to government regulations, recalls are often a more complex way to return products.
- Refurbishment: Refurbishing means repairing, cleaning, and repackaging products. It extends product life, reduces waste, and recovers value.
- Repackaging: What happens when customers return products because they’re unhappy with them, not because they’re defective? Usually, repackaging the product will allow it to be resold.
- Recycling: A recycling process takes old products and recovers raw materials. The process involves separating and processing products into their constituent materials, which are then used to manufacture new ones.
Reverse Logistics Examples
Reverse logistics are an ever-present force in many industries, offering clever solutions to secondhand parts and products. Take retail, for instance; when products are returned, reverse logistics allow companies to resell, refurbish, and recycle them. Electronics and automotive fare similarly – the former has remanufacturing and refurbishing at the ready, while the latter’s reverse logistics often take the shape of remanufactured auto parts.
In the food sector, reverse logistics use waste to create compost and animal feed. As for healthcare, reverse logistics may take back unused or expired medications from pharmacies, and apparel companies reclaim used clothing for resale, renovation, and recycling.
Importance of Reverse Logistics to your Business
Reverse logistics are proving to be an invaluable approach in business today. By taking a mindful second look at the supply chain, companies can reduce waste while improving operations and sustainability – giving their bottom line the boost it deserves.
- Cost Savings: Businesses can recover value from returned products with reverse logistics, reducing return, disposal, and replacement costs.
- Environmental Sustainability: Companies can reduce and improve their carbon footprint by implementing effective recycling and refurbishment processes with reverse logistics.
- Customer Satisfaction: By facilitating the efficient return and replacement of products, reverse logistics can improve customer service, satisfaction, and brand loyalty.
- Competitive Advantage: A well-developed reverse logistics strategy can give your company a competitive edge.
- Regulatory Compliance: Reverse logistics can help companies comply with regulations related to the disposal of hazardous materials, the handling of electronic waste, and other environmental regulations.
Returns are Costing you – Save with ShipHero.
Reverse logistics doesn’t have to be a daunting task. A comprehensive, well-integrated WMS can significantly benefit companies looking to minimize their environmental costs while maximizing the value of their returned products. Handling the physical and accounting processes separately is key as it reduces time and improves efficiency for warehouse managers and customers.
When considering a WMS explicitly designed for reverse logistics, look at ShipHero. Leveraging a powerful cloud-based system, ShipHero can simplify your reverse logistics operations and get you one step closer to success. So if you’re ready to upgrade your WMS to ShipHero, don’t hesitate – let’s make something great happen together!
Subscribe to our blog to learn more, or Click HERE to Schedule a Meeting Today!
—
Aaron Rubin, Founder & CEO – ShipHero
About the author: Aaron Rubin is the Founder & CEO of ShipHero. He is responsible for planning and executing the overall vision and strategy of the organization. Rubin’s greatest strengths are leadership, change management, strategic planning, and a passion for progression. He is known for having his finger on the pulse of ShipHero’s significant initiatives, entrepreneurial spirit, and keen business acumen. His leadership of ShipHero is grounded in providing excellent customer service that drives improved business operations. His passion for ShipHero comes from the culture and his ability to impact the lives of employees, customers, partners, and investors.
Follow Aaron on Twitter & LinkedIn.
Feb 24, 2023 | 3PL Warehouse Management, Blog, Fulfillment
Are you looking for an innovative way to increase revenue without creating excessive workloads for yourself and your team? White-glove fulfillment might be the answer! But what is it, and more importantly, how can you manage white glove fulfillment services at scale? Don’t worry – this blog has all the answers you need. From finding your niche in the industry to earning a good return on investment, this blog provides guidance on incorporating white-glove fulfillment into your current business model.
Organizational Efficiencies: Do You Have Enough Warehouse Space?
Ensuring that your orders are well taken care of is important, which is why white glove service needs extra attention. Stocking items like bubble wrap or foam inserts can take up more space in the warehouse than standard packing requirements. Consider setting up a special packing station specifically for white glove orders to avoid any mix-ups and help maintain employee efficiency. It’s all about finding the right organizational balance – with great planning, you can achieve the perfect combination of space and order accuracy.
Having the right workflow for packing is essential, and it will be important to assess the available warehouse space to ensure there is enough room for all your packing needs. The volume, type of products, and size of the packing station must be considered carefully so that you have one-touch efficiency when organizing items for shipping. Streamlining this process can help keep errors down while promoting a faster throughput, so it’s worth taking the time to get organized and find the most efficient way of packing for your white glove service. To optimize your packers’ workflows, start by considering all the factors in play and create a plan that works best with your goals and resources.
Having warehouse managers adept in their Tetris skills can be beneficial when optimizing space through reorganizing. With the right tools and dedicated stations for white glove packing needs, it will be much easier to manage it all.
Employee Efficiency: Can you Designate a White Glove Packer?
Keeping an eye on employee efficiency in white glove packing ensures your warehousing operations are profitable. Designating the right person or persons for this type of job will pay off in the long run, as white-glove packing can sometimes take a bit longer – and you don’t want to lose time! Finding out who your best packers are and giving them the responsibility of handling white glove shipments is a great way to ensure that they are efficient while keeping costs low.
As any 3PL company knows, time is money. When it comes to efficiency, wasting time on something like creating a single order kit can add up quickly. The need to repeatedly go back and forth across the warehouse over and over again takes valuable moments away from getting packages ready and out the door. Time wasters such as this are one of the many reasons why efficiency tracking should be taken into account when evaluating your operations.
The second reason why white glove fulfillment may slow you down is that, since items involved with white glove services must remain as unscathed as possible, the picking and packing process needs to be done in a way that ensures minimal touches. That’s why creating a warehouse space specifically tailored for such tasks can be incredibly beneficial.
Having an efficient packing process can make all the difference when it comes to streamlining your warehouse. Having a designated “white glove packer” could be beneficial in optimizing your workflow, as they can assess and select the proper shipping supplies for each product. Investing in packing items designed to make their job easier, like conveyor belts, can save time and make every process smoother. By getting products closer to the packer or relocating finished packages to a staging area for shipping, you can help get products out on time!
Automation Rules: Can your WMS Support White Glove Fulfillment?
Managing white glove fulfillment at scale requires more than just a strong team – you need a warehouse management system that can support it, too! When managing white glove items, your WMS should be able to separate them from your regular processes so they don’t get mixed up or slow down your workflow. To do this successfully, you’ll want to look for an automated solution that allows you to provide “special projects” like white glove fulfillment with the speed and precision it deserves. That way, you are sure your team and customers will have a seamless experience every time.
Automation and your WMS should be integral to any white glove fulfillment setup. Automated rules are a great way to streamline the logistics process, allowing you and your team to focus on providing that extra-special care associated with white glove fulfillment. Automating these processes also makes it easier for you to keep track of all the fine details that can easily get lost in manual processing, simplifying everything with one-touch ease.
Examples of White Glove Fulfillment
White glove fulfillment is becoming increasingly popular for businesses that are aiming to give their customers an unforgettable unboxing experience. It requires a lot of planning and attention to detail, but when done right, it can be a fantastic way to bring in repeat business. White glove fulfillment solutions involve custom packaging and extra touches like branded swag or personalized notes that help boost the customer’s satisfaction. In addition, this approach adds extra value that leaves a lasting impression, encouraging customers to return for more. A successful white glove service can set your business apart from your competition and maximize customer loyalty.
Delivering large or fragile items to customers can be a complicated task – it takes special packaging and attention to detail, so it’s no wonder why more and more businesses are turning to white-glove fulfillment when it comes to these projects. The extra expense is worth it for the clients because receiving their purchases in perfect condition will keep their customers happy and coming back for more.
Are you Ready to Scale your Fulfillment?
Scaling your 3PL services can be a big undertaking for businesses needing more than just regular order fulfillment. It’s important to take the time to consider the overall efficiency of your warehouse, pickers, and customers when looking at growth opportunities. Streamlining and building up specific operations that work best with your current and future clients may be the most beneficial approach toward expanding naturally. You know what works best for you and your company, so why not explore the options available? From consolidating orders professionally or finding solutions that elevate the customer experience through specialized services, there are many paths forward that can help take your business to the next level!

—
Maggie M. Barnett, Esq. COO of ShipHero – Author
About the author: Maggie M. Barnett, Esq., is the COO of ShipHero. She is responsible for planning and executing the overall operational, legal, managerial, and administrative procedures, reporting structures, and operational controls of the organization. Barnett’s greatest strengths are leadership, risk mitigation, change management, and a passion for business transformation. She is known for her expertise in delivering operational excellence and her ability to provide guidance and mitigate risk. Her leadership of ShipHero is grounded in a servant mentality, always doing the right thing for our stakeholders. Her passion for ShipHero comes from the ability to drive operational excellence throughout the organization impacting the lives of our employees, customers, and partners.
Follow Maggie on Twitter & LinkedIn.